Цинк покрытие: суть покрытия, как оцинковать своими руками – Свойства цинкового покрытия и область применения
Свойства цинкового покрытия и область применения

Цинковые покрытия являются достаточно эластичными и хорошо выдерживают развальцовку, изгибы, вытяжку. Свежеосажденный цинк хорошо паяется с применением бескислотных флюсов; для пайки цинковых покрытий, находившихся на воздухе длительное время, необходимы активные флюсы.
Цинк относится к весьма активным металлам, легко реагирующим с кислыми и щелочными растворами. В паре с железом, имеющим более положительный потенциал, цинк является анодом, поэтому в результате коррозионных процессов, происходящих на поверхности оцинкованных деталей под действием влажного воздуха, растворяется цинк, а не основной металл. Коррозионный процесс, происходящий по такой схеме, является более благоприятным, чем в случае катодных покрытий, например никель по стали, так как разрушение основного металла практически не происходит до тех пор, пока сохраняется цинковое покрытие. На поверхности цинка в атмосферных условиях влажный воздух, содержащий углекислый газ, сернистые соединения и тому подобные вещества, обусловливает образование светло-серых продуктов коррозии в виде тонкого слоя гидроокиси цинка Zn(OH)
В промышленной и приморской атмосферах в состав продуктов коррозии входят также хлориды и сульфаты цинка. Скорость коррозии цинкового покрытия по мере накопления на поверхности продуктов коррозии уменьшается в результате частичного заполнения пор в покрытии. Таким образом, пленка из продуктов коррозии толщиной до 20 мкм служит своего рода дополнительной защитой.
Анодный характер цинка по отношению к стали обусловливает возможность защиты оголенных участков поверхности, отстоящих па расстоянии нескольких миллиметров от кромки покрытия. Забоины и царапины в покрытии не влияют существенно на коррозию изделий. Протекторное действие цинка обусловливает также защиту от коррозии непокрытой резьбы гаек, если они навинчены на оцинкованные болты, срезы листовых оцинкованных материалов, проволоки и т. п.
В некоторых случаях цинковое покрытие принимает катодный характер защиты по отношению к стали, например при воздействии горячей воды (температура выше 70° С), в результате происходит весьма интенсивная коррозия стали, а цинковое покрытие не разрушается.
Защитное действие цинкового покрытия резко ослабляется в атмосфере, содержащей продукты органического происхождения: синтетические смолы, олифу, хлорированные углеводороды и т. п. вещества. Цинковые покрытия разрушаются, если они находятся в контакте или в одном и том же закрытом объеме со свежеокрашенными и промасленными деталями. Для повышения химической устойчивости цинка при воздействии агрессивной атмосферы его поверхность подвергают специальной химической обработке в растворах, содержащих хромовую кислоту или ее соли, при этом в результате реакции образуются пленки хроматов цинка, значительно улучшающие коррозионную устойчивость покрытия. Устойчивость достигается также обработкой оцинкованных деталей в растворах, содержащих соли фосфорной кислоты. Эта операция называется фосфатированием.
Высокие защитные свойства цинковых покрытий, обусловленные анодным характером этого покрытия и низкой стоимостью цинка но сравнению с другими цветными металлами, обусловливают широкое распространение процесса цинкования в различных отраслях промышленности. Цинковые покрытия составляют более 60% всех видов металлических покрытий, применяемых в народном хозяйстве. Цинкованию подвергаются листы кровельного железа, трубы, каркасы, шасси радиоприемников, детали автомобилей приборов, станков, сельскохозяйственных машин, крепежные детали, проволока и другие изделия массового производства.
Толщина цинкового покрытия на деталях устанавливается в зависимости от условий эксплуатации изделий, а также условий сопряжения деталей при сборке. Выбор толщины покрытия производится в соответствии с ведомственными нормами, отраслевыми стандартами и другой нормативно-технической документацией.
Таблица 1. Толщина цинкового покрытия.
Характеристика ycлoвий экслуатации |
Толщина, мкм |
Обозначение по ГОСТ 9791-68 |
Легкие условия (ЛС). Отапливаемые и вентилируемые помещения. Относительная влажвость 65 ± 15 % при температуре 25° С. |
6 — 9 |
Ц 6 |
Средние условия (СС). Отсутствие атмосферных осадков, неотапливаемые помещения, атмосфера загрязнена небольшим количеством промышленных газов. Температура воздуха от -60 до + 60° С, относительная влажность 95 ± 3 % при температуре +30° С. |
15 — 18 |
Ц 15 хр |
Жесткие условии (ЖС). Эксплуатации на открытом воздухе. Воздействие атмосферных осадков, загрязненных промышленными газами. Относительная влажность 95 ± 3 % при температуре +35° С (тропические условия). |
24 — 30 |
Ц 24 хр |
Эксплуатация в особых условиях. Длительное пребывание в воде. Атмосфера насыщена промышленными газами. |
36 — 42 |
Ц 36 хр |
В табл. 1 даны рекомендации по выбору толщины цинкового покрытия в зависимости от условий эксплуатации и приведено обозначение цинкового покрытия на чертежах деталей. При выборе толщин покрытия для мелких резьбовых крепежных деталей необходимо учитывать условия свинчиваемой, поэтому толщина слоя цинка на резьбовых деталях с шагом до 0,8 мм устанавливается 3 — 6 мкм для деталей с шагом более 0,8 мм — 9 -18 мкм.
Необходимо также принимать во внимание, что если деталь находится внутри прибора и защищена кожухом от попадания влаги, а при работе прибора выделяется теплота, то условия эксплуатации детали являются менее жесткими, чем условия эксплуатации изделия.
Цинковые покрытия бывают от серого до светло — серого цвета. При длительном хранении оцинкованных деталей допускается потускнение поверхности. Образование осыпающегося белого налета на цинковом покрытии ухудшает его внешний вид, но не снижает защитных свойств.
Для цинковых покрытий, подвергнутых хроматированию, цвет — от золотисто — желтого до желтовато — зеленого с радужным оттенком. Коричневый цвет пленки не допускается. Отсутствие хроматной пленки в порах и раковинах литья, в швах сварки и около них, вблизи щелевых зазоров и малых отверстий допускается. Нарушение хроматной пленки в виде отдельных рисок и точек тоже допускается. Цинковое фосфатированное покрытие имеет цвет от светло-серого до темно-серого с явно выраженной кристаллической структурой фосфатной пленки. Основные физические свойства цинка представлены ниже:
Плотность, г/см3 — 7,1
Температура плавления, °C — 420
Твердость электролитического цинка, кгс/мм2 — 50 — 60
Электрическое сопротивление, Ом*см — 5,75*10-8
Цинк-ламельное покрытие: революция в антикоррозионной защите
Ежегодно 10% производимых металлов приходит в негодность из-за ржавчины, что оценивается десятками миллиардов долларов. Это сопоставимо с годовым объёмом продукции крупного металлургического завода. Сберечь оборудование и избежать убытков поможет антикоррозионная защита металла.
Виды антикоррозионной защиты
Существует два основных вида антикоррозионной защиты:
- Легирование. В обычную углеродистую сталь добавляют различные легирующие элементы: хром, никель, молибден, титан, бор и другие химические элементы, препятствующие окислению металла. В результате получаются стали со множеством специальных свойств. Наиболее распространённый вариант для крепежа – это нержавеющие аустенитные стали марок А2 и А4.
- Антикоррозионное покрытие металла. На изделии создаётся барьерный слой, устойчивый к воздействию окружающей среды. Для этого используется краска, лак, эмаль, оксидная плёнка или металл – хром, никель, кадмий, а чаще всего цинк. Покрытие крепежа цинком или его сплавом называется цинкованием (оцинковкой) – это наиболее популярный и доступный способ защиты металлических изделий от ржавчины.
Типы цинкования
Самые популярные типы цинкования – гальваническое, горячее и термодиффузное и цинк-ламельное.
- Гальванический способ – это цинкование путём электролиза. Даёт наименее стойкое покрытие толщиной 4–20 мкм, не рассчитанное на жёсткие условия эксплуатации, из-за чего этот вид покрытия ещё называют декоративным. Выдерживает внешние воздействия класса С1. Из плюсов – яркий металлический блеск деталей (привлекательный внешний вид), низкая цена и возможность точно дозировать толщину покрытия. Из минусов – опасность водородного охрупчивания при гальваническом цинковании высокопрочных сталей (на крепеже класса прочности выше 8.8) и грязное с точки зрения экологии производство.
- «Горячее» цинкование – оцинковка металла путём окунания в ванну с расплавленным цинком при температуре около 460 °C. Простой, недорогой и надёжный способ нанесения защитного покрытия. Толщина цинкового слоя составляет 40-60 мкм, что позволяет выдерживать нагрузки классов С3 и С4.Главное достоинство – высокие антикоррозийные свойства (изделие прослужит до 50 лет). Даже при появлении царапин или сколов на поверхности защитные свойства покрытия будут препятствовать образованию ржавчины. Недостатком технологии является неравномерность толщины покрытия (наплывы цинка достигают 1 мм). Из-за этого её нельзя использовать для защиты деталей, требующих высокой точности изготовления (нельзя применять для крепежа меньше М8). В результате «горячего» цинкования детали получаются матовыми, без металлического блеска.
