Гц 50 цемент: Цемент ГЦ-50 — Цементы огнеупорные
Глиноземистый цемент — что это?
Глиноземистый цемент представляет собой быстродействующую гидравлическую смесь, основной отличительной особенностью которой является способность быстро твердеть в воде и на воздухе. Такой тип цемента удается получить в процессе измельчения обожженного сырья, которое обогащено глиноземом. В качестве первичного сырья в процессе производства используют бокситы, известняк или породы с высоким содержанием оксида алюминия (поэтому вещество часто называют еще алюминатным цементом).
Цемент ГЦ может использоваться для приготовления особого жаростойкого бетона. Цемент отличается чрезвычайно высоким уровнем огнестойкости – согласно утверждениям специалистов, монолиты из такого раствора можно эксплуатировать при температуре до +1700 С. Часто смесь применяют в тандеме с шамотом или магнезитом, что дает возможность делать огнестойкие растворы, способные застывать в воде.
Несмотря на специфические свойства, цемент глиноземный используется как в индивидуальном строительстве, так и в промышленном.
Выбор конкретного метода производства зависит от специфики состава бокситов, объема содержания в элементах различных включений и т.д.
Содержание
- 1 Область применения
- 2 Особенности изготовления
- 2.1 Плавление
- 2.2 Спекание
- 3 Состав и свойства
- 4 Структура и виды
- 5 Технические характеристики
- 6 Маркировка
Область применения
Прежде, чем более подробно рассматривать глиноземистый цемент, его свойства и области применения, необходимо понять, где и почему он актуален. Данный тип смеси больше востребован, все же, в промышленной сфере, так как в быту огнестойкость на уровне тысяч градусов не нужна, а приобретать столь дорогое сырье из-за его способности ускоренного твердения не актуально.
Применение глиноземистого цемента в промышленной сфере:
- Ремонт и реконструкция мостов
- Ускоренное строительство конструкций с высоким уровнем устойчивости – все работы занимают до 3 дней
- Случаи, когда важно обеспечить монолиту стойкость к сульфатам
- Фиксация и крепление анкерных болтов
- Создание тары для эксплуатации с агрессивными веществами
- Обустройство нефтяных скважин
- Цемент глиноземистый ГЦ40 может использоваться как ускоритесь для схватывания бетона, компонент для огнеупорной смеси
- Осуществление ремонта морских судов
- Строительство железобетонных конструкций, подверженных особо серьезным нагрузкам
- Сооружение морских и подземных конструкций
- Введение в состав клеевых растворов, предназначенных для эксплуатации в области строительной химии
- ГЦ 40 цемент является основным компонентом при приготовлении расширяющихся и водостойких растворов
- Производство гидроизоляционной штукатурки также может осуществляться с использованием глиноземистого цемента – материал применяют в отделке водопроводных линий, метрополитенов, в стыках трубопроводов и т.
Применение глиноземистого цемента в индивидуальном строительстве:
- Обустройство стяжки пола (в некоторых случаях, где есть особые требования к бетону)
- Подготовительный этап работ с подоконниками
- Строительство подвалов, цоколей зданий (редко)
- Ремонт/реконструкция систем вентиляции, дымоходов в частных домах.
- Часто при сооружении каминов и топок в домах, иных видов отопительных устройств используют именно цемент ГЦ 40, характеристики которого позволяют обеспечить нужные свойства конструкции
Особенности изготовления
Глиноземистый цемент, свойства которого достаточно специфичны, изготавливается из чистых бокситов или известняков, с добавлением других элементов для придания нужных характеристик смеси. Основных способов производства цемента два – плавление и спекание. Выбор метода зависит от: состава бокситов, качества кокса, показателя объемного содержания в них оксидов железа, и в дополнение кремниевой кислоты.
Плавление
Для метода плавления используют бокситы высокого качества, к ним домешивают известняк и кокс. Эту смесь отправляют в ватержакетные печи с водяным типом охлаждения и плавят благодаря подаче через фурмы воздуха, до нужной температуры предварительно нагретого в рекуператорах. Потом массу пропускают через летку, в изложницах печи охлаждают и отправляют в дробилку для измельчения. В дробилках стоят многокамерные мельницы. Печи работают за счет пылевидного топлива.
В некоторых случаях используется электроплавка, в процессе которой выплавляется ферросилиций, за счет чего смесь очищается от кремниевой кислоты. Иногда применяют способ дуговой плавки с использованием специальных печей переменного тока с целью производства глиноземистого цемента особенно высокого качества. Сначала готовят сырье: измельчают, смешивают компоненты, делают из них гранулы или брикеты. Известняк заранее кальцинируют, а вот бокситы подвергают прокаливанию, шихту используют коксосодержащую.
В современных электродуговых печах уровень температуры может доходить до очень высоких показателей, именно из-за этого кремнезем в шихте восстанавливается до кремния, а он, в свою очередь, входит в реакцию с железом – так получается ферросилиций.
В производстве глиноземистого цемента могут использоваться и доменные печи, но материал получается не очень прочным на первых этапах твердения.
Спекание
Данный метод производства предполагает использование сравнительно невысоких температур в обычных печах. Сначала смесь медленно охлаждают, чтобы кристаллизовался геленит и приобрел стеклообразную форму. Тут важно, чтобы в процессе спекания температура не оказалась ниже оптимальной, так как это приводит к кристаллизации алюминатов кальция. В итоговом составе стекла появиться не должно, для чего создают системы очень быстрого охлаждения (чтобы не создались кристаллы геленита).
На этапе выхода из печи смесь превращают в гранулы паровоздушные потоки. Полученный данным методом глиноземистый цемент демонстрирует прекрасные показатели прочности в сравнении с веществом, которое охлаждалось более медленно.
Состав и свойства
Чтобы лучше понять, что такие глиноземистый цемент, стоит рассмотреть его состав. Основной компонент смеси – низкоосновной однокальциевый алюминат (обозначается как СаО-А12О3), который в процессе твердения трансформируется в двухкальциевый гидроалюминат. Цемент данного типа бывает малоизвестковым (с СаО меньше 40%) и высокоизвестковым (СаО больше 40%).
Состав глиноземистого цемента (указаны химические элементы):
- Оксид железа – от 5% до 15%
- Оксид кремния – от 5% до 15%
- Оксид кальция – от 35% до 45%
- Оксид алюминия – от 30% до 50%
Также в смесь вводят алюминаты, двухкальциевый силикат (призван замедлить твердение), геленит в качестве балластной примеси.
Особые свойства глиноземистого цемента:
1) Из-за наличия в составе смеси алюминатов кальция цемент обладает прекрасными вяжущими свойствами, высокой прочностью после полного твердения. Но сам процесс затвердевания глиноземистого цемента, хоть и схож с аналогичным поведением портландцемента, проходит с выделением тепла: в течение первых суток выходит около 70% тепла, а это опасно. Если температура воздуха будет выше +30 градусов, бетон будет демонстрировать стойкость, в 2-3 раза меньшую нормативной.
2) Глиноземный цемент создает более плотный искусственный камень (если сравнивать с портландцементом), демонстрирует высокую прочность, великолепную стойкость к агрессивным средам. Но такой монолит быстро деформируется в щелочной среде, поэтому его запрещено самостоятельно смешивать с гипсом, портландцементом, известью.
3) Скорость твердения бетонных растворов данного типа высокая: смесь начинает твердеть через полчаса, завершается процесс уже в течение 12 часов. Схватывается глиноземистый цемент так же, как и портландцемент, но нормативную прочность выдает уже через 72 часа, (а не по прошествии 28 суток).
Свойства глиноземистого цемента:
- Стойкость к газообразным средам, агрессивным жидкостям
- Возможность проводить работы при минусе
- Быстрый набор прочности
- Высокая плотность создаваемого монолита
- Высокий уровень термической устойчивости, что позволяет получать огнеупорные растворы
Структура и виды
В зависимости от того, какой объем примесей в веществе, цемент данного типа делится на два основных вида: обычный состав и высокоглиноземистый. Определение марки цемента осуществляется по прошествии 72 часов. Состав обычно завозится в Москву и область, другие регионы в небольших объемах, продается в специальных мешках или контейнерах по 40-50 килограммов. В зависимости от объема железа в общем составе и показателя окисления компонентов, глиноземистый цемент может быть зеленым, желтым, коричневым, черным по цвету.
