Отопления стальные трубы: Стальные трубы для отопления. Плюсы и минусы. Разновидности стальных труб
Какие трубы отопления выбрать? Пластиковые или стальные?
В нашем суровом климате без хороших радиаторов и труб отопления не обойтись никак. Если выбор радиаторов отопления достаточно большой, то трубы отопления на отечественном рынке представлены двумя видами – стальными и пластиковыми. Какие из них считаются лучшими? В решении вопроса поможет сайт http://teploguru.ru/.
Стальные трубы отопления можно смело относить к нестареющей классике – их принято устанавливать в жилище еще с прошлого века. И действительно, если купить для собственного жилья качественные стальные трубы, то они способны прослужить в частном секторе, в котором имеется качественный теплоноситель в виде чистой воды, не менее 15-20 лет. Но здесь нужно быть внимательным – покупать нужно только бесшовные трубы, отличные повышенной прочностью, тогда как шовные варианты служат относительно недолго. При плановой замене изношенных труб отопления, чаще всего ЖЭКи стараются установить «бесплатно» именно шовные версии стальных труб, которые даже при теплоносителе хорошего качества от силы способны выдержать работу в течение нескольких лет! Лучше не рисковать и купить в строительном рынке или магазине бесшовную стальную трубу, привезти домой на багажнике автомобиля и далее отдать мастеру.
Но любые, даже лучшие версии стальных труб, неминуемо выходят из строя в результате воздействия коррозии. Когда важно заиметь в доме систему отопления, способную прослужить не менее несколько десятков лет, рекомендуется покупать для нее исключительно пластиковые трубы, которым вообще не свойственна коррозия. Но трубы из пластика встречаются разными и покупателю важно сделать правильный выбор. Самыми популярными с точки зрения формулы цена-качество считаются трубы из полипропилена. Они встречаются как однослойными, так и многослойными. Лучшими считаются последние версии, способные выдерживать серьезное давление теплоносителя, поскольку они имеют посередине между двумя слоями дополнительное карбоновое покрытие.
Можно купить и металлопластиковые трубы, у которых имеется усиливающий слой из алюминиевой фольги, но в силу не всегда высокого качества (у некоторых версий фольга вздувалась от конденсата) их не всегда рекомендуется покупать для городских тепловых сетей. Но что касается сельских отопительных систем, в которых теплоноситель циркулирует с пониженным давлением, покупка вышеуказанных труб изначально будет считаться лучшим решением.
Для современных многоэтажных домов, в которые подается теплоноситель под высоким давлением (не менее 30 атмосфер), лучшим выбором окажутся трубы из сшитого полиэтилена или PE-X, ценные тем, что отлично выдерживают как высокое давление теплоносителя, так и экстремально высокую температуру. Стоимость вышеуказанных труб удерживается на высокой отметке, но в силу их полезных эксплуатационных характеристик, они считаются лучшим выбором для городской застройки.
На правах рекламы
Основные диаметры стальных труб для системы отопления частного дома
Данный параметр очень важен для обеспечения эффективности обогрева. Неправильный выбор диаметров труб для отопления отражается на объеме теплоносителя (следовательно, увеличении затрат на эксплуатацию системы при превышении нормы), его скорости (возможно появление постоянных шумов), а также гидравлических потерях.
Чтобы уже после окончания первого же сезона не заниматься переделкой контура, следует сразу определиться с оптимальным сечением монтируемых изделий. Как это сделать и что учесть при выборе труб по диаметру – со всем этим поможет разобраться предлагаемая статья.
Рассматривается только вариант с трубами стальными. Если для системы используются изделия из других материалов (меди, пластиков), то численные значения будут несколько иными.
Что учесть при выборе диаметра труб
- К каждому товару прилагается спецификация, в которой отражены различные характеристики, в том числе, и размеры. Применительно к диаметру стальной трубы производители указывают только внутренний. Не путать с пластиковыми образцами, для которых в документации прописывается наружный!
- При расчетах необходимо в качестве ориентира брать выходной патрубок котла. Именно под величину его сечения подбираются образцы.
- Единой рекомендации по выбору диаметров стальных труб для отопительной системы быть не может по определению, так как все контура отличаются друг от друга, и нередко – принципиально.
Поэтому при монтаже сложной по конфигурации (схеме) системы следует пользоваться соответствующими таблицами и ориентироваться на тепловую нагрузку и пропускную способность. Например, если дом в 2 – 3 этажа и дополнительно производится отопление пристроенного гаража (сарая, теплицы, бани) одним теплогенератором. В подобных случаях вычисления производятся индивидуально, причем для каждой нитки (линии), и учитывается множество нюансов.
Для большинства частных домов сложными расчетами можно пренебречь, тем более что есть пределы допусков, которые позволяют ограничиться определением примерной величины диаметра на той или иной «нитке» и подобрать соответствующую продукцию из ассортимента.
Практика подтверждает, что допущенные погрешности не сильно влияют на функционирование небольшой по протяженности системы отопления. Поэтому можно отметить лишь основные моменты, которые нужно принять к сведению при определении диаметров труб из стали.
Рекомендации
- Диаметр трубы на входе котла («обратка») не может превышать аналогичную характеристику изделия, присоединяемого к его выходу – или такой же, или чуть меньше.
- Если на трассе имеются отводы (разветвления), то до первого из них сечение изделий не меняется (в случае соединения – сварного или резьбового – нескольких колен).
- Подключение любых приборов – отопительных (радиаторы), контрольных или технологических (расширительный бак) делается трубами ½ ».
На заметку!
Перевести дюймы в метрическую систему несложно. Достаточно значение диаметра (внутреннего!) умножить на 2,54 (см) или 25,4 (мм).