- Термодиффузное цинкование (шерардизация) – насыщение верхнего слоя металлического изделия цинком (термодиффузный слой). Достаточно сложная и дорогая технология нанесения защиты. Производится в разогретых вращающихся центрифугах с цинковой пылью. Температура в контейнере достигает 290–450 °C. Шерардизация позволяет получить толщину покрытия в диапазоне от 6 до 110 мкм, причём покрытие образуется ровное и беспористое, с высокой адгезией к подложке. Защитная способность такого покрытия в 3–5 раз выше, чем у гальванического, и сравнима с горячецинковым. Этот способ используется для защиты металлопродукции специального назначения, например, для деталей железнодорожного транспорта. К минусам стоит отнести небольшую производительность, лимитируемую объёмами камер для цинкования, ограничение размера деталей размером контейнера и отсутствие декоративных свойств у диффузионного покрытия (серые тона, отсутствие блеска).
Свойство/вид покрытия |
Гальваническое цинкование |
Горячее цинкование |
Термодиффузионное цинкование |
Цинк-ламельное покрытие |
Толщина |
5–12 мкм |
55–85 мкм |
6–110 мкм |
4–20 мкм |
Стойкость в соляном тумане до появления коррозии |
24–96 часов |
450–850 часов |
До 1500 часов |
Более 2000 часов |
Достоинство метода |
Позволяет обрабатывать детали сложной формы из тонкого металла, позволяет наносить покрытие на металл после операции сварки |
Высокая коррозионная стойкость, для крупных деталей – высокая скорость нанесения покрытия |
Мощная коррозионная защита и высокая адгезия к подложке (сцепление слоёв). Тонкий слой покрытия |
Высочайшая коррозионная стойкость. Простота нанесения на детали сложной формы. Мягкие требования к толщине материала базы. Отсутствие водородного охрупчивания на высокопрочных изделиях. Высокая стойкость к перепадам температур и воздействию химикатов |
Недостатки |
Низкая коррозионная стойкость, длительное время нанесения покрытия, высокие требования к подготовке поверхности |
Требования к минимальной толщине детали во избежание коробления вследствие высокой температуры при нанесении, сложность покрытия деталей средних и малых размеров |
Небольшая производительность; ограничение размера деталей, на которые наносится покрытие; дороговизна и сложность технологии |
Высокие требования к подготовке поверхности. Необходимость операции спекания в сушильном шкафу, что затруднительно для крупногабаритных деталей |
Цинк-ламельное покрытие
Лучше всего из перечисленных видов цинкования от коррозии защищают «горячее» и термодиффузное. Однако у них есть недостатки: сложная и дорогая технология нанесения либо ограничения в типах и размерах деталей, которые покрываются цинком.
В 70-е годы прошлого века, когда развитие промышленности и строительства потребовало новых решений, инженеры стали искать альтернативные виды антикоррозионной защиты – технологически простые и максимально эффективные. Тогда в США разработали и запатентовали новую систему покрытия – цинк-ламельную. При малой толщине слоя (6-12 мкм) данное покрытие обеспечило высокую степень антикоррозионной защиты. Также эта технология препятствует охрупчиванию металла под воздействием водорода.
Свойства
Цинк-ламельное покрытие содержит до 80% цинковых чешуек (ламелей), 10% алюминиевых и связующую основу (акриловые, уретановые, эпоксидные и кремнийорганические смолы). Микроскопические чешуйки расположены параллельно, поэтому перекрывают друг друга, не оставляя «пробелов» на металлической поверхности, куда мог бы попасть кислород. Кроме того, скорость окисления алюминия ниже, чем цинка, поэтому цинк-алюминиевое покрытие в 3 раза устойчивее к коррозии, чем стандартное горячеоцинкованное покрытие.
Цинк-ламельное покрытие можно наносить не только на чёрный металл, но и на оцинкованную сталь, никель, алюминий, медь, нержавеющую сталь и другие металлы. При необходимости на базовое покрытие наносятся дополнительные слои, которые повышают коррозионную и химическую устойчивость, придают нужный цвет и увеличивают износостойкость.
Преимущества цинк-ламельного покрытия
Высокая коррозионная защита (более 2000 часов в камере соляного тумана до появления ржавчины)
Стойкость к перепадам температур
Высокая стойкость к воздействию химикатов
Контролируемый коэффициент трения, который позволяет регулировать момент затяжки
Отсутствие водородного охрупчивания на высокопрочных изделиях
Заданная электропроводность
Экологичность (отсутствие вредного шестивалентного хрома)
Широкая цветовая гамма
Надёжность в резьбовых соединениях
Способы нанесения покрытия
- Распыление. Материал наносится на поверхность подготовленных деталей с помощью пистолета-распылителя вручную или на автоматизированной установке. Размер деталей ограничивается только возможностями условий подготовки и дальнейшей термообработки.
- Погружение с центрифугированием. Детали загружаются в контейнер с покрывающим составом. Остатки удаляются в центрифуге. Применяется для мелких деталей.
- Погружение с центрифугированием на оснастке. Детали фиксируются на оснастке, а затем вместе с ней погружаются в состав, центрифугируются и помещаются в печь. Применяется для особо ответственных деталей средних размеров.
- Погружение с вытягиванием. Детали погружаются в жидкую среду покрытия, после этого плавно вынимаются. Применяется для покрытия крупных деталей.
Отметим, что перед нанесением покрытия детали тщательно готовят. Поскольку при травлении серной или соляной кислотой в структуру стали проникает водород и детали становятся хрупкими, для очистки изделия перед нанесением цинк-ламельного покрытия используется другой способ. Поверхность обезжиривается водно-щелочным раствором, затем окалина и ржавчина удаляются дробемётной обработкой – стальными микрочастицами в виде шариков, которые ускоряются в турбине.
Кроме того, после нанесения каждого слоя цинк-ламельного покрытия происходит процесс сушки-спекания: изделия поступают в печь, разогретую до 200 °С, 240 °С или 320 °С. Таким образом покрытие структурируется и образуется однородный, тонкий, адгезионно-прочный и сухой слой.
Применение цинк-ламельного покрытия
- Транспортное машиностроение
Цинк-ламельное покрытие обычно наносится на стальные болты, гайки, шайбы, шпильки, винты, саморезы, анкеры, пружины, детали из листовой стали, элементы конструкций и др. В ветроэнергетических установках такое покрытие наносится на детали с резьбой.
Цинк-ламельное покрытие особенно подходит для высокопрочных болтов, винтов, шпилек (класс прочности 10.9 и выше), высокопрочных гаек (класс прочности 10 и выше), деталей конструкций с пределом прочности более 1000 Н/мм² или твёрдостью по Викерсу более 320 HV, чтобы избежать водородного охрупчивания.
Вывод
Среди всех видов покрытия цинк-ламельное заметно превосходит аналогичные, выигрывая по физическим и эстетическим параметрам. Несмотря на то, что детали покрываются тонким слоем состава и полностью сохраняют свою форму, они на 100% защищены от коррозии, а металл – от проникновения водорода и охрупчивания. Такое покрытие выдерживает максимальный класс нагрузки – С5. Его просто наносить на детали сложной формы, а требования к толщине материала базы минимальны. Несмотря на очевидные преимущества цинк-ламельного покрытия, в России его пока используют предприятия, которые можно сосчитать по пальцам одной руки.
Заказать изделия с цинк-ламельным покрытием, а также ознакомиться с российскими и международными стандартами применения данного материала вы можете на сайте ЦКИ.
Выступление специалиста в области цинк-ламельных покрытий Максима Крепака в рамках VII специализированной конференции «Крепёж. Качество и ответственность».
Цинковые покрытия — сравнение методов цинкования и их характеристики

Глубокий анализ-сравнение различных методов нанесения цинковых покрытий!
Как уже говорилось, горячее цинковое покрытие представляет из себя систему железо-цинковых сплавов с различным отношением содержания железа и цинка с постепенно уменьшающимся содержанием железа по мере приближения к внешней стороне покрытия.
Все железо-цинковые сплавы прочнее, чем сталь основы, что придает покрытию высокую устойчивость к истиранию. Наоборот, внешний ή-слой мягче, чем сталь, что создает хорошие условия для устойчивости к удару.
Таким образом, совокупность этих слоев создает устойчивость к разрушению при перевозках, монтаже и при обслуживании.
Цинковое покрытие, нанесенное электрохимическим способом, по механическим свойствам подобно обычному цинку, то есть является относительно мягким. Кроме того, электрохимическое цинкование осуществляется при обычной температуре, поэтому, кроме очень узкой переходной области, в системе не наблюдается железо-цинковых сплавов, и адгезия цинкового слоя к металлу основы относительно невелика. Сам процесс нанесения покрытия представляет определенные сложности с точки зрения равномерности нанесения покрытия, поскольку ток стремится избегать полостей. Приходится изощряться при пространственном расположении анодов. Метод является достаточно дорогостоящим, и поэтому ограничиваются нанесением покрытия на мелкие, в том числе резьбовые детали. Он не может конкурировать с методом горячего цинкования при защите цинком крупных, средних и даже большинства относительно мелких деталей.
Рис. 2. 11. Часть ассортимента деталей, которые могут быть механически оцинкованы.
Наоборот, метод шерардизации в модификации “Дистек” постепенно начинает отвоевывать пространство как у электрохимического, так и горячего цинкования. Достаточная толщина покрытия (до 60-120 мкм), его равномерность и плотность с последующей защитой методом фосфатирования позволяет изделиям выдерживать в солевом тумане (одним из основных методов определения коррозионной устойчивости изделий) до 1500 часов, что является очень хорошим показателем. Поскольку нанесение покрытия производится при 380-400°С на поверхности изделия, образующиеся железо- цинковые слои на данных изделиях получаются более твердыми, чем в случае электрохимического нанесения покрытий. Поступают сообщения о создании новых установок, позволяющих обрабатывать все более крупные изделия.