Маркируется продукция ГОСТом.
Выделяют три основных вида глиноземистого цемента, которые отличаются по способности выдерживать нагрузки на сжатие: марок ГЦ-40, ГЦ-50 и ГЦ-60. По прошествии 72 часов после заливки смесь ГЦ-40 набирает прочность с 22.5 (МПа через сутки) до 40 МПа. Это самая ходовая марка, актуальная для разных строительных работ. Показатель прочности ГЦ-50 достигает 50 МПа, соответственно, цемент используется в сфера топлива и энергетики. Прочность ГЦ-60 доходит до 60 МПа, данную смесь эксплуатируют в оборонной сфере и металлургии. Цемент глиноземистый – это материал, который требует правильной эксплуатации.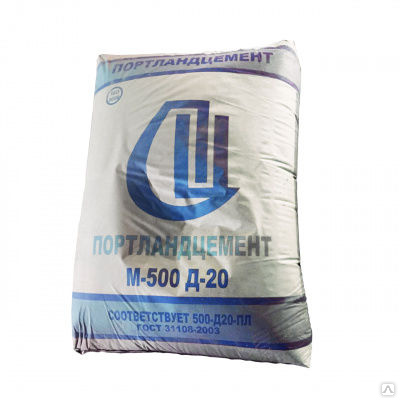
Смесь обычно готовится небольшими порциями, так как замедлить процесс твердения не удастся, а быстро использовать большие объемы бетона практически невозможно. Когда же состав начинает схватываться сразу по приготовлению, работать с ним очень трудно, да и на качестве итоговой конструкции это может сказаться.
Глиноземистый цемент нередко используется для приготовления разных типов расширяющихся смесей, быстротвердеющих составов. Для любого такого раствора соотношение компонентов и состав вычитываются отдельно. Обычно смесь при твердении увеличивается в объеме, балансируя усадку, а также самоуплотняется. Чтобы получить данные смеси, глиноземистый цемент смешивают с разными добавками.
Особые виды ГЦ:
- Расширяющийся цемент с гипсом и дробленым шлаком – схватывается быстро, расширяется в воде.
- Водонепроницаемая смесь с минимальной усадкой – в цемент добавляют полугидрат гипса и гашеную известь, что позволяет получать материал, актуальный для эксплуатации в гидроизоляционных работах.
- Расширяющийся водонепроницаемый цемент – быстро набирает прочность, используется для гидроизоляции судоходных шлюзов, туннелей, трубопроводов, бассейнов и т.д.
Технические характеристики
- Быстрое твердение – начинается через 30-45 минут, заканчивается по прошествии трех суток.
- Выделение больших объемов тепла в процессе твердения, благодаря чему глиноземистый цемент можно использовать при температуре до -10С.
- Повышенные характеристики стойкости как к низким, так и к высоким температурам.
- Огнеупорность – до +1300-1700 С.
- Высокий уровень плотности (мало пор в структуре).
- Очень высокая прочность.
- Стойкость к газообразным и жидким средам, коррозии, сернистым соединениям магния и кальция, хлоридам щелочных металлов.
Маркировка
Основное обозначение на упаковке смеси – это ее марка: МЦ-40 (что соответствует показателю прочности марки М400 – 40МПа), МЦ-50 и МЦ-60 (самый прочный – 60МПа). Кроме того, существуют высокоглиноземистые цементы первой-третьей категорий, которые обозначаются ВГЦ I, ВГЦ II и, соответственно, ВГЦ III. Маркировка может дополняться цифрами, обозначающими прочность – маркировка может быть такой: ВГЦ I-35, ВГЦ II-25, ВГЦ II-35, ВГЦ III-25. Также на упаковке часто указывают процент содержания алюминия в смеси – чем он выше, тем раствор будет прочнее.
Глиноземистый цемент – качественный и дорогой материал с особыми характеристиками, который нужно уметь выбирать и правильно использовать. Приобретать смесь лучше у проверенных поставщиков, а перед приготовлением и эксплуатацией тщательно изучить всю информацию и правила работы с раствором. В таком случае удастся создать прочную и долговечную конструкцию с нужными характеристиками и корректно выполнить любую поставленную задачу.
Глиноземистый цемент в Ижевске ООО МЕРКУРИЙ
Цену уточняйте у менеджера по тел. 8-912-757-12-35
Даже неспециалист знает, что цемент — основа строительного процесса. Однако немногим известно, что современный цемент имеет множество разновидностей – это обстоятельство позволяет удовлетворить различные практические запросы строительства.
Глиноземистый цемент представляет собой высокопрочный вяжущий материал коричневого, тёмно-зелёного, серого либо чёрного цвета, быстро затвердевающий как в воде, так и на воздухе. ГЦ цемент изготавливается путём измельчения обожженной насыщенной глинозёмом сырьевой смеси. Это единственная разновидность цемента, которая увеличивается в объёме во время затвердевания и сразу выделяет тепло.
Глиноземистый цемент является одним из наиболее жароустойчивых цементов, он может выдержать температуру до 1700C°. Способность затвердевать в условиях повышенной влажности – ещё одно достоинство ГЦ цемента. Для этого материала свойственны высокая скорость тепловыделения, морозоустойчивость, водонепроницаемость, невосприимчивость к агрессивных воздействиям жидких и газообразных веществ. Уникальные свойства глиноземистого цемента обусловили его применение в специальных областях строительства и производства.
Применение глиноземистого цемента
• Получение быстрозатвердевающих жаростойких бетонов и смесей, применяемых при скоростных и аварийных строительных работах, бетонировании в зимних условиях.
• Изготовление железобетонных конструкций особого назначения на предприятиях и стройплощадках (изделия можно выпускать с завода уже через 24 часа после их изготовления).
• Возведение железобетонных сооружений, испытывающих воздействие минерализованных (например, морских) вод.
• Изготовление гидроизоляционных штукатурок.
Кроме глиноземистого цемента компания «Меркурий» рада предложить вам большой ассортимент строительных и огнеупорных материалов.
Технические характеристики глиноземистого цемента марки ГЦ-40:
Химический состав, содержание оксидов, % | |||||
Al2O3 | CaO | Fe2O3 | SiO2 | MgO | TiO2 не более 9 |
Физико-механические показатели | Значение для марки цемента | ||
Предел прочности при сжатии, | 40 | 50 | 60 |
МПа, не менее в возрасте: 1 суток | 22,5 | 40 | 27,4 |
Тонкость помола: ГОСТ 6613, % не более | 10 | 10 | 10 |
Сроки схватывания глиноземистого цемента: начало — не ранее чем через 30 мин. , а конец — не позднее чем через 12 час. после начала затворения.
Сроки схватывания могут быть изменены введением замедлителей (борной кислоты, буры, хлористого кальция и др.) или ускорителей (известь, портландцемент, гипс и др.).
Прочность глиноземистого цементного камня нарастает с большой скоростью. Уже через сутки сопротивление сжатию и растяжению достигает более 50 % проектной прочности.
Для твердения глиноземистого цемента наиболее благоприятной является температура + 15-20 °С при нормальной влажности или твердения в воде.
При твердении, протекающем при температуре выше 30 °С, прочность цемента снижается в 3-4 раза.
Отрицательное влияние высокой температуры в раннем возрасте твердения сказывается резче, чем в более позднем.
При пониженных положительных температурах твердение происходит менее интенсивно, но все же значительно быстрей, чем портландцемента.
При охлаждении массы цемента (бетона) ниже -2°С твердение его с водой практически прекращается.
Поэтому для твердения необходимо обеспечить оптимальные температурные условия.
Возможна также поставка цемента глиноземистого марки ГЦ-50,60 и высокоглиноземистых цементов марки ВГЦ.
Глиноземистый цемент — Огнеупорные материалы
Цемент является одним из важнейших и необходимых в строительстве материалов. Его применяют для производства бетонов, бетонных и железобетонных изделий, строительных растворов, асбестоцементных изделий. Цемент — это общее название группы гидравлических вяжущих веществ, главной составной частью которых являются силикаты и алюминаты кальция, образовавшиеся при высокотемпературной обработке сырьевых материалов, доведенных до частичного или полного плавления.