Примеры подбора диаметров стальных труб отопления
(варианты)
Приводить какие-либо формулы и примеры расчетов вряд ли целесообразно, так как не каждый читатель сможет самостоятельно оперировать исходными данными (а их еще нужно правильно определить). В принципе, вышеизложенной информации вполне достаточно, чтобы выбрать стальные трубы по диаметру для системы отопления небольшого частного строения.
ГОСТ 3262-75 — Трубы для изготовления газопроводов и водопроводов систем отопления
ГОСТ 3262-75 — Трубы для изготовления газопроводов и водопроводов систем отопления — ЧТПЗ
Популярные направления доставки
- Главная
- ГОСТы
- ГОСТ 3262-75. Трубы для изготовления газопроводов и водопроводов систем отопления
Трубы для изготовления газопроводов и водопроводов систем отопления
Государственный стандарт 3262-75 действует с 1977 года вместо утратившего силу ГОСТ 3262-62 и сегодня, после внесения уточняющих корректировок, полностью сохранил свою актуальность. Действие документа распространяется на стальные сварные трубы, в том числе – на образцы с оцинкованием и с накатанной цилиндрической резьбой, применяемые в ходе монтажа сетей и комплектующих инженерных коммуникаций – отопления, водо- и газоснабжения. Основное содержание стандарта – сведенные в таблицу взаимосвязанные параметры веса, толщины стенок и наружного диаметра. Подробно освещены требования к качеству и перечень допустимых отклонений.
Трубы для изготовления газопроводов и водопроводов систем отопления по ГОСТ 3262-75 от производителя
Чтобы приобрести стальной трубопрокат для монтажа трубопроводов сетей водоснабжения, поставок газа и отопления, просмотрите предложения Складского комплекса ЧТПЗ в каталоге. Постоянно в продаже – полный сортамент труб производства ЧТПЗ и ПНТЗ согласно ГОСТ 3262-75, полностью соответствующий нормативным техническим характеристикам и прошедший многоступенчатую проверку качества. Все заказы независимо от объемов выполняются в сжатые сроки. Возможно изготовление труб по размерам, заявленным заказчиком. Для получения дополнительных консультаций звоните 8 800 2345 005.
Популярные ГОСТы
ГОСТ 9567-75
Трубы прецизионные
ГОСТ 10498-82
Трубы бесшовные особотонкостенные из коррозионностойкой стали
ГОСТ 11017-80
Трубы стальные бесшовные высокого давления
ГОСТ 14162-79
Трубки стальные малых размеров (капиллярные)
ГОСТ 9941-81
Трубы бесшовные холодно- и теплодеформированные из коррозионностойкой стали
ГОСТ 21729-76
Трубы конструкционные холоднодеформированные и теплодеформированные из углеродистых и легированных сталей
ГОСТ 23270-89
Трубы-заготовки для механической обработки
ГОСТ 30564-98
Трубы бесшовные горячедеформированные из углеродистых и легированных сталей со специальными свойствами
ГОСТ 52079-2003
Трубы стальные сварные для магистральных газопроводов, нефтепроводов и нефтепродуктоводов
ГОСТ 8644-68
Трубы стальные плоскоовальные
ГОСТ 10704-91
Трубы стальные электросварные прямошовные
ГОСТ 10705-80
Трубы стальные электросварные
ГОСТ 8639-82
Трубы стальные квадратные
ГОСТ 10706-76
Трубы стальные электросварные прямошовные
ГОСТ 20295-85
Трубы стальные сварные для магистральных газонефтепроводов
ГОСТ 8645-68
Трубы стальные прямоугольные
ГОСТ 8734-75
Холоднодеформированные трубы
ГОСТ 8732-78
Трубы стальные бесшовные горячедеформированные
Заявка отправлена
В ближайшее время наш менеджер свяжется с вами
Отправить повторноМонтаж стальных труб отопления и водопровода своими руками: видео инструкция
Сталь – прекрасный и распространенный материал, в частности в качестве изделий для построения систем водоснабжения и отопления. И пусть сейчас появляется все больше новых материалов, дарящих повышенные эксплуатационных характеристики и простоту монтажа, стальные изделия остаются очень востребованными.
Стальные отопительные трубы
И пусть есть мнение, что такие детали имеют не очень большой срок службы, трубы, установленные еще во времена Союза, уверенно служат во многих домах, опровергая такое суждение.
Поэтому рассмотрим этот материал для труб отопления и водоснабжения, учитывая особенности монтажа.
Стальные отопительные трубы
Сталь широко используется для отопления уже давно. Они особенны тем, что могут выдержать значительные нагрузки при давлении и воздействии внешних факторов. При этом важно и то, что стоят они недорого.
При этом через металлические изделия можно пропускать жидкость, температура которой превышает сто градусов. Если же они замерзнут, то отогреть их нельзя даже открытым пламенем.
Конечно, не лишен этот материал и недостатков:
- Средний срок службы (в зависимости от условий эксплуатации) – пятнадцать лет.
Коррозия труб
- Нестойкий к коррозии.
- Нужна дополнительная теплоизоляция.
- Сложность придания нужной геометрической фигуры и установки.
В некоторых случаях имеет смысл исправить определенные недостатки, если это имеет значение. К примеру, если от прибора отопления до радиатора расстояние значительное. Теплоизоляция помогает сохранить тепло, сделав систему более эффективной.
В некоторых случаях спасает оцинковка, которая поможет избежать коррозии. Однако в таком случае исключается применение антифриза.
Рассмотрим эти изделия подробнее
Свойства оцинкованных труб
Это стальные трубы, покрытые цинком для стойкости к коррозии. Это позволяет существенно увеличить срок службы системы.
Оцинкованные трубы для систем отопления
Нужно отметить, что покрыть цинком можно не только сталь, а и, скажем, чугун.