Сравнение свойств различных видов цинковых покрытий очень наглядно видно из таблицы № 2.12.
Поскольку, как видно из таблицы, все виды цинковых покрытий имеют как свои преимущества, так и недостатки, очевидно, что каждый тип покрытия имеет свою нишу применения. Встает вопрос, насколько долговечны покрытия различного типа, и имеется ли в этом вопросе преимущество одного типа покрытия перед другим. Ответ на этот вопрос дает рис. № 2.12, где приведены времена жизни покрытий, нанесенных различными способами и различной толщины. Из рисунка видно, что практически все точки для покрытий, полученных самыми разнообразными способами (горячее цинкование, электрохимическое, шерардизация, окрашивание в координатах “длительность службы” — “толщина покрытия” с очень малым разбросом укладываются на единую кривую, что говорит об отсутствии связи времени службы изделия с типом нанесения покрытия, основной фактор — это толщина покрытия. Однако надо иметь в виду, что красочное покрытие ограничено в сроке службы из-за подверженности его истиранию.
Рис. 2.12. Зависимость времени жизни покрытия от его толщины при разных способах нанесения.
Таблица № 12.2. Сравнение различных методов нанесения цинковых покрытий на функциональные свойства изделий (механическое цинкование в таблице не рассматривается, но по характеристикам оно ближе всего к методу шерардизации).
Характеристика покрытия |
Горячее цинкование |
Электрохимическое нанесение |
Шерардизация (механич. цинкование) |
Напыление цинка |
Окраска цинк-содержащими красками |
Адгезия |
Покрытие, сросшееся со сталью, из-за наличия различных железосодержащих слоев |
Хорошая, сравнимая с таковой для покрытий из других металлов |
Хорошая, сравнимая с таковой для электрохимического покрытия |
Хорошая механическая подготовка под окраску при условии, что дробеструйная подготовка проведена нормально |
При хорошей дробеструйной обработке дает наилучшие результаты |
Непрерывность и однородность |
Хорошие — любая непроцинковка хорошо видна в виде “черных пятен”. Некоторый избыток цинка на точках слива |
Однородная в пределах возможности ванны. Поры не представляют проблемы, поскольку сталь защищается прилегающим цинком |
Покрытие тонкое на углах — в противоположность горячему цинкованию |
Зависит от опытности оператора. Покрытие пористое, но поры вскоре заполняются продуктами коррозии цинка |
Хорошая — любые поры заполняются продуктами реакции |
Толщина |
Обычно 50-125 мкм на трубах и другой продукции; более толстые покрытия до 250 мкм получаются на сталях, раскисленных кремнием или после дробеструйной очистки перед цинкованием. Покрытия толщиной 10-30 мкм применяются на проволоке и листе. |
Толщина в пределах 3-15 мкм. Более толстые слои возможны, но невыгодны экономически |
Изменяются по желанию, обычно в пределах 10-80 мкм |
Толщина изменяется в интервале 100-150 мкм, но покрытия до 500 мкм могут использоваться |
До 40 мкм краски (или более в специальных случаях) при окраске в один слой |
Формуемость и механические свойства |
Обычные покрытия, на конечных изделиях не пригодны к изменению формы; слой сплава устойчив к абразивному воздействию, но хрупкий при гибке. Специальные покрытия с тонким слоем сплава или при его отсутствии хорошо формуются (на листах) и устойчивы к сварке |
Сталь с электрохимическим покрытием обладает превосходной формуемостью и может быть сварена точечной сваркой. Небольшие детали обычно подвергаются такой обработке перед окраской |
Хорошие. Не наблюдается охрупчивания высокопрочных сталей |
При применении конечной продукции формовка не нужна. Можно осуществлять сварку через тонкое покрытие, если это необходимо, но обычно экранируют края, которые необходимо сварить, и после сварки эти места покрывают слоем цинка |
Сопротивление к истиранию лучше, чем у обычных красок. Окрашенные листы могут быть подвергнуты формовке и сварке с небольшими нарушениями покрытия |
Последующая обработка |
Конверсионные покрытия — хроматы предотвращают белую ржавчину; фосфатирование на новых листах является хорошей основой для последующей окраски |
Конверсионные покрытия (например, хроматы) для предотвращения белой ржавчины. Часто используются как основа для последующего окрашивания |
Могут быть применены конверсионные покрытия |
Возможно нанесение защитных покрытий, которые становятся основой для окрашивания, давая более долгую жизнь изделиям |
Может быть использова на отдельно или в качестве грунтовки под обычные красочные покрытия |
Другие свойства |
Доступны ванны различных размеров. Части изделий до 25 метров могут быть оцинкованы в некоторых случаях. Требуется внимательное отношение к дизайну изделия.Имеются непрерывные процессы цинкования листов и проволоки |
Любые размеры ванн доступны. Процесс обычно используется для простых, в основном, малых изделий, пригодных для цинкованиях в барабанах или при непрерывном цинковании листов и проволоки. Никакого нагревания, за исключением случая уменьшения водородной хрупкости для высокопрочных сталей |
Идеально для малых изделий, включая шайбы и пружины (примерно до 15 см или 250 г). Трудности при нанесении, например, внутри полых изделий |
Нет ограничений на размер или форму, очень экономичен для изделий с высоким отношением массы к поверхности. Неэкономичен при окрашивании сетчатых изделий. Наличие дополнительных трудностей (например, внутри труб) могут ограничить применение. Наилучший метод для нанесения очень толстых покрытий. Малое нагревание стали |
Пригоден для всего, что может быть окрашено, хотя могут быть трудности при окрашивании трубчатых структур. Не требуется никакого нагревания |
Горячее цинкование — Википедия
Материал из Википедии — свободной энциклопедии
Текущая версия страницы пока не проверялась опытными участниками и может значительно отличаться от версии, проверенной 25 сентября 2019; проверки требует 1 правка. Текущая версия страницы пока не проверялась опытными участниками и может значительно отличаться от версии, проверенной 25 сентября 2019; проверки требует 1 правка. Кристаллическая поверхность горячеоцинкованного металлаГорячее цинкование — покрытие металла (обычно железа или стали) слоем цинка для защиты от коррозии путём окунания изделия в ванну с расплавленным цинком при температуре около 460 °C. Под атмосферным воздействием чистый цинк (Zn) вступает в реакцию с кислородом (O2) и формирует оксид цинка (ZnO), с последующей реакцией с диоксидом углерода (CO2) и формированием карбоната цинка (ZnCO3), обычно серого матового, достаточно твёрдого материала, останавливающего дальнейшую коррозию материала.
Горячее цинкование считается одним из самых надёжных, экономичных и потому распространённых методов защиты железа и стали от коррозии.
Для металлоконструкций горячее цинкование является бесспорно самым распространённым видом покрытия.
Толщина цинкового слоя колеблется от 30 до 100 мкм, обычно — от 45 до 65 мкм.
По данным American Galvanizer Association горячее цинкование обеспечивает защиту от коррозии:
- В промышленной среде 65 лет
- В тропической среде: 70 лет
- В пригородной среде: 85 лет
- В загородной среде: 120 лет.
- В 1742 году французский химик и физик Поль Жак Малуэн (1701—1778) описал метод цинкования железа погружением в ванну с расплавленным цинком в докладе французской Королевской академии.
- В 1836 году французский химик Станислас Сорель (1803—1871) получил патент на данный метод цинкования железа, после очистки его сначала 9 % раствором серной кислоты (H2SO4) и затем флюсом — хлоридом аммония (NH4Cl).
-
Ванна с расплавленным цинком для горячего цинкования
Горячеоцинкованная балка
Горячеоцинкованный гнутый уголок
-
Стальной прокат, готовый к горячей оцинковке
Горячее цинкование крепежных изделий[править | править код]
Процесс[править | править код]
Горячеоцинкованные болты, гайки и шайбыТехнология нанесения покрытия такова. После обезжиривания, промывки, травления и повторной промывки, детали в барабане окунают в ванну (обычно керамическую) с расплавленным цинком. Вращением барабана обеспечивают поток цинковой массы относительно деталей для заполнения всех пор и микротрещин. Затем барабан вынимают из ванны и раскручивают для удаления излишков цинка центрифугированием. Однако на внутренней резьбе (на гайках) все же остаются излишки цинка, поэтому внутреннюю резьбу после цинкования протачивают. Отсутствие покрытия на внутренней резьбе не влияет на коррозионную устойчивость соединения, если гайка применяется с горячеоцинкованным болтом или шпилькой. Благодаря высокой анодности цинка по отношению к железу при температурах до 70°, цинк сам покрывает непокрытые и повреждённые участки детали со скоростью около 2 мм в год. В данном случае цинк с наружной резьбы болта, благодаря разности потенциалов цинка и железа в естественной влажной и кислой среде переносится на участки внутренней резьбы гайки, оставшиеся при проточке резьбы без покрытия.
Достоинства[править | править код]
- Коррозионная устойчивость в 5-7 раз превышает электрооцинкованный крепёж и приближается к устойчивости нержавеющей стали.
- Покрытие само себя восстанавливает на повреждённых участках.