Одним из видов цемента является глиноземистый цемент. Глиноземистый цемент представляет собой быстро твердеющее в воде и на воздухе высокопрочное вяжущее вещество, предназначенное для изготовления строительных и жаростойких растворов и бетонов.
Глиноземистый цемент получают путем тонкого измельчения обожженной до спекания или сплавления богатой глиноземом сырьевой смеси. В настоящее время обжиг проводится чаще всего до плавления в доменных или электродуговых печах. При этом не требуется тонкого измельчения сырьевых компонентов и создаются условия для удаления железа и кремнезема.
Сырьем для глиноземистого цемента служат бокситы и чистые известняки. Бокситы — горная порода, состоящая из гидратов глинозема (А12О3 • nН2О) и примесей (в основном Fe2O3, SiO2, СаО и др.). Бокситы широко используются в различных отраслях промышленности: для получения алюминия, абразивов, огнеупоров, адсорбентов и т.п., а месторождений с высоким содержанием А12О3 очень немного.
Химический состав глиноземистого цемента, получаемого разными методами, находится в следующих пределах: СаО – 35 — 45 %; А12О3 – 30 — 50 %; Fe2O3 – 0 — 15 %; SiO2 – 5 — 15 %. В минеральном составе клинкера глиноземистых цементов преобладает однокальциевый алюминат СаО • А12О3 (СА), определяющий основные свойства вяжущего вещества. Кроме того, в нем присутствуют алюминаты — СА2, С12А7; двухкальциевый силикат C2S, отличающийся, как известно, медленным твердением, и в качестве неизбежной балластной примеси — геленит — 2СаО • А12О3 • 2SiO2.
При затворении водой глиноземистого цемента однокальциевый алюминат гидратируется. Образующееся при этом соединение служит главной составной частью затвердевшего материала. Начало схватывания глиноземистого цемента не ранее 45 минут, конец схватывания не позднее 10 часов. Сроки схватывания могут быть изменены введением замедлителей (борной кислоты, буры, хлористого кальция) или ускорителей (известь, портландцемент, гипс и др.).
Внешние параметры глиноземистого цемента — это тонкий порошок серо-зеленого, коричневого или черного цвета. Глиноземистый цемент фасуют в мешки по 50 кг и в контейнеры.
Наиболее ценным свойством глиноземистого цемента является способность быстрого затвердения при затворении водой.
Его объемный вес в рыхлом состоянии 1000-1400 кг/м3; при этом от портландцемента он отличается тонкостью помола, у глиноземистого цемента этот показатель значительно выше — остаток на сите № 008 составляет не более 10%.
Глиноземистый цемент характеризуется пониженной способностью к деформации в связи с крупнокристаллической структурой формирующегося цементного камня. Кроме того, из-за наличия кубического гидратированного моноалюмината при формировании цементного камня происходит потеря массы.
Для глиноземистого цемента характерно выделение большого количества тепла до до 376 кДж/кг (90 к кал/кг) тепла, при этом энергичное выделение тепла полностью происходит в первые часы схватывания и твердения цементного теста. Это свойство глиноземистого цемента, с одной стороны, ограничивает использование его для бетонирования массивных конструкций, с другой — может оказать положительное влияние на производство бетонных работ при отрицательных температурах до -10 градусов без подогрева.
Глиноземистый цемент является одним из самых огнестойких цементов (его огнестойкость выше, чем у портландцемента). Он не теряет своих основных характеристик даже при эксплуатации в температурном режиме до 1700C°. В смеси с огнеупорными наполнителями, такими как магнезит, хромитовая руда, шамот глиноземистый цемент используют для получения гидравлически твердеющих огнеупорных растворов и бетонов. Кроме того, данный цемент имеет повышенную плотность цементного камня, что определяет большую устойчивость бетона против кислых и промышленных вод, морской воды, органических кислот, растительных масел.
По сравнению с портландцементом глинозёмистый цемент обеспечивает получение бетонов и растворов большей плотности и водонепроницаемости. Однако глиноземистый цемент быстро разрушается даже слабыми растворами солей аммония и щелочей. Его нельзя применять в щелочных средах и смешивать с известью или портландцементом.
Существуют два способа производства глиноземистого цемента: метод плавления сырьевой шихты и обжиг до спекания.
Способ производства глиноземистого цемента методом плавления включает в себя подготовку зернистой шихты из цементного сырья, плавление, охлаждение полученного шлака, дробление и тонкое измельчение.
Способ спекания характеризуется тем, что исходные компоненты цементного сырья просушивают, тонко измельчают и перемешивают до достижения полной гомогенизации, после чего порошкообразную или гранулированную цементную шихту направляют в печь и выполняют обжиг цементного клинкера в различных печах. Далее цементный клинкер охлаждают, подвергают помолу и получают глиноземистый цемент.
При твердении глиноземистого цемента основное соединение — однокальциевый алюминат, подвергается гидратации, в результате чего образуется двухкальциевый гидроалюминат. При взаимодействии глиноземистого цемента с водой не образуется гидрата окиси кальция, благодаря чему цементный камень, бетоны и растворы на глиноземистом цементе значительно лучше противостоят действию минерализованных вод; отсутствие трехкальциевого гидроалюмината повышает стойкость к сульфатной коррозии. Однако бетоны па глиноземистом цементе корродируют в кислых агрессивных средах, концентрированных растворах сернокислого магния и в щелочных средах при концентрации щелочей более 1%. С повышением температуры твердения глиноземистого цемента сверх 25—30° С прочность цементного камня понижается, вследствие перекристаллизации двухкальциевого гидроалюмината в трех-кальциевый. Поэтому пропаривание и автоклавную обработку изделий на глиноземистом цементе не производят.
При пониженных положительных температурах твердение происходит менее интенсивно, но все же значительно быстрей, чем портландцемента.
При охлаждении массы цемента (бетона) ниже -2 °С твердение его с водой практически прекращается, поэтому для твердения необходимо обеспечить оптимальные температурные условия.
Различают 2 вида глиноземистого цемента:
- обычный глиноземистый цемент (содержит 73—75% глинозема, до 1% кремнекислоты и менее 0,5% оксида железа, состоит в основном из диалюмината кальция — СА2 и небольшого количества геленита и моноалюмината, температура плавления сырья 1450-1480С)
- высокоглинозёмистый цемент (при наличии 60—65% глинозема содержит 2—3 % кремнекислоты, температура плавления сырья — 1700-1750С)
Глиноземистый цемент выпускается по ГОСТ 969-91 трех марок: ГЦ-40, ГЦ-50, ГЦ-60. Марку цемента определяют в возрасте трех суток после изготовления образцов.
№ |
|
|||
п/п |
Физико-механические показатели |
Значение для марки цемента |
||
1 |
Предел прочности при сжатии, МПа, не менее в возрасте: |
40 |
50 |
60 |
|
1 сут. |
22,5 |
27,4 |
32,4 |
|
3 сут. |
40 |
50 |
60 |
2 |
Тонкость помола: |
|||
|
Остаток на сите с сеткой № 008 по ГОСТ 6613, % не более |
10 |
10 |
10 |
3 |
Сроки схватывания: |
|||
|
начало, мин. |
45 |
45 |
45 |
|
конец, час., не позднее |
10 |
10 |
10 |
Учитывая дефицитность сырья (бокситов) и значительную стоимость глиноземистого цемента, его выпускают в сравнительно небольших количествах (менее 1 % от общего выпуска цемента).
Применяют данный вид цемента для изготовления бетонных и железобетонных сооружений, когда расчетная прочность бетона должна быть достигнута в течение 1-х, 2-х, или 7 суток; для строительства морских и подземных сооружений, где требуется повышенная сульфатостойкость; для тампонирования холодных нефтяных скважин, тампонирования трещин в породах при большом дебите воды; для заделки пробоин в судах морского транспорта; для быстрого устройства фундаментов под машины, заливки анкерных болтов, восстановления поврежденных зданий и мостов; для изготовления сборных железобетонных изделий на заводах ЖБИ и строительных площадках, где глиноземистый цемент играет роль ускорителя твердения бетона; для изготовления емкостей и других сооружений, где глиноземистый цемент придает повышенную стойкость против органических кислот, соединений серы, серной кислоты, молочной кислоты, соляного раствора, крахмала и для изготовления огнеупорных бетонов и штучных изделий с огнеупорностью до 1700 °C.