Монтаж стальных труб отопления
Соединение таких изделий может быть выполнено двумя способами:
- Скруткой резьбой.
- Сваркой.
И тут нужно отметить, что в каждой методе есть свои тонкости и сложности, поэтому все процессы лучше доверить специалистам, которые умеют это делать.
Схема монтажа труб отопления
Если же монтаж нужно выполнить своими руками, тогда начинать нужно с проведения устройства стояков и укладки изделий. Если установка выполняется в квартире, то зачастую требуется замена этих элементов. Поэтому, если раньше была установлена отопительная система, потребуется лишь выполнить сварку.
В случае с оцинкованной сталью, применяется самозащитная проволока диаметром от 0,8 до 1,2 мм. В некоторых случаях используются электроды диаметром до 3 мм.
Сварка стальных труб выполняется внахлест, если их диаметр составляет до 2,5 см. В противном случае используется метод встык.
При этом большое значение имеет качество сварного шва. В этом основная сложность монтажа таких отопительных деталей. Особенно, если они находятся под давлением.
Сварка начинается с центра, с нижнего участка. Электрод нужно держать перпендикулярно месту сварки. Если шов выполняется в вертикальном положении, электрод должен находиться под углом вверх.
Горизонтальные участки соединяется проще всего.
Сварку нужно выполнять, проваривая металл, однако не прожигая его. Для этого нужно правильно выбрать марку (состав должен быть идентичным основному металлу, а также содержать примеси, которые улучшат характеристики шва), диаметр электрода, а также режим процесса. После окончания сварки шов нужно очистить от шлака.
Зачастую достаточно одного шва для труб, которые применяются в отопительных системах. Хотя можно сделать и два.
Сварка оцинкованных труб выполняется в среде защитных газов, поскольку в противном случае покрытие будет уничтожено, а значит, не будет защиты от коррозии.
Стальные изделия из нержавеющей стали можно соединить резьбовым способом, используя муфты, сгоны, угольники и прочие элементы.
Монтаж водопроводных труб
Первым делом нужно поменять вентиля. Следует отключить и сбросить стояки, открутить старые вентили.
Для обеспечения должной проходимости стояка водопровода в его направлении нужно осуществить прочистку тросиком. Дальше металлической щеткой защищаем резьбу, ее подматываем льном с применением олифы или эмали.
Безусловно, можно использовать и ленту ФУМ. Однако в этом варианте кроется опасность. Если будет малейший обратный ход, соединение будет течь. Приведенный выше способ проверенный и не имеет такого недостатка.
Лента ФУМ
Далее накручиваем вентиль и затягиваем разводным ключом очень аккуратно.
Если водопровод выполняется на несколько комнат, следует убедиться в достаточности диаметра отверстий в стене. Если нужно, их лучше сразу расширить.
Если прокладка водопровода будет выполняться под кафелем, нужно сделать штробы.
Фильтры
Чтобы все приборы, связанные с водопроводом, работали долго и надежно, рекомендуется устанавливать фильтры грубой очистки. Это особенно важно, если в доме есть водонагреватель. Это обязательное требование изготовителей.
Фильтр грубой и тонкой очистки
Подготовка труб и сборка
Полипропилен или металлопластик лучше отрезать по месту. Оцинкованную сталь подготавливать стоит заранее: отрезать и нарезать резьбы.
Соединять можно через обычный тройник или же через коллектор – разводка на отдельные приборы с запорной арматурой.
Варианты установки
Соединять, как уже отмечалось, своими руками можно при помощи сварки или резьбовых соединений.
Для сварки все же лучше обратить к сварщику, а резьбу можно нарезать вручную или же с применением токарного станка (если есть).
Заключение
Стальные трубы – прекрасный распространенный материал для создания систем отопления и водоснабжения. Однако стоит позаботиться о коррозийной стойкости, например, применив оцинкованную сталь.
Это увеличит срок службы, как и качественный монтаж. Если нужно выполнить все своими руками, дополнительно можно посмотреть видео инструкции. Тогда водопровод и отопление будет работать надежно долгие годы.
О трубах отопления, и энергонезависимости как о предрассудке
Основная проблема, связанная с применением современных котлов, их энергозависимость. Именно поэтому, на мой взгляд, отопление с естественной циркуляцией теплоносителя сохраняет свою привлекательность. В такой системе отопления теплоноситель нагреваясь в котле поднимается вверх, потом под действием гравитации опускается вниз через радиаторы обратно в котел. Котел стоит в самой нижней точке системы отопления. Горизонтальные трубопроводы в такой системе укладываются с уклоном в сторону котла по ходу движения теплоносителя. Основное отличие такой системы от отопления с принудительной циркуляцией теплоносителя заключается в больших диаметрах трубопроводов. Как следствие, такая система отличается высокой инерционностью в силу большого количества теплоносителя.
Трубопроводы большого диаметра применяются в системе отопления с естественной циркуляцией теплоносителя, чтобы снизить гидравлическое сопротивление. Однако, это имеет негативный побочный эффект. Теплоноситель в такой системе движется с очень маленькой скоростью, в силу чего он раскладывается на слои с высокой и низкой температурой. Именно поэтому в домах с естественным отоплением верхние этажи всегда теплее нижних. Кроме того, система отопления с низкой скоростью движения теплоносителя практически не поддается балансировке. Применение насоса решает проблему только в небольших системах, и не в полной мере.
Энергонезависимые котлы имеют следующие недостатки:
- Более высокая цена. (Если сравнивать котлы одного производителя.)
- Низкая экономичность. Применение автоматики может снизить эксплуатационные расходы на отопления до 30%.
- Низкая безопасность. Безопасность в таких котлах основана на механических способах защиты.
Итак, решаясь на применение стальных трубопроводов в отоплении, Вы получаете систему с неопределенным сроком службы, и более дорогую систему, потому что сварочные работы сегодня не дешевы.