- Покрытие более устойчиво к сколам при ударах, чем аналогичные по коррозионной устойчивости полимерные лакокрасочные покрытия.
Главным функциональным достоинством горячеоцинкованного крепежа является экономия на эксплуатации сооружений, благодаря отсутствию необходимости их перекрашивать.
Метод считается самым надежным и простым среди остальных методик цинкования. Рассмотренная нами процедура дает возможность достаточно легко обеспечить наилучшую антикоррозийную защиту благодаря максимальному слою цинка.
Недостатки[править | править код]
- Требует специальной высадки под толщину покрытия. Нельзя, из-за значительной толщины покрытия, просто купить болты без покрытия и оцинковать их горячим методом.
- Не все типоразмеры доступны (только от М8).
- Внешний вид — серый матовый.
- Из-за неравномерной толщины покрытия невозможно достичь высокой точности изделия.
- Гайки поставляются покрытыми транспортировочной смазкой (видно на фото — гайка блестит), для защиты от коррозии повреждённых проточкой участков внутренней резьбы.
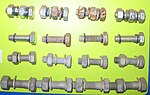
Горячее цинкование (Г/Ц) является вторым по распространённости после электролитического.
- Электролитическое цинкование (здесь- ЭЦ, или электроцинкование, также — гальваническое цинкование, англ. zinc electroplating, zinc plating, фр. zingage electrolytique, нем. elektrolytische Verzinkung)- самое распространённое для крепежных изделий покрытие. Главные достоинства — низкая цена и привлекательный внешний вид (обычно глянцевый серебристый, голубоватый либо жёлтый, бывает и матовый). Возможно ЭЦ деталей с пластиковыми элементами, например самоконтрящихся гаек. Главные недостатки — недостаточная коррозионная устойчивость делает это покрытие скорее транспортировочно-декоративным. Предназначено для деталей, используемых в сухих помещениях. Подвергает покрываемые детали водородному охрупчиванию, поэтому применимо для деталей класса прочности до 10.9.
- Дельта (Дакромет) — ближайшее к горячему цинкованию по цене, коррозионной устойчивости и внешнему виду покрытие, третье по распространённости покрытие для крепежных изделий. Главное достоинство — малая толщина (до 10 мкм) позволяет получить высокую точность детали, поэтому это покрытие получило широкое распространение в автомобильной промышленности. Позволяет покрывать детали любого класса прочности. Более привлекательный, чем у Г/О внешний вид — поверхность также матовая, но более ровная, без наплывов и бугорков; кроме того, возможны разные оттенки — от светло-серого (серебристого) до чёрного. Препятствует водородному охрупчиванию. Возможно покрытие деталей с пластиковыми элементами, например, самоконтрящихся гаек. Недостаток — покрытие легче, чем Г/О скалывается и неспособно самовосстанавливаться на повреждённых участках. Поэтому, например, на днищах автомобилей часто применяют Г/О крепёж.
- Термодиффузионное цинкование (ТДЦ, англ. sherardising, фр. cherardisation, нем. sherardisieren) примерно в два раза дороже, чем Г/Ц и Дельта (Дакромет), поэтому значительно менее распространено. Требует специальной высадки под толщину покрытия. Технология ТДЦ позволяет наносить цинковое покрытие любой толщины, в зависимости от требований. Но для получения удовлетворительной коррозионной устойчивости требуется толщина покрытия, не позволяющая нанесение на стандартно высаженные болты, из-за значительной толщины (от 40 мкм). Невозможно термодиффузионное цинкование деталей с пластиковыми элементами, например, самоконтрящихся гаек. Температура процесса 290—450 °C позволяет покрывать детали класса прочности до 10.9 — то есть, так же, как и Г/О.
- Газотермическое напыление — позволяет качественно наносить цинковое покрытие толщиной 200+ мкм на внешние поверхности крупногабаритных деталей непосредственно на месте монтажа, но неприменимо для крепежа, резьб, внутренних поверхностей диаметром менее 500 мм из-за технологических ограничений.
Термодиффузионное цинковое покрытие — Википедия
Покрытия термодиффузионные цинковые (ТДЦ)
Впервые этот метод был применен в Англии в начале XX века и получил название «шерардизация» (по фамилии изобретателя — Шерард (Sherard Cowper-Coles)).
Термодиффузионное цинковое покрытие является анодным по отношению к чёрным металлам и электрохимически защищает сталь. Оно обладает прочным сцеплением (адгезией) с основным металлом за счет взаимной диффузии железа и цинка в поверхностных интерметаллидных фазах Zn-Fe, поэтому покрытие мало подвержено отслаиванию или скалыванию при ударах, механических нагрузках и деформациях обработанных изделий.
Преимущество термодиффузионной технологии покрытий по сравнению с гальваническими состоит не только в её превосходстве по коррозионной стойкости, но и в том, что она не вызывает водородного охрупчивания металла.
Термодиффузионное цинковое покрытие в точности повторяет контуры изделий, оно однородно по толщине на всей поверхности, включая изделия сложной формы и резьбовые соединения.
Суть технологии термодиффузионного цинкового покрытия состоит в том, что антикоррозионное покрытие формируется в результате насыщения цинком поверхности металлических изделий в порошковой среде при температуре 290—450 °C, причём выбор температурного режима зависит от типа стальных изделий, марки стали и требований производителей деталей. Такая технология позволяет получить любую толщину покрытия в диапазоне от 6 до 100 микрон по требованию заказчика без изменения технологического процесса. Процесс происходит в закрытом контейнере с добавлением к обрабатываемым деталям специальной насыщающей смеси. Пассивация (финишная обработка деталей) предназначена для предотвращения образования жёлтых или белых продуктов коррозии на поверхностях, подвергаемых воздействию атмосфер с высокой влажностью, солёной воды, морских атмосфер или циклам конденсации и высыхания.
Защита металлов от коррозии обеспечивает долговременное функционирование различных деталей, конструкций и сооружений. Около 10% выпускаемых годового выпуска стали и стальных изделий ежегодно теряют свои технические характеристики из-за коррозии, что оценивается десятками миллиардов долларов. Один из наиболее распространенных способов защиты металлов от коррозии — покрытие цинком. Выбор цинка не случаен и объясняется высоким отрицательным значением окислительно-восстановительного потенциала пары Zn2+/Zn. Этот металл защищает основной металл (железо) анодно, то есть в гальванической паре «Fe-Zn» растворяется цинк. Электрохимической альтернативой цинку является кадмий, но его применение во многих странах запрещено из-за высокой токсичности. В РФ кадмирование имеет ограниченное использование и возможно, как правило, только по специальному разрешению. Толщина защитного цинкового покрытия выбирается в зависимости от назначения изделия и условий его эксплуатации. Анализ условий применения различных металлоизделий показывает, что защитное (антикоррозионное) покрытие для этих условий должно обладать не только повышенной коррозионной стойкостью, но быть также устойчивым к абразивному износу и иметь высокую степень сцепления с поверхностью защищаемого изделия.
Гальванические (электролитические) покрытия. Покрытия на поверхность изделий наносят в растворах электролитов под действием электрического тока. Основными компонентами этих электролитов являются соли цинка. Гальванический способ защиты металлоизделий имеет низкую коррозионную стойкость (около 140 часов в камере нейтрального соляного тумана), не позволяет нанести покрытие на изделия сложной конфигурации, при подготовке поверхности к оцинкованию на высокопрочных изделиях вызывает водородное охрупчивание, не позволяет производить демонтаж металлоизделий, имеет низкую степень сцепления с поверхностью. Данный вид защиты несет, скорее, декоративную функцию.
Металлизационные покрытия. Покрытия наносят путём распыления струей воздуха или горячего газа расплавленного цинка. В зависимости от способа напыления используют цинковую проволоку (пруток) или порошок цинка. В промышленности используют газопламенное напыление и электродуговую металлизацию.
Цинконаполненные покрытия. Эти покрытия представляют собой композиции, состоящие из связующего и цинкового порошка. В качестве связующих используют различные синтетические смолы (эпоксидные, фенольные, полиуретановые и тому подобные), лаки, краски, полимеры. Проявляют скорее свойства лакокрасочных, чем металлических покрытий.
Горячее цинкование. Как правило, горячее цинковние применяют для защиты от коррозии крупных металлоконструкций. Оцинкование мелких деталей и деталей с резьбой не дает необходимого качества оцинкованной поверхности. После обезжиривания, промывки, травления и повторной промывки, детали в барабане окунают в ванну (обычно керамическую) с расплавленным цинком. Вращением барабана обеспечивают поток цинковой массы относительно деталей для заполнения всех пор и микротрещин. Затем барабан вынимают из ванны и раскручивают для удаления излишков цинка центрифугированием. На деталях образуются наплывы, на внутренних резьбах остаются излишки цинка, резьбу приходится протачивать, снимая таким образом защитный цинковый слой, что в дальнейшем вызывает коррозию. Данный способ неприменим для мелких деталей, например для метрических крепёжных изделий. Не применим для деталей из высокопрочной и легированной стали.
Термодиффузионные цинковые покрытия. Они позволяют защищать от коррозии детали из любых марок стали, в том числе высокопрочных, и чугуна без изменения свойств основного металла, детали сложной конфигурации с отверстиями, детали в сборе, сварные и резьбовые. Ограничение размера деталей размером контейнера.