Кроме того, на основе глиноземистого цемента в смеси с жаростойкими заполнителями изготовляют бетоны, которые хорошо сопротивляются действию высоких температур (1000°С и выше). Глиноземистый цемент используют также для получения расширяющихся цементов: водонепроницаемый расширяющийся цемент (ВРЦ), водонепроницаемый безусадочный цемент (ВБЦ), гипсоглиноземистый расширяющийся цемент(ГГРЦ).
Ведущим дистрибьютором глиноземистого цемента, а так же других огнеупорных материалов является ООО «ОгнеупорЭнергоХолдинг» — тел. (495) 617-01-74.
В компании представлен широкий ассортимент огнеупорных материалов различных видов и марок по приемлемым ценам, с которыми Вы можете ознакомиться на сайте OGNEYPOR.RU
Испытания цементобетона на высокочастотную вибрацию для станков (300–500 Гц)
Основные характеристики станков в значительной степени определяются конструкцией и расположением конструктивных элементов. Кроме того, материал, используемый для структурных компонентов, оказывает большое влияние на конструкцию и размеры машин. Основными материалами для станков являются сталь и чугун. Однако все чаще предпринимаются попытки заменить их альтернативными материалами для снижения затрат и/или улучшения статических, динамических или тепловых характеристик машин. Обзор исследований в области материалов, используемых для станков, можно найти в [1].
Одним из альтернативных материалов для деталей станков является цементобетон. При сравнительно низких материальных затратах и высоком демпфировании материала, а также из-за нехватки сырья в начале ХХ века уже предпринимались попытки использовать цементобетон вместо стали или чугуна для токарных станков [1]. Тем не менее, из-за многочисленных проблем в производстве и применении, а также из-за разработки полимербетона исследования цементобетона в станках были на время приостановлены. Однако с момента разработки сверхвысококачественного бетона (UHPC) количество исследований по этой теме снова увеличилось.
В настоящее время цементобетон иногда используется для станин машин или конструктивных частей станков с малыми нагрузками, таких как координатно-измерительные машины или прецизионные машины [1]. Однако до сих пор отсутствуют фундаментальные исследования динамических характеристик цементобетона для использования в станкостроении. Особенно необходимо исследовать поведение при знакопеременных динамических нагрузках в высокочастотном диапазоне (> 200 Гц). Это связано с тем, что в области строительства испытания цементного бетона на усталость в основном проводятся с использованием испытаний на набухание под давлением в низкочастотном диапазоне (например, около 10 Гц) [2,3,4,5,6]. Эти низкие частоты испытаний, используемые в настоящее время в строительстве, означают, что испытания обычно ограничиваются 2 миллионами циклов нагрузки, а продолжительность испытаний очень велика. Испытания с циклами нагрузки до 10 8 в переменном диапазоне и частотах > 200 Гц, как они встречаются в станках, пока мало изучены. Результаты работы [3] показывают, что динамическая усталостная прочность простого бетона без армирования при нагрузках на сжатие составляет около 50–60 % от статической прочности на сжатие.
Развитие поведения бетона при испытаниях на усталость характеризуется тремя различными фазами: фазой образования трещин (фаза I), фазой стабильного распространения трещин (фаза II) и фазой нестабильного распространения трещин (фаза III) [2]. ]. Редкие исследования поведения динамической усталости при растягивающих нагрузках показывают, что ход усталостного поведения цементного бетона аналогичен таковому при сжимающих нагрузках и также может быть описан тремя характерными фазами [7,8,9].,10] (см. также рис. 1). Согласно [11, 12], динамическая усталостная прочность при растягивающей нагрузке также лежит в диапазоне 40–50 % от статической прочности цементобетона на растяжение, и различные дообработки не оказывают существенного отрицательного влияния на усталостную прочность.
Фазы усталостного поведения цементобетона по [2]
Описание стенда
Для исследования поведения цементобетона при знакопеременных динамических нагрузках в высокочастотном диапазоне , в Лаборатории станкостроения и технологии производства (WZL) Университета Рейн-Вестфалия Ахена был разработан испытательный стенд, основанный на принципе резонанса. На данном испытательном стенде образцы цементобетона могут подвергаться знакопеременным нагрузкам в диапазоне частот до 550 Гц и с амплитудами усилия до 25 кН. Устройство испытательного стенда и первые испытания с различными типами цементобетона описаны в [12,13,14], но краткое изложение также дается в этой статье.
В основном испытательный стенд состоит из рамы, гидравлического возбудителя, резонансной массы и инертной массы (см. рис. 2). Гидравлический возбудитель размещен относительно между рамой и резонансной массой и вызывает колебания резонансной массы. Образцы цементобетона устанавливаются между резонансной массой (на верхнем конце) и инертной массой (на нижнем конце). Чтобы резонансная масса могла колебаться, она упруго закреплена на четырех пружинах, которые размещены на инертной массе. Когда резонансная масса вибрирует, эта вибрация индуцируется в образце и приводит к сжатию, соответственно, удлинению образца за счет его закрепления на инертной массе. Вся система из инертной массы, образца и резонансной массы развязана от окружающей среды дополнительными пружинами и может быть приближенно описана как осциллятор с одной степенью свободы. Возбуждая резонансную массу собственной частотой системы, можно добиться усиления силы, приложенной к образцу. Таким образом, можно использовать возбудители (например, упомянутый гидравлический возбудитель), которые обычно используются для исследования станков. [13]
Стенд для испытания знакопеременных нагрузок на образцы СВПК в диапазоне высоких частот по [13]
Изображение в натуральную величину часть рамы и может перемещаться вверх и вниз с помощью шарикового винта. Пружины между резонансной массой и инертной массой установлены с предварительным натягом, что приводит к предварительному натяжению образца. Следовательно, поперечина компенсирует эту предварительную нагрузку, когда она перемещается вниз, соответственно превращая предварительное натяжение образца в предварительное сжатие, когда он перемещается дальше вниз. [13]
Поскольку, как описано выше, колебательная система испытательного стенда может быть описана как осциллятор с одной степенью свободы, очевидно, что собственная частота зависит от общей жесткости и вибрирующей массы. Таким образом, при заданной жесткости системы испытательного стенда и образца можно влиять на собственную частоту, адаптируя вибрирующую массу. Как видно из уравнения на рис. 2, увеличение вибрирующей массы приводит к снижению собственной частоты и наоборот. Поэтому существуют различные дополнительные массы, которые можно установить на резонансную массу для увеличения вибрирующей массы. Таким образом можно регулировать частотный диапазон вибрационных испытаний. Тем не менее определенная собственная частота испытаний зависит от материала и формы испытуемого образца. Это связано с тем, что из-за своего положения в прямом силовом потоке жесткость образца напрямую влияет на общую жесткость и, следовательно, на собственную частоту системы.
Во время вибрационных испытаний различные датчики, встроенные в испытательный стенд, собирают разные типы данных. Датчик силы на гидравлическом возбудителе измеряет возбуждающую силу, а другой датчик силы измеряет усиленную силу, действующую на образец цементобетона. Этот второй датчик силы встроен между резонансной массой и образцом и предварительно нагружен сжатием в 80 кН. Анализируя соотношение между двумя силовыми сигналами, можно определить коэффициент усиления в зависимости от частоты возбуждения. Коэффициент достигает своего максимума на собственной частоте системы.
Кроме того, на переходные пластины образца устанавливаются два датчика одноосного ускорения (один вверху и один внизу образца). Путем двухкратного интегрирования сигналов ускорения можно определить относительное удлинение или относительное сжатие образца. На рис. 2 показан испытательный стенд и его компоненты, а также различные возможные дополнительные массы.
Как было сказано выше, собственная частота колебательной системы зависит, с одной стороны, от величины резонансной массы, а с другой стороны, от формы и жесткости образца. Поэтому собственная частота должна определяться в начале каждого нового испытания. Это достигается путем измерения частотной характеристики (АЧХ) системы путем ее возбуждения синусоидальным сигналом развертки, индуцированным гидравлическим возбудителем. После этого на возбудитель настраивается синусоидальный сигнал с определенной собственной частотой системы и настраивается амплитуда возбудителя таким образом, чтобы в образец индуцировалась необходимая сила. Продолжительность каждого теста установлена на 10 8 циклов нагрузки, потому что обычная продолжительность 10 6 циклов нагрузки (рассматриваемая, например, для усталостного поведения металлов) достигается менее чем за час при использовании интересующего диапазона высоких частот. При продолжительности 10 8 циклов нагрузки испытания длятся от двух до трех дней.