Предпочитая энергонезависимую систему отопления, Вы обрекаете себя на большие затраты при ее покупке, так как большие диаметры труб дорого стоят, лишаете себя комфорта, поскольку, имея низкую скорость движения теплоносителя, практически невозможно обеспечить, чтобы все радиаторы вышли на расчетную мощность. Более того, Вы обрекаете себя на более высокие затраты, связанные с эксплуатацией системы отопления. Автоматика, без сомнения, делает отопление более экономичным.
Не нужно идти на такие жертвы, чтобы решить проблему энергозависимости современного отопления. Достаточно купить источник бесперебойного питания или генератор.
Неперехваченное исключение
После появления пластиковых труб, стальные стали использоваться все реже. Связано это с тем, что металлопластиковые или пропиленовые трубы проще устанавливать, не нужно красить, имеют меньшую шероховатость, поэтому стальные трубы применяются довольно редко.
Но, несмотря на все преимущества, пластиковые трубы обладают недостатками:
- Нужно защищать трубы от механического повреждения.
- Температура теплоносителя не может быть выше 70 градусов.
- Небольшой срок службы из-за низкого качества.
Но не все хотят использовать пластик. Что же осталось или металла? Например, стальная водогазопроводная труба. Ее можно сварить или соединить на резьбу. Но можно приобрести пресс-фитинги для удобного и быстрого соединения.
Труба под пресс-фитинги
ВГП трубу, соединенную пресс-фитингами можно использовать в котельной, где высокая температура носителя тепла. Такой вариант более интересный, чем полипропилен.
Кроме этого можно отметить трубу из нелегированной стали, которая оцинкована снаружи гальваническим способом. А также есть другой вид в пластиковой оболочке. Можно спрятать разводку в стяжку и не бояться удлинения труб при нагреве.
Несмотря на прочность труб, выполняется толстая теплоизоляция.
Гофрированная нержавейка
Следует отметить еще один вид труб из нержавеющей стали – гофрированная труба на резьбовых фитингах. Такие соединения не получится спрятать в стяжку. Но теплые полы выполняют из таких труб, а также лучевую разводку. Можно, конечно же, проложить их по стене, но внешний вид будет так себе. А в котельной использовать такие трубы очень удобно.
Стальные трубы выгодно отличаются от пластиковых тем, что могут выдержать температуру до 110 градусов. Таким образом, можно уменьшить диаметр трубопроводов. Если сравнить диаметр условного прохода стальных труб, то он дольше, чем у полипропиленовых такого же диаметра.
Стоит понимать, что металл всегда будет стоить дороже пластика. Произвести разводку таких труб трудно, а значит, и работа будет стоить недешево. Но срок эксплуатации стальных труб намного выше. Поэтому стальные трубы до сих пор используются в системе отопления.
Читайте также:
Знания о стальных трубах — процесс термообработки
Дата: 2019-06-17 Просмотр: 1592 Тег: Знания о стальных трубах — процесс термообработки
Процесс термообработкиОтжиг
Метод работы: после нагрева стали до Ac3 + 30 ~ 50 градусов или Ac1 + 30 ~ 50 градусов или ниже Ac1 (вы можете обратиться к соответствующей информации), она обычно медленно остывает вместе с печью температура.
Цели: 1. Уменьшить твердость, улучшить пластичность, улучшить производительность резки и обработки давлением; 2.Уточните зерно, улучшите механические свойства, подготовьтесь к следующему этапу; 3. Устранение внутреннего напряжения, вызванного холодной и горячей обработкой.
Области применения: 1. Применяется к легированной конструкционной стали, углеродистой инструментальной стали, легированной инструментальной стали, поковкам из быстрорежущей стали, сварным деталям и сырью с неудовлетворительными условиями поставки; 2. Обычно отжиг в холостом состоянии.
2. Нормализация
Метод работы: Сталь нагревают на 30–50 градусов выше Ac3 или Accm, а затем охлаждают до температуры, немного превышающей скорость отжига.
Цели: 1. Уменьшить твердость, улучшить пластичность, улучшить производительность резки и обработки давлением; 2. Уточните зерно, улучшите механические свойства, подготовьтесь к следующему этапу; 3. Устранение внутреннего напряжения, вызванного холодной и горячей обработкой.
Сферы применения: Нормализация обычно используется в качестве процесса предварительной термообработки поковок, сварных и науглероженных деталей. Для низкоуглеродистых и среднеуглеродистых конструкционных сталей и низколегированных сталей с низкими требованиями к характеристикам их также можно использовать в качестве окончательной термообработки.Для обычных средне- и высоколегированных сталей воздушное охлаждение может привести к полной или частичной закалке и, следовательно, не может использоваться в качестве окончательного процесса термообработки.
3. Закалка
Метод работы: Сталь нагревают до температуры фазового перехода Ас3 или Ас1, выдерживают в течение некоторого времени, а затем быстро охлаждают в воде, нитрате, масле или воздухе.
Назначение: Закалка обычно используется для получения мартенситной структуры высокой твердости. Иногда при закалке некоторых высоколегированных сталей (таких как нержавеющая сталь и износостойкая сталь) необходимо получить единую однородную структуру аустенита для повышения износостойкости. И коррозионная стойкость.
Области применения: 1. Обычно используется для углеродистой и легированной стали с содержанием углерода более 0,3%; 2. Закалка может полностью раскрыть потенциал прочности и износостойкости стали, но в то же время вызовет большое внутреннее напряжение. Чтобы снизить пластичность и ударную вязкость стали, необходимо провести отпуск, чтобы получить лучшие комплексные механические свойства.
4. отпуск
Метод работы: повторно нагреть закаленную сталь до температуры ниже Ac1 и после охлаждения охладить на воздухе или в масле, горячей воде и воде.