Комбинированные покрытия представляют собой комбинацию цинкового покрытия, лакокрасочного или полимерного. В мировой практике такие покрытия известны как «дуплекс-системы». В таких покрытиях сочетается электрохимический защитный эффект цинкового покрытия с гидроизолирующим защитным эффектом лакокрасочного или полимерного. Следует отметить, что гальванические и металлизационные цинковые покрытия не содержат интерметаллидных соединений (фаз) и состоят из цинка соответствующего химического состава. Горячецинковые покрытия, получаемые методом горячего цинкования (из расплава цинка), и диффузионные покрытия, наносимые из порошковых смесей на основе цинка, имеют аналогичный механизм образования — диффузионный. Однако диффузия цинка в металл различна: с применением горячецинкового покрытия диффузия составляет 0,1÷3%, термодиффузионного цинкования — 50÷70%. В соответствии с диаграммой состояния системы Fe—Zn в структуре этих покрытий присутствует ряд аналогичных фаз (интерметаллических соединений). Тем не менее общее строение этих покрытий всё-таки различно, также как их свойства.
Процесс нанесения термодиффузионного цинкового покрытия (ТДЦ)[править | править код]
Процесс нанесения покрытия представляет собой замкнутый технологический цикл, разбитый на несколько операций:
1-й этап: предварительная механическая очистка с помощью дробемётной установки; 2-й этап: загрузка очищенных деталей в контейнер; добавление насыщающей смеси; 3-й этап: проведение термодиффузионного процесса, обеспечивающего нанесение на покрываемую поверхность деталей цинкового слоя; 4-й этап: разгрузка деталей из контейнера с одновременной очисткой их от остатков насыщающей смеси и пассивирование. 5-й этап: остывание готовой продукции. Детали, предназначенные для нанесения следующих видов покрытий (краски, склейки, пластифицирование и др.), как правило, пассивируются 1 раз. Во всех других случаях проводятся две пассивационные операции, с промежуточной промывкой деталей. Для получения качественного антикоррозионного покрытия все технологические этапы имеют одинаково важное значение и являются равными составляющими технологического процесса. Следует отметить, что технология нанесения покрытия не делает исключения ни для одного вида деталей, которые по своим размерам, весу и конфигурации входят в технологический контейнер оборудования, принятого на вооружение в данный момент. Оборудование, предназначенное для обработки деталей другого размера, выполняется на заказ. Соответственно на этапе выработки технического задания определяется габаритный размер контейнера и печей, а также мощность остальных агрегатов в линии, пропускная способность дробемёта, пассивационных установок и сушки. Этап подготовки поверхности включает в себя ультразвуковую, дробемётную или пескоструйную очистку деталей, которая особенно важна для металлоизделий, имеющих на себе окалину после термической обработки во время производства.
Первое — это способность технологического процесса получить любую толщину покрытия по требованию заказчика. Второе — отсутствие склеивания деталей. Это один из самых негативных моментов, имеющих место в горячем цинке и в гальванике. Третье преимущество касается внешней и внутренней формы деталей. Российский рынок показал, что большинство крепежных и любых других вспомогательных деталей раньше красилось, пластифицировалось или просто оставалось без покрытия, так как они имели резьбовые соединения, полые и глухие отверстия, сложные соединения, сварные швы. Плюсом также является отсутствие каких-либо наплывов цинка в местах углублений или соединений. Четвёртое преимущество относится к возможности последующей обработки деталей разными видами красок, пластификаторов и т. п. Практически все виды промышленных красок хорошо прилегают к термодиффузионному покрытию. Высокая адгезия увеличивает коррозионную стойкость, практически исключается вздутие и отслоение красок с поверхности. Срок службы деталей с двойным покрытием увеличивается, что приводит к значительной экономии при их эксплуатации. Пятое преимущество состоит в экологической чистоте процесса (если нет необходимости в обезжиривании изделия).
В декабре 2003 года Департаментом электрификации и электроснабжения ОАО «Российские железные дороги» была выпущена инструкция по применению термодиффузионного цинкования деталей и конструкций контактной сети. Данная инструкция распространяется на защитные цинковые покрытия, наносимые методом термодиффузионного цинкования на резьбовые детали, арматуру, конструкции контактной сети и другие изделия из углеродистой и низкоуглеродистой стали, в том числе повышенной прочности, на чугунные и детали из цветных металлов контактной сети, включая чугунные оконцеватели фарфоровых изоляторов. C января 2008 года вышли ГОСТы на высокопрочный крепеж для металлических конструкций, в которых есть указание на применение термодиффузионного покрытия для защиты от коррозии высокопрочных болтов, гаек и шайб.
- ГОСТ 9.316-2006 «Единая система защиты от коррозии и старения. Покрытия термодиффузионные цинковые. Общие требования и методы контроля».
- ГОСТ 52643-2006 «Болты и гайки высокопрочные и шайбы для металлических конструкций. Общие технические условия».
- ЗАЩИТНЫЕ ЦИНКОВЫЕ ПОКРЫТИЯ: СОПОСТАВИТЕЛЬНЫЙ АНАЛИЗ СВОЙСТВ, РАЦИОНАЛЬНЫЕ ОБЛАСТИ ПРИМЕНЕНИЯ. Е. Проскуркин ГП «НИТИ», Украина журнал «Национальная металлургия» сентябрь, октябрь 2005 г. http://www.nmet.ru/a/2005/10/03/153.html
Стандарты цинковых покрытий — защита конструкций, ГОСТ, СНИП, рекомендации

В области стандартизации цинковых покрытий мы заметно отстаем от западных стран и США. Если в этих странах давно существуют стандарты как на процессы горячего нанесения покрытий, так и на особенности проектирования изделий для горячего цинкования, то в СССР (а затем и в России) имеется только один ГОСТ на горячее цинкование, лишь недавно в России появился стандарт на шерардизацию; только относительно электроцинкования и напыления металлических покрытий дела обстоят относительно нормально. Основную нагрузку по нормированию толщины покрытий несут СНиПы, но и в этом случае понятия о необходимой толщине покрытия очень размыты и могут трактоваться по-разному.
В ГОСТ 9.307-89 указывается, что толщина цинкового покрытия должна лежать в пределах от 40 до 200 мкм, в СНиП 2.03.11-85 — что для оцинкованных изделий для зданий и сооружений толщина покрытия должна лежать в пределах от 60 до 100 мкм. В “Общих технических требованиях к ограждающим устройствам на мостовых сооружениях, расположенных на магистральных автомобильных дорогах”, ОДН 218.012-99, указывается толщина покрытия не менее 80 мкм. В то же время связь между условиями цинкования и толщиной покрытия практически отсутствует, если не считать краткой информации в строительных правилах СП 23-101-98, где приведена связь между толщиной покрытия и временем цинкования (таблица № 3.1), причем для температуры, при которой промышленное цинкование не производится (480°С).
Таблица № 3.1. Рекомендуемые толщины покрытий (мкм) при различном содержании кремния в стали (из СП 23-101-98).
Время выдержки, мин |
Толщина цинкового покрытия, мкм, при содержании кремния, % масс. |
|||||||
0,05 |
0,075 |
0,1 |
0,12 |
0,2 |
0,3 |
0,4 |
0,5 |
|
3 |
80 |
140 |
90 |
85 |
90 |
125 |
160 |
200 |
6 |
110 |
240 |
140 |
100 |
120 |
160 |
210 |
280 |
9 |
140 |
360 |
200 |
120 |
200 |
260 |
330 |
400 |
Очевидно, что эти толщины весьма далеки от реальной практики цинкования, тем не менее, некоторые чиновники на основании этого документа создают требования толщины покрытия на отдельных объектах до 200 мкм.
До 80-х годов прошлого столетия разные страны имели свои собственные стандарты на горячее цинкование, причем эти стандарты часто не согласовывались между собой ни в части контроля, ни в классификации областей применения. Отметим, как наиболее разработанные, серию американских стандартов: ASTM A-385/1986/), ASTM A-384 (96), ASTM A-143/94, общеевропейские стандарты по горячему цинкованию EN ISO 1461 и EN ISO 14713. Но ни в этих, ни в большинстве стандартов других стран вообще не рассматривался тип сталей, применяемых в горячем цинковании.
Единственной страной, где в свое время была сделана попытка связать качество покрытия с типом стали, была Франция. Попытки на более низком уровне (уровне рекомендаций) связать тип стали с качеством покрытия были сделаны в Германии, а также в Швеции, где существовал стандарт SMS 2950 “Основные принципы и требования к технологии гальванизации горячим погружением”, в котором существовали два отдельных раздела с толщиной покрытия менее 100 мкм и с толщиной покрытия свыше 215 мкм с указанием об областях использования таких покрытий, но, по- видимому, и в них не было упоминаний о количестве кремния в используемых сталях. В северных странах, где особые требования к морозостойкости сталей, для удобства пользователей пошли по следующему пути: начали производить сталь с интервалом содержания концентрации кремния от 0,15 до 0,25%, особо мелкозернистую. Покрытие для такой стали остается умеренно толстым, матовым и неоднородным по цвету, но в этом случае мы уже не рискуем оказаться в пике Санделина, как при использовании полуспокойных сталей. Необходимо напомнить, что цвет покрытия играет роль только при сдаче объекта, через полгода-год цвет покрытия практически для всех сталей становится темно-серым из-за образования карбонатной пленки, и различия в цвете различных участков изделия становятся не очень заметными.
Из-за неопределенностей с толщиной покрытия во всех стандартах регламентируется минимальная толщина покрытия, но, в отличие от ГОСТ 9.307, как в американском, так и общеевропейском стандартах учитывается зависимость этой минимальной величины от толщины подложки. Эта зависимость определяется нижеследующей таблицей № 3.2.