Можно предположить, что жесткость и масса испытательного стенда остаются постоянными для каждого испытания. Следовательно, изменения собственной частоты во время испытания вызваны изменением жесткости образца из-за микротрещин в материале. Однако изменение собственной частоты также приводит к уменьшению коэффициента усиления и, следовательно, к уменьшению силы, действующей на образец. Из-за этого необходимо контролировать и адаптировать собственную частоту системы, а также амплитуду силы, действующей на образец во время испытаний. Ручная регулировка нагрузки приводит к непостоянной и в большинстве случаев более низкой нагрузке, чем требуется (особенно ночью и в выходные дни). Поэтому существующая программа записи измеренных значений адаптирована и дополнена автоматическим контролем и регулированием силы и собственной частоты. Стратегия измерения, реализуемая с помощью этой программы, поясняется ниже.
Стратегия измерения с программой для автоматического регулирования испытаний
Во время длительных испытаний с автоматическим контролем силы и собственной частоты происходят различные этапы, каждый из которых приводит к различным необходимым режимам. На рис. 3 показана структура программы автоматического регулирования теста. Возможные режимы теста:
ручной режим без автоматического контроля уровня нагрузки для начального этапа длительных испытаний (этап I с рис.
1)
Испытание на нормальную вибрацию, включая сохранение измеренных данных
измерение функции частотной характеристики параллельно текущим вибрационным испытаниям
адаптация собственной частоты или амплитуды сигнала возбуждения
законченное испытание после достижения максимального чередования нагрузки или преждевременного окончания испытания
Структура программы для автоматического регулирования испытаний
Увеличенное изображение
Во время первой фазы вибрационных испытаний характеристики схватывания цементобетона приводят к быстрому уменьшению собственной частоты (см. фазу I на рис. 1). В этой фазе требуемая сила не будет достигнута в течение некоторого времени, поскольку скорость процесса адаптации ограничена. Поэтому вибрационные испытания сначала проводят в исходном ручном режиме, без автоматического контроля уровня нагрузки. Это означает, что генерируется синусоидальный свипирующий сигнал для возбуждения резонансной массы, а образец и значения измерений от описанных выше датчиков используются для определения текущей частоты частотных характеристик и начальной собственной частоты испытания. Как описано выше, после этого генерируется синусоидальный сигнал с определенной собственной частотой, амплитуда которого регулируется вручную на блоке управления гидравлическим возбудителем. Когда замечается падение амплитуды силы, запускается новое измерение частоты частот для ручной адаптации собственной частоты. После схватывания материала (что происходит в первые минуты виброиспытаний) можно включить автоматический контроль усилия.
При выполнении вибрационных испытаний с автоматическим регулированием усилия генерируется сигнал для возбудителя с текущей собственной частотой и заданной амплитудой, а значения измерений непрерывно собираются и сохраняются. Дополнительно определяется текущее количество циклов нагрузки для контроля продолжительности вибрационных испытаний.
Для контроля уровня силы при испытании для каждого интервала данных измерений проверяют, отличается ли амплитуда силы от требуемой нагрузки менее чем на 7 % и не происходит ли значительных и внезапных потерь амплитуды. Внезапная потеря амплитуды может быть вызвана макротрещинами в цементном бетоне или другими важными нарушениями вибрационных испытаний и, следовательно, является критерием преждевременного окончания вибрационных испытаний. Если обнаружено только отклонение амплитуды от требуемой силы более чем на 7 %, автоматически запускается новое измерение ЧЧХ, а контроль силы приостанавливается. Это означает, что снова собираются и сохраняются только значения измерений.
При этом к синусоидальному сигналу возбудителя добавляется сигнал белого шума, а текущее время сохраняется в протоколе измерений АЧХ. Когда возбуждение новым сигналом с добавлением белого шума длилось одну секунду, так что система успела успокоиться, программа переводится в режим измерения АЧХ. Это означает, что десять пакетов данных измерений собираются и используются для определения усредненной частотной характеристики и автоматического определения новой собственной частоты. Чтобы предотвратить ложное определение собственной частоты, обнаружение происходит только в заранее определенном диапазоне частот, который можно настроить перед началом виброиспытания. После этого вновь измеренная АЧХ сохраняется отдельно, а новая собственная частота добавляется в протокол измерений. Затем программа снова переключается в режим, в котором собираются и сохраняются только данные измерений, и выполняется один из двух различных возможных случаев: адаптация собственной частоты или адаптация амплитуды силы.
Если разница между старой и новой собственной частотой превышает 1 Гц, необходимо выполнить ступенчатую адаптацию частоты возбуждения. Частоту можно регулировать только с шагом в 1 Гц, иначе проблемы с блоком управления сигналами вызывают импульсообразные обрывы сигнала возбуждения. Если разница между старой и новой собственной частотой меньше 1 Гц, можно напрямую адаптировать частоту и запустить режим адаптации амплитуды. Адаптация амплитуды после установки новой собственной частоты необходима, поскольку изменение коэффициента усиления силы возможно при новой частоте возбуждения.
Сначала снова включается контроль силы, и соотношение требуемой и текущей силы используется для определения коэффициента масштабирования для адаптации амплитуды. Однако, если значение коэффициента масштабирования слишком велико, возникают те же проблемы, что и при адаптации частоты с шагом, превышающим 1 Гц. Таким образом, можно настроить максимальное и минимальное значение коэффициента масштабирования. Это ограничивает коэффициент масштабирования, используемый для адаптации амплитуды, но также делает необходимой адаптацию амплитуды в итерационных шагах до тех пор, пока либо не будет достигнута требуемая сила, либо не будет обнаружено изменение амплитуды силы в течение ряда последовательных шагов. В последнем предполагается, что достигается максимальная амплитуда гидровозбудителя. В этом случае в протоколе сохраняется автоматическая запись, и вибротест выполняется с текущей амплитудой до тех пор, пока не будет измерен новый АЧХ. Это может снова привести к другому изменению коэффициента усиления силы и, следовательно, возможно, что требуемая сила снова может быть достигнута.
Сигнал возбуждения прекращается либо после достижения максимального количества циклов нагрузки, либо после остановки теста вручную или автоматически. После этого оставшиеся интервалы данных измерений сохраняются и программа останавливается.
Первые испытания с активным автоматическим регулированием испытаний показывают, что программа значительно улучшает амплитуду приложенной силы к образцу. Развитие силы происходит гораздо более непрерывно и значительно ближе к требуемой амплитуде силы. На рис. 4 сравниваются результаты двух долгосрочных тестов — одного без автоматического регулирования теста и одного с активным автоматическим регулированием теста. Оба образца были подвергнуты последующей обработке в процессе автоклавирования, и требуемые усилия в обоих испытаниях были одинаковыми. Причина, по которой силы не идентичны, заключается в естественной разнице прочности на центральное растяжение между различными партиями цементобетона. И, как подробно описано ниже, прикладываемые уровни нагрузки определяются в процентах от центральной прочности на растяжение.
Валидация программы автоматического регулирования испытаний
Полноразмерное изображение
Для автоматического регулирования испытаний используется программное обеспечение LabVIEW, поскольку оно предлагает готовые к использованию интерфейсы для связи с используемыми измерительными системами. для сбора данных и управления гидравлическим возбудителем. Программа предлагает возможности ввода необходимых конфигураций для вибрационных испытаний, а также кнопки для запуска и завершения испытаний (см. рис. 5). Кроме того, сигнальные лампы и диаграммы с кривыми текущих измеренных значений визуализируют состояние текущего испытания.