Задача: 1. Уменьшить или устранить внутренние напряжения после закалки, уменьшить деформацию и растрескивание заготовки; 2. Отрегулируйте твердость, улучшите пластичность и ударную вязкость и получите механические свойства, необходимые для работы; 3. Стабилизируйте размер заготовки.
Области применения: 1. Сохранение высоких температур и износостойкости стали после закалки с низкотемпературным отпуском; использовать среднетемпературный отпуск для повышения эластичности и предела текучести стали при условии сохранения определенной ударной вязкости; для поддержания высокой степени ударной вязкости и пластичности, а также высокотемпературный отпуск при достаточной прочности; 2. Сталь общего назначения не должна подвергаться отпуску при температуре 230 ~ 280 градусов, а нержавеющая сталь — при температуре 400 ~ 450 градусов, потому что это будет иметь хрупкость при отпуске.
5. Отпуск
Метод работы: высокотемпературный отпуск после закалки называется закалкой и отпуском, то есть стальная деталь нагревается до температуры на 10-20 градусов выше, чем во время закалки, закаливается после сохранения тепла, а затем закаляется при температуре от 400 до 720 градусов.
Цель: 1.Улучшить производительность резания и улучшить гладкость обработанной поверхности; 2. Уменьшить деформацию и растрескивание при закалке; 3. Получите хорошие комплексные механические свойства.
Области применения: 1. Подходит для легированной конструкционной стали, легированной инструментальной стали и быстрорежущей стали с высокой прокаливаемостью; 2. Может использоваться не только в качестве окончательной термообработки различных важных конструкций, но также и в качестве некоторых компактных деталей, таких как предварительная термообработка ходового винта и т. Д., Для уменьшения деформации.
WeChat picture_201
153502.jpg
6. Своевременность
Метод работы: Нагрейте сталь до 80 ~ 200 градусов, выдержите 5 ~ 20 часов или дольше, а затем выньте на воздух и охладите.
Назначение: 1. Стабилизировать микроструктуру стали после закалки, уменьшить деформацию при хранении или использовании; 2. Уменьшите внутреннее напряжение после закалки и шлифования и стабилизируйте форму и размер.
Области применения: 1. Подходит для закаленных сталей; 2.Обычно используется для плотных деталей, не требующих изменения формы, таких как тугие винты, измерительные инструменты, шасси станины и т. Д.
7. Холодная обработка
Метод работы: Закаленная стальная деталь охлаждается до -60-80 градусов или ниже в среде с низкой температурой (такой как сухой лед, жидкий азот), и температура становится однородной, а затем температура доводится до комнатной.
цель:
1. Восстановление всего или большей части остаточного аустенита в закаленной стали до мартенсита, тем самым увеличивая твердость, прочность, износостойкость и предел выносливости стали;
2. Стабилизируйте структуру стали, чтобы стабилизировать форму и размер стали.
Области применения:
1. После закалки стальные детали должны быть немедленно подвергнуты холодной обработке, а затем отпущены при низкой температуре для устранения внутренних напряжений во время низкотемпературного охлаждения;
2. Холодная обработка в основном применяется к компактным инструментам, калибрам и компактным деталям из легированной стали.
8. Закалка поверхности нагрева пламенем
Метод работы: пламя, которое горит смесью кислород-ацетилен, распыляется на поверхность стального элемента, быстро нагревается и распыляется для охлаждения сразу после достижения температуры закалки.
Цель: улучшить твердость поверхности, износостойкость и усталостную прочность стальных деталей, при этом сердцевина по-прежнему остается в твердом состоянии.
Области применения:
1. В основном используется для деталей из среднеуглеродистой стали, глубина закаленного слоя обычно составляет 2 ~ 6 мм;
2. Подходит для больших деталей при единичном или мелкосерийном производстве, а также для деталей, требующих частичной закалки.
9. Закалка поверхности с индукционным нагревом
Метод работы: стальная деталь помещается в индуктор, так что поверхность стальной детали генерирует индуцированный ток, который нагревается до температуры закалки за очень короткое время, а затем распыляется и охлаждается.
Цель: улучшить твердость поверхности, износостойкость и усталостную прочность стальных деталей и сохранить сердечную прочность.
Точки применения:
1. В основном используется для деталей из конструкционной стали из среднеуглеродистой стали и сплава Zhongtang;
2. Из-за скин-эффекта слой высокочастотной индукционной закалки и упрочнения обычно составляет от 1 до 2 мм, закалка на промежуточной частоте обычно составляет от 3 до 5 мм, а высокочастотная закалка обычно превышает 10 мм.
10. науглероживание
Метод работы: стальную деталь помещают в науглероживающую среду, нагревают до 900-950 градусов и изолируют, чтобы на стальной детали мог образоваться науглероживающий слой определенной концентрации и глубины.
Цель: улучшить твердость поверхности, износостойкость и усталостную прочность стальных деталей, при этом сердцевина по-прежнему остается в твердом состоянии.
Области применения:
1. Для деталей из низкоуглеродистой и низколегированной стали с содержанием углерода 0.От 15% до 0,25%, глубина науглероженного слоя обычно составляет от 0,5 до 2,5 мм;
2. После науглероживания необходимо провести закалку для получения мартенсита на поверхности для достижения цели науглероживания.
WeChat picture_201
153506.jpg
11. Азотирование
Метод работы: используйте на 5.. Активный атом азота, разложенный газообразным аммиаком при температуре ~ 600 градусов, насыщает поверхность стали с образованием нитридного слоя.
Назначение: Повышение твердости, износостойкости, усталостной прочности и коррозионной стойкости стальных деталей.