Таблица № 3.2. Зависимость локальной и средней толщины покрытия на изделиях из стального проката (поз. 1-4), стального литья (поз. 5-6), а также подвергаемых центрифугированию деталей из прутка (поз. 7-9) и плоских изделий (поз. 10, 11).
№ п/п |
Толщина стали (мм) |
Локальная толщина покрытия (мкм) |
Средняя толщина покрытия (мкм) |
1 |
Сталь 6 мм и более |
70 |
85 |
2 |
Сталь от 3 до 6 мм |
55 |
70 |
3 |
Сталь от 1,5 до 3 мм |
45 |
55 |
4 |
Сталь менее 1,5 мм |
35 |
45 |
5 |
Литье более 6 мм |
70 |
80 |
6 |
Литье менее 6 мм |
60 |
70 |
7 |
Диаметр более 20 мм |
45 |
55 |
8 |
Диаметр от 6 до 20 мм |
35 |
45 |
9 |
Диаметр менее 6 мм |
20 |
45 |
10 |
толщина более 3 мм |
45 |
55 |
11 |
толщина менее 3 мм |
35 |
45 |
Эти данные перекликаются с данными американского стандарта ASTM A 123A/123M-97 “Standard Specification for Zinc (Hot-Dip Galvanized) Coatings on Iron and Steel Products”(табл.3.3), поскольку они основаны на реальной практике горячего цинкования.
Таблица № 3.3. Зависимость минимальной толщины покрытия от градации стали в изделии.
Категория материала |
Толщина материала в мм |
||||
<1,6 |
от 1,6 до 3,2 |
от 3,2 до 4,8 |
от 4,8 до 6,4 |
>6,4 |
|
Прокат |
45 |
65 |
85 |
85 |
100 |
Полоса |
45 |
65 |
75 |
85 |
100 |
Труба |
— |
— |
75 |
75 |
75 |
Проволока |
45 |
45 |
65 |
65 |
85 |
Примечание: под градацией понимается отнесение стали по толщине к некоторому интервалу толщины.
Существующие стандарты позволяют учитывать только часть практики горячего цинкования: как следует из рисунка № 3.1, обширная практика двух заводов, чьи данные приведены на рисунке, показывает, что толщины покрытия расположены, в основном, в области выше области нормального цинкования, причем толщины покрытия могут превышать нормальные аж в пять раз. Частично разброс в толщинах покрытия объясняется различной длительностью нахождения изделий или отдельных частей изделий в расплаве (это, кстати, учитывается в стандартах тем, что разрешенная локальная толщина в изделии может быть меньше средней толщины покрытия, рассчитываемой как средняя от суммы толщин различных частей изделия).
Но из рисунка вытекает и другая особенность горячего цинкования — часть покрытий имеет меньшую толщину, чем это допускается стандартами. Объяснить эту особенность горячего цинкования в настоящее время пока не представляется возможным, но с большой вероятностью это связано с особенностями кристаллизации сталей при непрерывной разливке. Борьба с этим отрицательным явлением — расцинковка изделия и его повторное цинкование. В этом случае из-за повышения шероховатости поверхности последующее цинкование идет с несколько большей скоростью, и толщина покрытия будет несколько больше.
Еще до массового применения оцинковки стальных изделий стало ясно, что для цинкового покрытия имеются всего два врага: это сернистый газ, побочный продукт тепловых электростанций, и дистиллированная вода. На рис. 3.2 показана хронологическая зависимость скорости уменьшения толщины цинкового покрытия и наличия сернистого газа в воздухе. Видно, что корреляция весьма и весьма хорошая.
Другая интересная зависимость приведена на рис. № 3.3. Здесь показана скорость коррозии цинкового покрытия, находящегося в воде, имеющей различные значения рН. Видно, что наименьшая скорость коррозии наблюдается в довольно широком интервале рН — от примерно 6 до 11. Но и в этом, оптимальном для покрытия интервале, скорость коррозии очень велика. Это объясняется очень просто — в воде происходит разрушение плотного карбонатно-гидроксидного покрытия, вместо него образуется проницаемое покрытие, и цинк уже не защищен. Таким образом, если цинковое покрытие периодически смачивается дождевой водой или на нем данная дождевая вода скапливается, то такое покрытие довольно быстро разрушается.
Рис. 3.1. Зависимость реально измеренной толщины покрытия от толщины металла для двух предприятий Германии (данные 1940 года).
Рис. 3.2. Скорость атмосферной коррозии цинка (г/м2*сутки) и поглощения диоксида серы из воздуха (г/м2*сутки) по месяцам в Берлине: 1 – поглощение диоксида серы; 2 – потери цинка.
Рис. 3.3. Скорость коррозии цинка в водных растворах в зависимости от значения рН.
Однако на практике оказалось значительно проще. При правильном проектировании изделий избыточной толщины не нужно. Исследования, проведенные за годы эксплуатации оцинкованных изделий, показали, что избыточная толщина цинкового покрытия в большинстве случаев не является оправданной, так как изделие морально устаревает прежде, чем оно начнет разрушаться под воздействием погодных факторов. Оказалось, что толщина покрытия в 60 мкм отражает все требования, предъявляемые к жизнестойкости оцинкованных изделий — в большинстве условий как континентального, так и приморского климата начальные скорости коррозии почти для всех категорий климата не превышают 4 мкм в год, а по мере течения времени скорость коррозии продолжает уменьшаться. Наглядно ожидаемое время жизни оцинкованных изделий наглядно видно из рис. 3.4 и таблицы № 3.4. Ожидаемое время жизни оцинкованного изделия с толщиной покрытия 100 мкм для сельской местности — порядка 100 и более лет, для приморского климата и промышленного города — порядка 50-40 лет, и только для морского климата и насыщенного промышленностью индустриального района — порядка 25-20 лет. Лишь для сооружений, находящихся в морской воде (особенно в зоне приливов) и в подземных сооружениях оцинкованные конструкции не рекомендуются к применению. В то же время в закладных изделиях, находящихся внутри бетона в контакте с солеными водами толщина покрытия в 50 мкм вполне достаточна.
Рис. 3.4. Предположения по времени службы оцинкованных изделий в зависимости от толщины покрытия для различных категорий агрессивности окружающей среды (по ISO 9223): С1- очень слабая; С2 – слабая; С3 – умеренная; С4 – суровая; С5 – очень суровая; Im2 – морская вода в районах умеренного климата.
Таблица № 3.4. Категории агрессивности климата (по ISO 9223, EN ISO 14713).
Климат |
||||
Категория агрессивности |
Среда местонахождения Справочные примеры |
скорость коррозии за первый год |
||
ISO 9223 |
EN ISO 14713 |
|||
Углеродистая сталь, мкм/год |
Цинк, мкм/год |
Цинк, мкм/год |
||
С1 (очень слабая) |
Внутренние помещения: сухие помещения |
<1,3 |
<0,1 |
<0,1 |
С2 (слабая) |
Внутренние помещения: временами конденсация влаги. Наружный климат: внутриконтинентальная cельская местность. |
1,3-25 |
0,1-0,7 |
0,1-0,7 |
С3 (умеренная) |
Внутренние помещения: высокая влажность, небольшое количество загрязнений. Наружный климат: внутриконтинентальный город, приморский климат со слабой засоленностью. |
25-50 |
0,7-2,1 |
0,7-2 |
С4 (суровая) |
Внутренние помещения: предприятия химической промышленности. Наружный климат: внутриконтинен- тальная промышленность, приморский город |
50-80 |
2,1-4,2 |
2-4 |
С5 (очень суровая) |
Наружный климат: Очень влажный промышленный климат, соленый приморский климат |
80-200 |
4,2-8,4 |
4-8 |
Погружные и подземные конструкции |
||||
Категория вредного воздействия |
Окружающая среда Справочные примеры |
|||
Im1 |
Пресная вода. Речныесооружения, гидроэлектростанции |
— |
— |
— |
Im2 |
Морская вода в районах умеренного климата. Сооружения портовой акватории. |
— |
— |
10-20 |
Im3 |
Грунт. Подземные хранилища, стальные сваи, стальные трубы |
— |
— |
— |
Защитное цинковое покрытие для крепежа
Дата публикации: 19.09.2019Один из самых важных вопросов при производстве крепежа – его долговечность и надежность. Наиболее действенным и распространенным способ для увеличения срока является нанесение цинкового покрытия. Цинк имеет отрицательный потенциал, поэтому в отличие от стали, изделия покрытые цинком более стойкие к агрессивным средам, за счет электролитов процесс коррозии замедляется, так как происходит регенерирование цинковой пленки при повреждении. Главное предназначение цинкового покрытия – защитить основную ферритную подложку от деформации.
Цинковое покрытие имеет широкую сферу применения при покрытии метизов, крепежа, а так же других производственных изделий. В ходе множества испытаний было выявлено, что срок эксплуатации крепежа с цинковым покрытием составляет около 30 лет, что значительно выше по-сравнению с изделиями без цинкового покрытия. Такие метизы и крепеж позволяют сократить расходы на постоянное сервисное обслуживание и замену расходных материалов на узлах. Покрытие из цинка может быть нанесено разными методами, в зависимости от заявленных характеристик.
Современные цинковые покрытия можно разделить на следующие виды:
- Гальваническое цинкование;
- Термодиффузионное цинкование;
- Горячее цинкование;
- Цинкламельное цинкование;
- Механическое цинкование.