Лицевая панель программы автоматического регулирования испытаний
Изображение в полный размер
План экспериментов по длительным испытаниям
Бетонные образцы для длительных испытаний были изготовлены и подвергнуты последующей обработке в Ibac . Выбранный бетон был UHPC с максимальным размером зерна 8 мм. Для исследований были изготовлены цилиндры диаметром 100 мм и высотой 300 мм, а затем плоскопараллельно отшлифованы. Из каждой партии образцов три образца использовали для определения среднего значения прочности на растяжение по центру. Это значение используется для определения максимальной деформации и, следовательно, амплитуды силы, прикладываемой к образцам во время длительных испытаний. После этого к каждому образцу прикрепляют две переходные пластины из стали (одну вверху и одну внизу образца). Соединение между адаптерными пластинами и образцом обеспечивается двухкомпонентным клеем на основе эпоксидной смолы. Пластины были дополнительно подвергнуты пескоструйной обработке перед склеиванием для достижения большей поверхности склеивания. Адаптерные пластины необходимы для крепления образца к резонансной массе вверху и к инертной массе внизу. При установке образца на испытательном стенде в WZL он подвергается сжатию в 2 кН, чтобы предотвратить повреждения из-за натяжения при затягивании винтов на переходных пластинах. После этого сжатие ослабляется, чтобы получить требуемую нейтральную предварительную нагрузку образца. Для начала длительных испытаний определяют начальную собственную частоту системы и задают требуемую динамическую нагрузку. Испытание завершается, когда 10 8 циклов нагрузки или ранее произошло разрушение образца бетона. В конце испытания определяют окончательную собственную частоту и, если видимой трещины образца не произошло, определяют остаточную прочность образца на растяжение при Ibac.
В предыдущих исследованиях, описанных в [12,13,14], образцы из обычного цементного бетона (NC) и UHPC (с добавлением и без добавления стальной фибры) были испытаны при различных амплитудах нагрузки. Результаты показывают, что динамическая нагрузка от 40 до 50% от центрального предела прочности на растяжение приводит к значительному повреждению образцов до достижения максимального количества циклов нагрузки. Это согласуется с результатами других исследований в области длительных испытаний с переменными нагрузками (с меньшей частотой) [11].
К бетону для использования в компонентах станков предъявляются высокие требования, особенно в отношении стабильности размеров, прочности на растяжение и усталости. Поскольку бетон дает усадку из-за гидратации, особенно в первые несколько дней после изготовления, в работе [12] были испытаны различные варианты твердения. Особое внимание уделялось термообработке и автоклавированию. Автоклавирование значительно увеличило прочность бетона на растяжение и сжатие. Кроме того, высокие температуры до 190 °С позволяли ускорить гидратацию и предвидеть усадочную деформацию [12].
Поэтому дальнейшие длительные испытания на испытательном стенде WZL с новым автоматическим регламентом испытаний были проведены с автоклавными образцами для исследования долговременной устойчивости к динамическим нагрузкам. Из-за больших усилий, связанных с продолжительностью испытаний, основное внимание было уделено образцам сверхвысокого давления с максимальным диаметром зерна 8 мм без стальных волокон. Состав смеси приведен в [12].
Для исследования влияния тестовой частоты использовались два разных уровня нагрузки. Для регулировки различных частот резонансная масса была адаптирована с помощью дополнительной массы, как описано выше. Для испытаний были выбраны резонансные массы массой 100 кг и 200 кг. Резонансная масса 100 кг приводит к начальной собственной частоте системы около 470 Гц, а масса 200 кг — около 320 Гц. Амплитуда знакопеременной нагрузки для испытаний была установлена в диапазоне 37–40 % и 41–45 % от ранее определенного центрального предела прочности при растяжении. Необходимо определить диапазон уровня нагрузки из-за допуска, заданного для регулировки нагрузки в регламенте автоматического испытания. Для сравнения с предыдущими исследованиями дальнейшие испытания проводятся с автоклавированными образцами с двумя уровнями нагрузки, но без автоматического регулирования испытаний. Кроме того, длительные испытания с новым автоматическим регламентом испытания и двумя различными уровнями нагрузки проводились на образцах, которые не подвергались автоклавированию, а хранились под водой после извлечения из формы до седьмого дня, а затем при 20 °C и 65 % отн. влажности до испытания (L7). Наконец, были проведены испытания с автоматическим регулированием испытаний, резонансной массой 100 кг и уровнем нагрузки 47–50% от центрального предела прочности на растяжение.
Определение предела прочности при центральном растяжении, а также проведение испытаний на усталость бетонных образцов сложны с точки зрения техники испытаний, особенно при приложении усилия. Кроме того, бетон является неоднородным материалом, а это означает, что при испытаниях может иметь место сравнительно большой разброс. Таким образом, было испытано шесть образцов из партии. Только в случае серии Л7 с меньшей амплитудой нагрузки исследовались три образца. В таблице 1 представлен обзор долгосрочных испытаний, проведенных в WZL.
Полноразмерная таблица
Оценка результатов испытаний больше не пригодны для станков, за исключением видимых и зияющих трещин. Однако в ходе длительных испытаний на стенде в образцах не возникало видимых трещин, даже если целевое усилие резко падало и не могло быть достигнуто, а испытания приходилось прекращать до достижения максимального числа циклов нагружения. Даже если достигнуто максимальное количество циклов, не очевидно, на какой фазе (см. рис. 1) усталостного поведения испытание было завершено. Теоретически возможно, что число 10
8 циклов нагрузки находится незадолго до окончания фазы II, а фаза III, где появляются видимые и зияющие трещины, достигается при еще нескольких циклах нагрузки. Следовательно, необходимо было определить другие критерии для оценки повреждения образца в ходе длительных испытаний.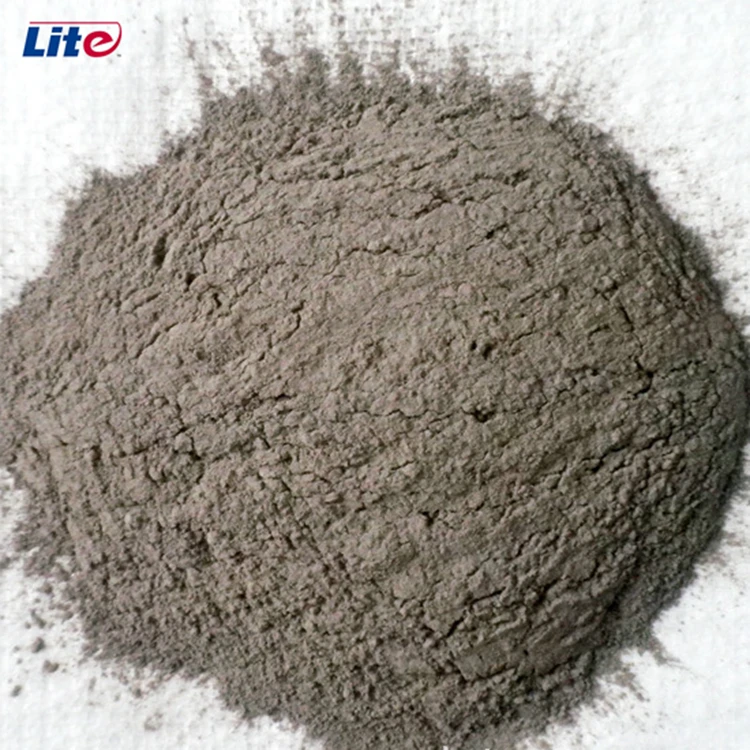
Для оценки долгосрочных испытаний учитываются различные аспекты измеренных значений. Как описано выше, остаточная прочность на разрыв образцов после окончания длительного испытания была испытана на Ibac, и было проанализировано процентное отклонение от среднего значения прочности на растяжение испытанной партии. Кроме того, собственная частота системы (образец + испытательный стенд) — как показатель жесткости образца — используется для оценки того, поврежден ли образец во время длительных испытаний. Жесткость в центральной точке инструмента (TCP) станков является важным критерием удобства использования станка. Следовательно, начальная собственная частота каждого испытания сравнивается со значением собственной частоты, измеренным непосредственно после испытания, и вычисляется процентное отклонение. Кроме того, измеренные ускорения в верхней и нижней части образца используются для расчета относительного смещения (удлинения или сжатия образца), и это относительное перемещение соотносится с фактической нагрузкой. Результирующее удельное удлинение/сжатие, подобно модулю Юнга, является характеристическим значением материала и должно быть постоянным в течение всего испытания. Поэтому отклонения на диаграммах удельного удлинения/сжатия свидетельствуют о повреждении бетона при длительном испытании. Пример графиков и значений оценки характеристик для длительных испытаний приведен на рис. 6. Поскольку граничные условия испытаний изменились, в том числе, в связи с применением нового автоматического регламента испытаний, процедура оценивания и критерии отличаются от анализа предыдущих тестов, описанных в [12].