Области применения: в основном используется для конструкционной стали из среднеуглеродистого сплава, содержащей алюминий, хром, молибден и другие легирующие элементы, а также для углеродистой стали и чугуна, общая толщина нитридного слоя составляет 0,025 ~ 0,8 мм.
12. Азотирование
Принцип работы: одновременное науглероживание и азотирование поверхности стали.
Назначение: Повышение твердости, износостойкости, усталостной прочности и коррозионной стойкости стальных деталей.
Точки применения:
1. В основном используется для низкоуглеродистой стали, низколегированной конструкционной стали и деталей из инструментальной стали, обычно толщина слоя азотирования 0,02 ~ 3 мм;
2. Закалка и низкотемпературный отпуск после азотирования.
Пример 1: Схема термообработки для нескольких распространенных сталей
Q345: Сталь используется для строительства, мостов и т. Д., А предел текучести составляет около 345 МПа. Обычно оно нормализовано, и содержание углерода составляет около 0,12-0,2%.
20Cr: содержание углерода составляет около 0,2%, что позволяет использовать его в качестве конструкционной стали, которую можно использовать для нормализации. Его также можно использовать для науглероживания, науглероживания и закалки.
GCr15: Подшипниковая сталь, содержание углерода около 1%, температура закалки обычно составляет 860 ° C, низкотемпературный отпуск около 180 ° C.
60Si2Mn: пружинная сталь, содержание углерода около 0,6%, температура закалки 860 ° C, среднетемпературный отпуск (около 450 ° C).
0Cr18Ni9Ti: аустенитная нержавеющая сталь, содержание углерода менее 0.06%, обычно применяемые при обработке раствора при температуре около 1050 ° C (т.е. охлаждение греющей водой), улучшают коррозионную стойкость.
Пример 2: 45 #, 42CrMo, 20CrMo, как достичь требований к твердости 45HRC
Сталь45 # и 42CrMo могут подвергаться прямой закалке + отпуску для соответствия требованиям твердости 45HRC;
20CrMo может также соответствовать требованиям твердости 45HRC после науглероживания и закалки + отпуска.
Шестерни, изготовленные из 40CrMo.45 #, обычно нормализуются [или отпускаются] с поверхностным упрочнением.20CrMo науглероживается и закаливается. Он не только отвечает требованиям твердости. Этот тип деталей требует определенной контактной усталостной прочности.
Пример 3: Параметры процесса термообработки стали GCr15
СтальGCr15 представляет собой высокоуглеродистую хромистую сталь с меньшим содержанием сплава, хорошими характеристиками и широким применением. После закалки и отпуска он имеет высокую и однородную твердость, хорошую износостойкость и высокие характеристики контактной усталости. Холодная обработка стали средней пластичностью, режущая способность в целом, сварочные характеристики плохие, чувствительность к белым пятнам большая, и достигается отпускная хрупкость.
Химический состав / содержание элементов (%)
C: 0,95-1,05 Mn: 0,20-0,40 Si: 0,15-0,35 S:
Система термообработки: отжиг стального прутка, отжиг проволоки или 830-840 градусов закалка в масле.
Параметры процесса термообработки:
1. Обычный отжиг: нагрев 790-810 градусов, после охлаждения печи до 650 градусов, охлаждение на воздухе — HB170-207
2. Изотермический отжиг: нагрев 790-810 градусов, 710- 720 градусов изотермический, воздушное охлаждение — HB207-229
3.Нормализация: нагрев 900-920 градусов, охлаждение на воздухе — HB270-390
4. Высокотемпературный отпуск: нагрев 650-700 градусов, охлаждение на воздухе — HB229-285
5. Закалка: нагрев 860 градусов, закалка в масле — HRC62-66
6. Низкотемпературный отпуск: отпуск 150-170 градусов, воздушное охлаждение — HRC61-66
7. Карбонитрирование: 820-830 градусов совместной инфильтрации 1,5-3 часа, закалка в масле, криогенная температура от -60 до -70 градусов обработка от +150 градусов до +160 отпуск, охлаждение на воздухе — HRC ≈ 67
5 Процессы термообработки бесшовных стальных труб
Процесс термообработки бесшовных стальных труб в основном включает следующие 5 категорий: 1.Закалка + высокотемпературный отпуск
Стальную трубу нагревают до температуры закалки, чтобы преобразовать внутреннюю структуру стальной трубы в аустенит, а затем быстро охлаждают со скоростью, превышающей критическую скорость закалки, чтобы преобразовать внутреннюю структуру стальной трубы в мартенсит, а затем с высокой скоростью охлаждения. В результате термического отпуска структура стальных труб в конечном итоге преобразуется в однородную структуру из закаленного сорбита. Этот процесс может не только улучшить прочность и твердость стальной трубы, но также органично сочетать прочность, пластичность и ударную вязкость стальной трубы.
2. Нормализация
После нагрева стальной трубы до нормализующей температуры внутренняя структура стальной трубы полностью превращается в структуру аустенита, и затем происходит процесс термообработки, в котором в качестве среды для охлаждения используется воздух. После нормализации можно получить различные металлические структуры, такие как перлит, бейнит, мартенсит или их смешанная структура. Этот процесс может не только измельчить зерна, сделать состав однородным и устранить напряжение, но также повысить твердость стальной трубы и улучшить ее режущие характеристики.
После того, как стальная труба нагревается до температуры нормализации, внутренняя структура стальной трубы полностью превращается в структуру аустенита, а затем она охлаждается на воздухе, а затем согласовывается с процессом отпуска.

4. Отжиг
После того, как стальная труба нагревается до температуры отжига и выдерживается в течение определенного периода времени, она медленно охлаждается до определенной температуры вместе с печью, а затем выгружается из печи для охлаждения. Уменьшить твердость стальной трубы и повысить ее пластичность, чтобы облегчить последующую резку или обработку холодной деформации; Измельчение зерна, устранение дефектов конструкции, однородность внутренней структуры и состава, улучшение характеристик стальной трубы или подготовка к последующим процессам; Устраните внутреннее напряжение стальной трубы, чтобы предотвратить деформацию или растрескивание.