При нанесении цинкового покрытия крепеж становится надежно защищенный от коррозии за счет своим анодным свойствам почти ко всем материалам, кроме алюминия и изделий с содержанием магния. Цинк оказывает сопротивление в агрессивных средах, таких как морская вода, кислоты и щелочи, поэтому крепеж с цинковым покрытием широко применяют в промышленности, при строительстве, а так же судостроительной сфере. Благодаря цинку сталь не подвергается коррозии, так как слой цинка его защищает.
Главным показателем надежности является большой срок службы. Существуют специальные методы проверки цинкового покрытия, один из таких – «климатические испытания», за счет убыстрения влияния окружающей среды и выявления появления коррозии на изделиях. Результатом такого испытания считается полученное значение коэффициента ускорения, которое имеет средние значения от 17-20%, от этого и вычисляется срок эксплуатации. Для крепежа, который предназначен для декорации, то коэффициент надежности покрытия считается 5-10%, для крепежа, который устанавливается в профессиональное оборудование или используется при строительстве, такой коэффициент составляет до 50%.
Метод гальванического цинкования
Давайте немного поговорим о методе – гальваническое цинкование. Этот метод считается наиболее распространенным. Химический процесс гальванического цинкования называется – электролиз. Суть метода в том, что в подготовленную ванночку с электролитом опускают стальную делать и платину из цинка, дальше в ванну проводят ток и при постоянном токе происходит процесс электролиза. Под действием тока, анодная пластина из цинка распадается на мелкие ионы, которые попадают на поверхность стальной детали, за счет этого происходит формирование гальванического покрытия. Толщина такого покрытия может варьироваться от 5 до 25 мкм.
Внешне изделия, покрытые методом гальванической оцинковке, имеют привлекательный вид с блеском, но одним из минусов считается небольшая стойкость к адгезии. За счет того, что происходит массовая оцинковка данным методом, поверхность крепежа может иметь масляную пленку, которая ухудшает цинковое покрытие, а так же негативно влияет на нанесения покрытия при увеличении расстояния между ними. В качестве электролита при гальваническом методе покрытия используются:
- Цианидные ванны. Такие ванны имеют в составе цианид натрия, что является очень токсичным веществом. При добавлении в состав ванн цианида, изделия получают свойства высокой эффективности покрытия, хорошая текучесть, за счет нее можно обработать даже самые сложные изделия, которые имеют множество граней, а так же при помощи такой ванны можно создать больше покрытий, чем в других. Самым значительным минусов считается, что цианид опасное вещество для окружающей среды и человека, а так же стальные изделия становятся хрупкими, что снижает прочность высокопрочной стали.
- Щелочные ванны. Такие ванны содержат не более 2 граммов оксида цинка, а так же не более 20 грамм натрия на 1 литр химического раствора. Значительным плюсом по-сравнению с цианидными ваннами, можно назвать большую безопасность для окружающей среды. Так же ванны из щелочи, имеют ограничения, в таких ваннах можно оцинковывать только стальной крепеж, процесс нагревания происходит до 30 градусов, так же стальные изделия становятся более хрупкими, за счет этого внешний вид утрачивает свой блеск и изящность.
- Кислотные ванны. Наиболее внимательно стоит рассмотреть кислотные ванны с низким содержанием кислот, что позволяет изделиям выглядеть привлекательнее, а поверхности быть полностью покрытой цинком. Так же значительным плюсом можно отнести стойкость стали к хрупкости при нанесении цинкового слоя для изделий, которые имеют многогранность. Поэтому данный метод применим к чугуну, а так же к сплаву из алюминия и меди. Наиболее часто данный метод позволяет изготовить изделия, который имеют разноцветный внешний вид и применяется для декора фасадов и конструкций.
Для того, чтобы все изделия имели привлекательный внешний вид, поверхность стали необходимо хорошо обработать. Перед оцинковкой, все листы стали проходят предварительную очистку от неровностей или следов коррозии. После происходит процесс оцинковки. Для закрепления результата, изделия осветляют за счет нанесения азотной кислоты, а так же хроматированием, чтобы изделия служили дольше. Дополнительное покрытие – называется пассивацией, которая может быть разных цветов: ярко-желтой, белой или с голубым отливом, а так же может быть черной. Но стоит быть острожным с такими покрытиями, так как на большинстве предприятий производящих метизы и крепеж, используют ядовитые вещества (шестивалентный хром) в виде пленки. Стоит обратить внимание, что такие покрытия теряют стойкость к коррозии при повышении температуры более 100 градусов. С 2007 года такие пленки из хрома является запрещенным в широкой линейке крепежа для автомобилей.
Покрытие | Цинк с добавлением хрома | ||||
---|---|---|---|---|---|
Блестящий | Блестящий | Блестящий | Блестящий | ||
Номинальный размер | Номинальный размер | Цвет | |||
метрический | дюймовый | обычный серебристый | голубой | желтый | чёрный |
< 5 мм | < 3/16 « | A1J | A1K | A1L | A1T |
5 < 10 мм | 3/16″ < 3/8″ | A2J | A2K | A2L | A2T |
> 10 мм | > 3/8″ | A3J | A3K | A3L | A3T |
С течением времени, такие опасные пленки были заменены на хромитные (трехвалентный), без содержания опасного хрома, которые решили множество проблем. С недавних пор, такой крепеж стали использовать в автомобильном производстве, так как он стал более защищенным от влияния окружающей среды, но не решил всех проблем. За счет того, что при обработке стали для нанесения цинкового покрытия при помощи разных ванн, применяются опасные химические вещества, которые негативно влияют на окружающую среду. Поэтому производствам, которые занимаются оцинковкой гальваническим методом необходимо непрерывно вести разработку и усовершенствование системы защиты окружающей среды от попадания вредных химических веществ, которые используются при электролизации. На данные сооружения предприятия отчисляют большие суммы, которые влияют на стоимость крепежа.
Не смотря на это, гальванический метод самый часто используемый метод для оцинковки крепежа, так как это наработанная схема, изделия которой пользуются высоким спросом. Гальванические ванны постоянно усовершенствуются, за счет появления новых технологий и разработок, что позволяет наносить цинковое покрытие на резьбу, а так же имеет привлекательный внешний вид. Негативными факторами можно назвать то, что при электролизации сталь становится более хрупкой, что делает невозможным использование этого метода для высокопрочной стали.
Метод горячей оцинковки
Метод горячей оцинковки производится в несколько этапов: 1. Сначала металл обезжиривают, промывают в специальных растворах, а так же травят в кислотном растворе и снова моют. 2. Подготавливают керамическую ванну с расплавленным цинком, температура которого достигает до 465 градусов, в которую окунают изделия в специально подготовленном барабане. 3. Барабан вращательными движения прокручивают, за счет этого горячий цинк равномерно распространяется по крепежу, что гарантирует наибольшее заполнение даже самых маленьких щелей. 4. После всего вышеописанного, барабан убирают из ванны и убирают лишний цинк.
Одной из отрицательных сторон данного метода – это то, что резьба не сохраняется и ее необходимо прокручивать заново. При этом, стойкость к коррозии таких изделий значительно снижается. Не смотря на это гайки, которые не имею покрытия, зачастую применяются совместно с болтами или шпилькой, которая горячеоцинкованная, благодаря такой системе, значительно снижается возможность разрыва изделия при установке, а так же покрытие будет более надежное, если гайка и болт будет не более чем на 2 мм дальше друг от друга. Такое возможно из-за того, что, к железу, цинк имеет более высокую анодность. Если же вы решите совместить крепеж, обработанный разными методами, то он долго не прослужит и покрытие быстро сотрется и изделие станет не защищенным от коррозии и потеряет свои свойства.
Метод горячей оцинковки оказывает большую защиту от коррозии, чем метод гальванической оцинковки. За счет этого, наиболее часто горячеоцинкованный крепеж используется при проведении электрики (установки оборудования на высоковольтных столбах), а так же разных вышек приемы/передачи, а так же для крепления дорожных знаков и ограждений. Стоит обратить внимание, что горячеоцинкованный крепеж имеет хорошие защитные свойства покрытия при повреждении, защитная оболочка регенерирует все повреждения не вызывая коррозию. Особую прочность имеет крепеж с классом прочности 8.8.
Наиболее непривлекательным моментом можно назвать высокую стоимость изделий, так как стоимость значительно выше стоимости при нанесении покрытия гальваническим методом, приблизительно на 30%. Стоимость выше за счет того, что по технологическому процессу емкости необходимо всегда поддерживать на высоких температурах, без возможности снизить температуру, когда цинкование не производится. Так же перед началом горячей оцинковки необходимо обработать резьбу, чтобы обеспечить припуск для цинка и исключить появления лишнего цинка. Допустимая норма цинка 40-60 мкм, из-за этого метод гальванического цинкования используют только для изделий с диаметром более 8 мм, так как резьба слишком маленькая. Метод горячей оцинковки не применяется в декоративных целях, так как цвет преобладает серых оттенков. Крепеж, который оцинковывается методом горячей оцинковки, не используется при строительстве автомобилей и рабочих машин.
Метод горячей оцинковки имеет свой особенности, которые подходят для определенного вида крепежа: гвозди, изделия из проволоки, потому что данный метод имеет погрешности при нанесении резьбы.