Диаграммы и характеристические оценочные значения длительных испытаний неповрежденного образца
Изображение в полный размер
Наиболее очевидными критериями повреждения образца являются процентное отклонение предела прочности при растяжении после длительные испытания и процентное отклонение собственной частоты по отношению к начальной собственной частоте. Анализ результатов испытаний показывает, что если остаточное сопротивление растяжению после длительного испытания уменьшилось более чем на 45 % по отношению к среднему значению центрального предела прочности испытанной партии, то в большинстве случаев собственная частота уменьшилась более чем на 4 % по отношению к начальной собственной частоте. Поэтому каждый образец, для которого превышены эти два предела, оценивается как поврежденный образец. Даже если достигнуто максимальное число циклов нагрузки, маловероятно, что это значительное снижение предела прочности произошло только из-за рассеяния испытаний на определение предела прочности, поскольку снижение собственной частоты уже произошло. во время долгосрочного теста в этих случаях. Разброс результатов испытаний по определению предела прочности при растяжении также является причиной того, что предельное значение остаточной прочности при растяжении после длительных испытаний в 45 % установлено сравнительно высоким. Пример критериев оценки поврежденного образца показан на рис.
7.
Диаграммы и характеристические оценочные значения для длительных испытаний поврежденного образца
Изображение в полный размер
Образцы, для которых превышен только один предел (уменьшение частоты или уменьшение предела прочности) были автоматически остановлены до того, как они достигли максимального количества циклов нагрузки, далее анализируются в отношении конкретного удлинения/сжатия. Если в развитии удельного удлинения/сжатия обнаруживаются значительные отклонения в течение испытания, можно предположить, что в материале имеются значительные изменения, свидетельствующие о существующих или возникающих повреждениях образца. Эти экземпляры помечены как «вероятно» поврежденные. Если в дополнение к отклонениям удельного удлинения/сжатия уменьшение частоты и/или предела прочности при растяжении приближается к пределу 4 % или 45 %, образец оценивают как поврежденный.
Чтобы оценить, были ли образцы уже повреждены перед длительными испытаниями (например, во время погрузочно-разгрузочных работ или транспортировки), используется начальная собственная частота испытания аналогично [12]. Для каждой комбинации резонансной массы и образца с различной последующей обработкой рассчитывается среднее значение начальных собственных частот, а также среднее абсолютное отклонение этого среднего значения (см. Таблицу 2). Каждое испытание, имеющее начальную собственную частоту, меньшую, чем среднее абсолютное отклонение, вычтенное из среднего значения, поэтому является потенциально поврежденным и должно оцениваться отдельно. Если потенциально предварительно поврежденный образец дополнительно поврежден на очень ранней стадии длительных испытаний (менее 200 000 циклов нагрузки), этот факт является еще одним показателем того, что образец предварительно поврежден, и не должен учитываться при оценке.
Полноразмерная таблица
Один из 54 протестированных образцов был оценен как предварительно поврежденный и поэтому исключен из окончательной оценки. Как и ожидалось, образцы, испытываемые без регламента автоматического испытания, не могли должным образом выдерживать требуемый уровень нагрузки, поэтому среднее значение нагрузки, приложенной к образцу, должно было быть установлено как реально испытанное на уровне нагрузки. Этим объясняются образцы с низким уровнем нагрузки при оценке. К сожалению, также возникла проблема с партией автоклавированных образцов, которые должны были быть испытаны с центральным пределом прочности 41–45 %, резонансной массой 100 кг и активным автоматическим регулированием испытаний. Требуемый диапазон нагрузки не мог быть достигнут во время этих длительных испытаний. Вместо этого эти образцы также должны были быть испытаны при 37–40% прочности на центральное растяжение. Однако, по сравнению с испытанной партией с 50% центральным пределом прочности, все же возможно утверждение относительно предельного диапазона нагрузки при динамических длительных нагрузках на СВВД в высокочастотном диапазоне.
На рисунках 8 и 9 показаны результаты для различных конфигураций тестовых параметров. На диаграммах по вертикальной оси отложено количество испытанных образцов для соответствующих диапазонов уровня нагрузки по горизонтальной оси. Цвет столбцов на диаграммах указывает на оценку образцов как «поврежденные» (= красные), «вероятно поврежденные» (= желтые) или «не поврежденные» (= зеленые). Ниже диапазона уровней нагрузки 37–40 % большинство образцов оценивается как «неповрежденные», выше этого диапазона уровней нагрузки большинство образцов оцениваются как «поврежденные» или «вероятно поврежденные». Таким образом, оценка представленных испытаний показывает, что предел длительных нагрузок в высоком диапазоне частот лежит близко к 40% от центрального предела прочности при растяжении. Это означает, что общий предел длительных циклических нагрузок на UHPC, уже известный по частотам низкого уровня, по-видимому, применим и для частот высокого уровня, и что процесс автоклавирования и фактический диапазон высоких частот существенно не влияют на этот предел. Однако следует учитывать, что несколько поврежденных/вероятно поврежденных экземпляров уже встречались при 38% до 39% от центральной прочности на растяжение. Основываясь на результатах, при использовании UHPC для станков предел циклического нагружения в высокочастотном диапазоне должен быть установлен на уровне 36% от центрального предела прочности на растяжение, чтобы быть в безопасности.
Результаты длительных испытаний для различных конфигураций параметров автоклавированных образцов
Изображение полного размера
Рис. 9Результаты длительных испытаний для различных постобработок образцов изображение
Диэлектрическая проницаемость бетона в диапазоне от 50 МГц до 1 ГГц и измерения георадара для оценки строительных материалов
- title={Диэлектрическая проницаемость бетона в диапазоне от 50 МГц до 1 ГГц и измерения георадара для оценки строительных материалов},
автор={Антуан Робер},
journal={Журнал прикладной геофизики},
год = {1998},
объем={40},
страницы={89-94}
}
- A. Robert
- Опубликовано 1 октября 1998 г.
- Инженерный V. Schmidt, W. Wilting, M. Gruse, N. Wagner
Physics
- 2015
Разработан экранированный и защищенный конденсатор для неразрушающего измерения комплексной диэлектрической проницаемости цилиндрических образцов горных пород.
В сочетании с векторным анализатором цепей…
Влияние карбонизации бетона на электромагнитную диэлектрическую проницаемость, измеренную с помощью георадара и емкостных методов
В этом документе рассматривается влияние карбонизации бетона на распространение и рассеивание электромагнитных (ЭМ) волн, а также способность двух ЭМ неразрушающих методов обнаруживать это …
Новый планарный микроволновый датчик для комплексной характеристики диэлектрической проницаемости строительных материалов
- Жоао Г. Д. Оливейра, Ж. Г. Д. Джуниор, Э. Н. Пинто, В. П. С. Нето, А. Д’ассунсао
Материаловедение
Датчики
- 2020
Предлагается новый микроволновый датчик для определения комплексной относительной диэлектрической проницаемости строительных немагнитных материалов, который используется для определения характеристик трех образцов бетона в соответствии с имеющимися в литература.
Диэлектрическая проницаемость с использованием георадара.
0002 Цель этой статьи состоит в том, чтобы представить инновационный метод извлечения электромагнитной дисперсии строительных материалов с использованием георадара. Этот метод основан на соединении…
Большая коаксиальная отражательная ячейка для широкополосной диэлектрической характеризации крупнозернистых материалов
- Т. Боре, Х. Бхуян, Т. Биттнер, В. Мурган, Н. Вагнер, А. Шойерманн
Физика
- 2017
Знание частотно-зависимых электромагнитных свойств крупнозернистых материалов необходимо для успешного применения методов высокочастотных электромагнитных измерений для…
Измерение диэлектрической проницаемости вяжущих материалов и компонентов с помощью коаксиального зонда с открытым концом: сочетание экспериментальных данных, численного моделирования и емкостной модели коаксиальные зонды с открытым концом, предназначенные для исследования диэлектрической проницаемости бетона,…
Извлечение диэлектрической проницаемости волновода Дебая с расширенным частотным диапазоном для материалов с высокой комплексной диэлектрической проницаемостью: характеристика процесса схватывания бетона
Волновод с центральной частотой 868 МГц используется в режиме передачи/отражения для точного измерения поведения комплексной диэлектрической проницаемости гранул с высокой комплексной диэлектрической проницаемостью… с емкостными зондами
- Г.