5. Раствор
Стальную трубу нагревают до температуры твердого раствора, так что карбиды и различные легирующие элементы полностью и равномерно растворяются в аустените, а затем быстро охлаждают, так что углерод и легирующие элементы слишком поздно для осаждения и термической обработки. процесс для единой аустенитной структуры. Функция процесса: выравнивание внутренней структуры стальной трубы и состава стальной трубы; Устранение затвердевания во время обработки для облегчения последующей обработки холодной деформацией; Восстановить коррозионную стойкость трубы из нержавеющей стали .
Термическая обработка стальной трубы
Термическая обработка стальной трубы
Традиционно считается, что на трубопрокатном заводе нет процесса термообработки, но на самом деле контролируемая прокатка и контролируемое охлаждение, нормализация в реальном времени и светлый отжиг оправки можно отнести к категории термической обработки. Кроме того, большинство компаний устанавливают линию термообработки на трубопрокатном заводе.
Контролируемая прокатка и контролируемое охлаждение — это новый процесс с 1980-х годов, который широко используется в производстве листов.Он в основном улучшает индекс прочности и вязкости за счет контроля температуры прокатки (в большинстве случаев необходимо комбинировать V, Nb, Ti и другие элементы с мелким зерном) и скорости охлаждения после прокатки.
Нормализация в оперативном режиме относится к нормализации (нормализации) термообработки на линии прокатки, то есть нагреву необработанной трубы до аустенизации и воздушного охлаждения на большом охлаждающем слое с помощью калибровочной машины для повышения прочности. Наиболее распространенными марками стали на трубопрокатных заводах являются материалы для муфт N80, класс I и K55.В настоящее время наша компания продолжает разработку обсадной колонны класса P110 из квазибейнита в режиме реального времени.
Определение и значение термической обработки
Термическая обработка стальной трубы — это технологический метод изменения внутренней структуры стальной трубы путем нагрева, изоляции и охлаждения стали в твердом состоянии для получения требуемых свойств. Как правило, в соответствии с требованиями цели процесс термообработки стали можно разделить на: отжиг, закалка + отпуск, закалка и отпуск, а также обработка поверхности.
Термическая обработка может полностью раскрыть потенциал стальных труб, улучшить эксплуатационные характеристики заготовки (стальной трубы), уменьшить вес заготовки (стальной трубы), сэкономить материалы, снизить затраты и продлить срок службы. С другой стороны, процесс термообработки также может улучшить производительность обработки, улучшить качество обработки и снизить износ инструмента. В то же время некоторые физико-химические показатели могут быть получены только после термической обработки. Такие как: высокая стойкость к коррозии под напряжением h3S, усиление труб из нержавеющей стали и т. Д.
Для нашей компании, будь то трубопрокатный завод или завод по переработке труб, процесс термообработки улучшает физические и химические показатели, такие как прочность и ударная вязкость стальных труб, чтобы удовлетворить требования пользователей и улучшить экономические преимущества. На трубопрокатном заводе оперативный процесс нормализации значительно упрощает технологический процесс и снижает производственные затраты; На трубоперерабатывающем заводе стальные трубы с высокой добавленной стоимостью в основном производятся путем закалки и отпуска, особенно специальные трубы для нефтепродуктов серии TP, не относящиеся к API, с коррозионной стойкостью, сопротивлением разрушению, стойкостью к коррозии и разрушению и сверхвысокой прочностью.
Основной принцип термообработки
Разработка процесса термической обработки металла
Внутренняя структура металлов и сплавов изменяется путем нагрева, сохранения тепла и охлаждения для получения структуры, необходимой для эксплуатационных характеристик деталей. Эта технология называется термической обработкой. Один и тот же материал может приобретать разные свойства после различной термической обработки. Изменение свойств происходит за счет изменения микроструктуры.Таким образом, понимание структурных изменений стали во время термической обработки является основой для правильной термической обработки.
Как и другие естественные науки, технология термической обработки металлов развивается вместе с ростом производительности и тесно связана с развитием других наук и технологий. Термическая обработка — это результат развития древней металлургической технологии. Как часть металлургической технологии, она постепенно превратилась в дисциплину.
В истории Китая технология термообработки появилась в железный век, вместе с появлением чугуна. Производство стали в древности осуществлялось обезуглероживающим отжигом и многократной ковкой чугуна, то есть так называемым «сотенным рафинированием в сталь». С развитием технологии выплавки стали была разработана и технология термообработки. Со времен династии Хань китайские технологии термообработки были зарегистрированы в письменной форме, включая общую технологию закалки, закалочную среду и процесс науглероживания, почти включая все аспекты технологии термообработки. Например, «огонь и вода погашены» содержится в исторических записях и в книге небесных дворцов.Согласно отдельной биографии Пу Юаня, Пу Юань сделал 3000 мечей для Чжугэ Ляна в наклонной долине вокруг уезда Мэйсянь провинции Шэньси. Он сказал: «Вода в Ханьчжуне тусклая и слабая и не угасает; Вода Шу прохладная и крепкая », поэтому он послал кого-то в Чэнду за водой. Закалка действительно резкая. Из текстовых исследований обнаруженных культурных реликвий и некоторых письменных записей можно ясно увидеть, что китайская технология термообработки имеет долгую историю и превосходные навыки, которые уступали таковым в других странах того времени.