Метод термодиффузионного цинкования
Термодиффузионное цинкование широко применяется при обработке стали и имеет свои преимущества и недостатки, как и другие методы. Для данного метода цинкования, применяются специальные колбы, которые полностью изолированы от окружающего мира и не производят испарения, что позволяет производствам, значительно экономить средства. Технологический процесс применяет повышенные температуры вплоть до 4500 градусов, за счет которой изделия закаляются и не подвержены разрушению или ломкости, поэтому таким методом можно обрабатывать и изделия из высокопрочной стали. Имеют улучшенную стойкость к влиянию окружающей среды.
При применении метода термодиффузионного цинкования толщина цинкового покрытия достигает 50 мкм, что значительно выше, чем у гальванического метода. Стоит обратить внимание, что срок службы при соприкосновении с морской водой составляет около 15 лет. Так же стоит учесть, что покрытие может быть любой толщины, в зависимости от выдержки в специальной печи.
Положительно характеризует данный метод то, что при нанесении покрытия, цинк распределяется равномерно без подтеков, что позволяет покрывать данным методом сложный крепеж, который имеет много граней, а так же он отлично заполняет щели, полости в изделии. Для данного метода нет необходимости подготавливать изделия при помощи растворов, травления кислотой, чтобы не появилось высокое содержания водорода, что может привести к хрупкости, которую нельзя допустить для высокопрочного крепежа.
К отрицательным свойствам данного метода, можно отнести несколько особенностей, которые заключаются в том, что изделия покрытые данным методом нельзя использовать в декоративном плане, так как при термодиффузионном методе изделия приобретают темный непривлекательный цвет. Данный крепеж используется в конструкциях, которые несут существенные нагрузки, поэтому цвет зачастую неважен. Данный метод еще недавно не позволял изготовить сразу большие партии изделий, так как формы для оцинковки имели небольшие габариты, но сейчас уже изобретены большие формы, которые способны производить до 1 тонны крепежа единоразово.
При разработке данного метода была создана специальная система защиты от цинковой пыли. За счет специальных колб, которые не выпускают созданную цинковую пыль, данный метод считается наиболее защищенным и экологичным, по-сравнению с другими методами. Данная технология была описана и разработана в методе «Шерардайзинга».
Особенности данного метода заключается в том, что стальную поверхность сначала очищают от излишков металла и пыли, после чего частицы цинка начинают оцинковывать поверхность за счет соприкосновения с поверхностью железа и легирующими элементами, которая под воздействием высоких температур создает защитное покрытие. Полученное покрытие при помощи напыления закрепляется по всей поверхности изделия, включая резьбу, пробу.
При нанесении цинкового покрытия происходит диффузия цинка, которая влияет на заполнение повреждений в цинке при повреждении, такие повреждения могут влиять на увеличения напряжения, которое может сильно повлиять на деформацию крепежа из высокопрочной стали. Для создания такого процесса «заживления» необходимо, чтобы произошло взаимодействие между атомами цинка и стали. Для создания такой возможности, перед нанесением покрытия, необходимо произвести полную очистку металла, который будет цинковаться, а так же подготовить специальный раствор, изолируют короб, в котором будут производить восстановление. Такой процесс проходит при температурном режиме от 370 до 600 градусов, что значительно ускоряет диффузию и восстановительные свойства детали. Стоит обратить внимание, что такие созданные свойства влияют на покрытие и делают его ненадежным, что приводит к хрупкости металла и возникновению коррозии за непродолжительное время. Цинковые покрытия стоит наносить при средних температурах до 420 градусов. Так как за счет диффузии цинк занимает 1/3 толщины покрытия, что показывает на высокую стойкость к адгезии, а так же хорошую защиту от появления коррозии.
Толщина покрытия при термодиффузионном методе составляет от 25 до 110 мкм, это главное отличие данного метода, так как при термодиффузионном покрытии необходимо соблюдать четкие пропорции для толщины. Такие методом цинкуются маленькие шайбы и маленькие гайки, винты, которые имеют маленькую резьбу, которые защищены от влияния коррозии, а так же подходит для высокопрочного крепежа.
Стоимость таких изделий значительно ниже, чем при нанесении цинка при помощи других методов. На цену влияет отсутствие опасных для здоровья человека и окружающей среды отходов, что позволяет экономить средства на строительство и разработку технологий по защите окружающей среды.
Большим недостатком считается, что данные изделия получаются непривлекательными, не блестят и не могут служить декоративными элементами, но за счет дополнительного сплава, данный минус можно доработать и дополнить.
Термодиффузионный метод используется для нанесения покрытия в широкой сфере производства, промышленности, в машиностроении, где не применяются другие методы цинкования. Так же данный метод цинкования отлично применяется при строительстве больших сооружений, которые несут значительные нагрузки и для них важна надежная защита от коррозии, а так же стойкость к водородной хрупкости и т.п.
Метод механического цинкования
Механическое цинкование происходит при помощи водного раствора, в который опускают детали со стеклянными изделиями в виде шаров, а так же цинковый раствор. Данные растворы опускаются в специальный барабан или колоколообразный сосуд, который осуществляет вращательные движения. Стеклянные шары служат неким посредником, которые помогают цинковому раствору распространить цинк по всей поверхности изделия. Получившийся слой бывает двух типов:
- Тонкий слой до 10 мкм;
- Толстый слой до 20 мкм.
Раствор не подвергается повышенным температурам и весь процесс осуществляется при обычной температуре, что позволяет экономить бюджет.
Данный метод так же хорош, как и термодиффузионный метод, за счет того, что не происходит влияние на сталь, и она не становится хрупкой. Данный метод позволяет создать изделия, которые имеют отличные внешний вид и служат декоративными элементами при сборке мебели и фурнитуры. Срок эксплуатации таких изделий не более 2 лет, что очень незначительно. Поэтому данный метод оцинковки не применяется для изделий, которые будут установлены на производстве, машиностроении и т.п., так как они не будут обладать нужными свойствами.
Такие крепежные изделий покрытые методом механической оцинковки предназначены только для декоративной цели, поэтому изделия не имеют антикоррозионной защиты от появления ржавчины. Стоимость таких изделий самая привлекательная, так как нет затрат на сложные технические процессы, электроэнергию и нет необходимости беспокойства об окружающей среде и парах, которые попадают в воздух, воду. Данный метод применяется в небольших цехах.
Метод цинкламельного цинкования
Данный цинкламельный метод применяется при помощи добавления алюминия в цинковый раствор. Нанесение цинкового покрытия, может быть нанесено несколькими способами:
- При помощи опускания деталей в специальный, статический спрей без добавления неэкологичного шестивалентного хрома;
- При помощи специальных барабанов и колоколов.
Метод цинкламельного покрытия заключается в нанесении основного слоя, который покрывается параллельными полосами цинка с добавлением специального электропроводящего слоя, а поверх наносится несколько цинковых слоев, в зависимости от того, что необходимо от изделия. Верхними покрытиями можно добиться, что детали будут обладать привлекательным внешним видом, гибкостью, фрикционными свойствами, а так же стойкость к средам, где щелочи и кислоты.
Толщина подбирается по необходимым выходным параметрам, толщина которого может составлять до 100 мкм. Цинкламельное покрытие имеет разные сроки эксплуатации, если толщина до 10 мкм, то срок службы не более 700 часов. Если изделия закаляются при температуре более 2000 градусов, значит они способны служить более 2000 часов. В данном методе не возникает хрупкость при обработке, поэтому данный метод подходит для высокопрочного крепежа. Пластичность достигается путем добавления дополнительных элементов, что позволяет обеспечить сохранность резьбы. Так же при добавлении дополнительных элементов, можно получить разные цвета детали, что позволяет использовать их в декоративных целях.
Не смотря на все плюсы, цинкламельное покрытие хуже обеспечивает сохранность покрытия, чем гальваническое цинкование, об этом говорит ряд испытаний. Если Вы видите красивый метиз, то значит он декоративный, если же метиз черный или серый, то скорее всего метиз имеет более надежные свойства и стойкость к коррозии.
В отличии от других методов, детали оцинкованные цинкламельным методом, подходит для производства деталей для автомобильного производства. Цинкламельное покрытие надежно защищает крепеж от появления коррозии. Так же данное покрытие можно сравнить с гальваническим нанесение покрытия, но считается, что цинкламельное имеет более надежные свойства.
Если говорить в целом о покрытиях, то стоит обратить внимание на их свойства, которые появляются в ходе обработки элемента. При добавлении тех или иных металлов, свойства покрытия меняются и способны служить дольше или выдерживать высокие температуры эксплуатации, при этом защитный слой будет служить дольше, а так же при повреждениях сможет надежно защитить себя от появления коррозии. Поэтому, при выборе крепежа, необходимо четко понимать, где будет служить метиз, какие цели выполнять.
Методы нанесения покрытия имеют разные технологические процессы, а так же дополнительные вложения, для защиты окружающей среды от попадания вредных веществ. Главной целью большинства производителей, которые обрабатывают крепеж гальваническим методом, это обеспечить безопасность, с этим стремлением, появляются расходы на обеспечение этой безопасности, которая влияет на стоимость изделия. При нанесении покрытия методом горячей оцинковки происходят затраты на поддерживание постоянной температуры, что так же значительно влияет на стоимость изделия.
Материалы подготовлены специалистами компании «Трайв-Комплект».
При копировании текстов и других материалов сайта — указание
ссылки на сайт www.traiv-komplekt.ru обязательно!
Просмотров: 1237
19.09.2019