Виллан, А. Ихамоутен, Ксавье Деробер
Материаловедение
- 2017
Влияние карбонизации бетона на георадарные и емкостные измерения
В данной статье рассматривается влияние карбонизации бетона на распространение и рассеивание электромагнитных электромагнитных волн. Емкостные датчики, работающие на низкой частоте (около 33 МГц) и георадар (антенна…
Разработка многолинейного квадратичного экспериментального плана для определения электромагнитных свойств бетона в диапазоне частот радара
- Xavier Dérobert, G. Villain
Материаловедение
- 2017
с показателем 1-10 из 18 ссылок
Сорт Byrelevancemost, повлиявшие на PapersRecency
Аналитическое моделирование диэлектрических свойств бетона.
- 1997
Оценка состояния железобетонных конструкций с использованием электромагнитных волн
- У. Халабе, К. Мазер, Э. Каусель
Машиностроение
- 1993
Износ железобетонной инфраструктуры является серьезной проблемой в Соединенных Штатах. Электромагнитные (ЭМ) волны продемонстрировали растущий потенциал для быстрой оценки состояния бетона…
Эффекты текстуры на мегагерцовые диэлектрические свойства образцов кальцитовой породы
- W. Kenyon
Физика, геология
- 1984
Диэлектрические свойства уплотненных затвердевших цементных материалов
- M. Pérez-Peña, D. Roy, A. Bhalla, L. Cross
Материаловедение
- 1986 мембрана
- T. Chung, C. Carter, T. Masliwec, D. Manning
Engineering
- 1994
- P. Sen
Геология
- 1981
- P. Sen, C. Scala, M. Cohen
Геология
- 1981
- G.
Weil
Материаловедение
- 1992
- К. Горур, М. Смит, Ф. Виттманн
Машиностроение
- 1982
- Полиуретан
- Асфальтовая краска
- Водонепроницаемый
- Заливка
- Водостойкое поверхностное покрытие
- Огнезащитные материалы
- Латексная краска
- Мощность сверла: 850 Вт
- Напряжение/частота: 220 В, 50 Гц
- Давление: 2 МПа
- Расход: 1-10 л/мин
- Объем бункера: 15 л
- Гранулированный материал: менее 2 мм
- Размер: 88 х 51 х 93 см
- Вес: 54/36 кг
Импульсный радар доказал свою эффективность при неразрушающем контроле мостовых настилов, состоящих из слоев диэлектрических материалов таких как асфальт, гидроизоляционная мембрана и железобетон. В…
Связь некоторых геометрических особенностей с диэлектрической аномалией горных пород
Показано, что действительная часть диэлектрической проницаемости e′ горных пород может быть аномально низкой частоты высокой из-за наличия небольшой концентрации η частиц с высоким аспектным отношением. Для сплющенного…
Автомодельная модель для осадочных пород с приложением к диэлектрической проницаемости расплавленных стеклянных шариков
Мы разрабатываем теорию диэлектрической реакции водонасыщенных пород на основе реалистичной модели порового пространства. Отсутствие порога перколяции проявляется в законе Арчи, прогнозах,… характер передачи фундаментального электромагнитного (ЭМ) поля и частотно-зависимый физический…
Неразрушающий контроль покрытий мостов, автомагистралей и аэропортов
При контроле металлов и металлов неразрушающий контроль материалов является принятым упражняться. Например, рентгенографический и ультразвуковой. Методы обычно используются для выявления аномалий в…
Микроволновое исследование гидратации цементного теста в раннем возрасте
AIKO 850W Насос для раствора и распыление цемента 50 Гц Hyvst
Наведите курсор на изображение, чтобы увеличить Нажмите на изображение, чтобы увеличить
Сэкономьте $-1118,20
AikoSKU: CS-SPA95
Поделитесь этим продуктом
AIKO 850 Вт растворонасос и распылитель цемента 50 Гц Hyvst | Модель: CS-SPA95
Особенности:
Технические характеристики:
Ваша платежная информация защищена. Мы не храним данные кредитной карты и не имеем доступа к информации о вашей кредитной карте.
Страна
Сингапур
Почтовый индекс
Возврат
Наш полис действует 7 дней. Если с момента покупки прошло 7 дней, к сожалению, мы не можем предложить вам возврат или обмен.
Чтобы иметь право на возврат, ваш товар должен быть неиспользованным и находиться в том же состоянии, в котором вы его получили. Он также должен быть в оригинальной упаковке.
Пожалуйста, сфотографируйте ваш товар, который нужно вернуть, и отправьте его через WhatsApp по номеру +65 8923 2880 вместе со счетом или доказательством покупки, чтобы мы могли его проверить.
На основании нашей оценки, если товары приемлемы, мы попросим вас доставить их в наш главный филиал по адресу: Блок 5022 Индустриальный парк Анг Мо Кио 2 #01-31 Сингапур (569525).
Некоторые виды товаров не подлежат возврату. Скоропортящиеся товары, такие как шлифовальные круги, защитная обувь, защитные каски, ремни безопасности, привязные ремни, сварочные электроды, силиконовые/акриловые герметики, сверла и т. д. возврату не подлежат. Мы также не принимаем товары интимного или санитарного назначения, опасные материалы, легковоспламеняющиеся жидкости или газы. Машины, работающие на бензине или дизельном топливе, также не подлежат возврату.
Дополнительные товары, не подлежащие возврату:
Подарочные карты
Загружаемые программные продукты
Некоторые товары для здоровья и личной гигиены
Для оформления возврата нам потребуется квитанция или подтверждение покупки.
Пожалуйста, не отправляйте покупку обратно производителю.
Существуют определенные ситуации, когда предоставляется только частичное возмещение (если применимо)
— Машины или инструменты с явными признаками использования
— Шлифовальные круги, отрезные диски, которые были вскрыты
– Любой товар, который не находится в исходном состоянии, поврежден или отсутствует по причинам, не связанным с нашей ошибкой.
– Любой товар, возвращенный более чем через 7 дней после доставки. и WhatsApp по телефону +65 8923 2880 вместе со счетом-фактурой или подтверждением покупки, чтобы мы могли его проверить.
На основании нашей оценки, если товары приемлемы, мы попросим вас доставить их в наш главный филиал по адресу: Блок 5022 Индустриальный парк Анг Мо Кио 2 #01-31 Сингапур (569525).
Если вы будете одобрены, ваш возврат будет обработан, и кредит будет автоматически применен к вашей кредитной карте или первоначальному способу оплаты в течение определенного количества дней.
Задержка или отсутствие возмещения
Если вы еще не получили возмещение, сначала проверьте свой банковский счет еще раз.
Затем свяжитесь с компанией, выпустившей вашу кредитную карту, может пройти некоторое время, прежде чем ваш возврат будет официально отправлен.
Далее обратитесь в свой банк. Часто перед отправкой возмещения требуется некоторое время на обработку.
Если вы сделали все это, но до сих пор не получили возмещение, свяжитесь с нами по телефону +65 8923 2880.
Предметы со скидкой
Возврат возможен только за товары по обычной цене, к сожалению, возврат за товары со скидкой невозможен.
Обмен
Мы заменяем товары, только если они неисправны или повреждены. Если вам нужно обменять его на тот же товар, отправьте нам электронное письмо по адресу [email protected] и отправьте товар по адресу: Aik Chin Hin Pte Ltd, 5022 ANG MO KIO INDUSTRIAL PARK 2 , #01-31, Сингапур 569.525, Сингапур.
Доставка
Чтобы вернуть товар, отправьте его по почте: Aik Chin Hin Pte Ltd, 5022 ANG MO KIO INDUSTRIAL PARK 2 , #01-31, Singapore 569525, Singapore
Вы будете нести ответственность за оплату своего товара. стоимость доставки для возврата вашего товара. Стоимость доставки не возвращается. Если вы получите возмещение, стоимость обратной доставки будет вычтена из вашего возмещения.
В зависимости от того, где вы живете, время, которое может потребоваться для того, чтобы ваш обмениваемый товар был доставлен к вам, может различаться.