Базовые теоретические знания по термообработке
Микроструктура стали
Кристаллическая структура металла
Материя состоит из атомов. По разному расположению атомов материю можно разделить на две категории: кристаллическую и аморфную. Расположение атомов в кристалле правильное, то есть «упорядоченное расположение». Это регулярное расположение называется кристаллической структурой; Расположение атомов в некристалле неправильное, то есть «неупорядоченное расположение».Расположение атомов обычно называют структурой решетки. Расположение атомов во всех металлах правильное. Следовательно, металлы относятся к кристаллам.
Существует две основные структуры решетки железа: объемно-центрированная кубическая решетка (α-FE) и гранецентрированная кубическая решетка (γ-Fe). Две структуры решетки показаны на рисунках 1 и 2.
Рис.1 объемно-центрированная кубическая решетка
Рис.2 гранецентрированная кубическая решетка
Металлографическая структура стали
Понятие «фаза»: компоненты с одинаковым химическим составом, кристаллической структурой и физическими свойствами в структуре металлического сплава. В области металлографии это называется металлографией, которая включает твердые растворы, соединения металлов и чистые элементы.
Понятие «организация»: оно обычно относится к целому, состоящему из одной или нескольких фаз с разными формами, размерами и режимами распределения, а также с различными дефектами и повреждениями материала, видимыми металлографическими методами.
Обычно мы называем сплав, состоящий из железа (FE) и определенного углерода (c), сталью, но углерод существует в стали в форме соединения железа и углерода (Fe3C).Из-за наличия углерода в стали он влияет на структуру решетки железа и формирует различные структуры. Как правило, все виды стальных конструкций вместе называются металлографическими структурами. Микроструктура стали иная, и ее свойства очень разные. Путем различной термической обработки стали можно получить разные конструкции и, наконец, получить нужные нам свойства. Основные конструкции из стали следующие:
- (1) Аустенит: твердый раствор гранецентрированной кубической структуры, образованный железом и другими элементами, обычно относящийся к комбинации углерода и других элементов.
Γ Твердый раствор внедрения в железе.
- (2) Феррит: твердый раствор объемно-центрированной кубической структуры, образованный железом и другими элементами, обычно относящийся к комбинации углерода и других элементов. Α Твердый раствор внедрения в железе.
- (3) Мартенсит: метастабильная фаза, превращенная из аустенита недиффузионным превращением. Фактически, это твердый раствор внедрения, в котором углерод перенасыщен железом. Кристалл имеет объемно-центрированную квадратную структуру.
- (4) Перлит: слоистая микроструктура с чередованием листов феррита и цементита.Это прямой продукт эвтектоидной реакции переохлажденного аустенита. Его также можно понимать как механическую смесь феррита и цементита.
- (5) Бейнит: полимеризованная структура феррита и цементита, разложенная переохлажденным аустенитом в диапазоне ниже температуры перлитного превращения и выше температуры мартенситного превращения. Верхний бейнит, разложившийся при более высокой температуре, называется верхним бейнитом, он перистый; Бейнит, разложившийся при более низкой температуре, называется нижним бейнитом, который похож на игольчатую структуру мартенсита низкотемпературного отпуска.
Кроме того, при фактическом производстве, в соответствии с требованиями к характеристикам продукта и специфическому процессу термообработки, в стали будут присутствовать другие структуры, такие как сорбит, троостит, гранулированный перлит, отпущенный мартенсит, отпущенный сорбит и т. Д. но эти структуры существенно не отличаются от вышеупомянутых базовых структур.
Превращение стали при нагреве
При отжиге, нормализации, закалке или науглероживании стальные детали необходимо сначала нагреть до аустенитного состояния.Аустенит — это твердый раствор атомов углерода в гранецентрированной кубической решетке железа. Состав, однородность, размер зерна, количество и распределение других фаз аустенита имеют большое влияние на процесс разложения, продукты разложения и свойства аустенита во время охлаждения. В то же время процесс нагрева стали также вызовет изменения качества и состава поверхности (окисление и обезуглероживание), что повлияет на эффект термической обработки детали.
Чтобы гарантировать, что термообработка может достичь ожидаемой цели, необходимо овладеть законами образования и роста аустенита во время нагрева стали и использовать эти законы для управления эффектом термообработки.
(1) Аустенитная формация
Температурный диапазон образования аустенита в стали во время нагрева в целом можно объяснить с помощью диаграммы состояния железоуглеродистого сплава (рис. 3). Из рисунка видно, что при нагревании эвтектоидной стали со структурой перлита от комнатной температуры до температуры ниже A1 не происходит никаких других структурных превращений, за исключением незначительного увеличения содержания углерода в феррите.Когда температура поднимается немного выше A1, перлит превращается в аустенит. Точно так же для доэвтектоидной стали с ферритом и перлитом при нагревании немного выше A1 перлит превращается в аустенит, а феррит не изменяется. При постоянном повышении температуры нагрева феррит продолжает превращаться в аустенит. Когда температура повышается до A3, весь феррит превращается в аустенит.
Рис.3 Диаграмма состояния железоуглеродного сплава
(2) Процесс образования аустенита
Преобразование перлита в аустенит можно условно разделить на четыре стадии, а именно: образование зародыша кристалла аустенита, рост кристаллов, растворение остаточного карбида и гомогенизация аустенит (рис.4).
Рис. 4 Процесс образования аустенита в эвтектоидной углеродистой стали
① Зарождение аустенита
Зарождение аустенита обычно происходит преимущественно на границе раздела фаз между ферритом и цементитом в перлите, поскольку атомы расположены нерегулярно на границе раздела фаз, это легко обнаружить получить условия энергии и концентрации, необходимые для образования аустенита. В изотермических условиях с увеличением времени зародыши аустенита растут с нуля, от меньшего к большему, и растут на границе раздела между ферритом и цементитом.
② Рост аустенита
После образования зародышей аустенита распределение углерода в аустените неравномерное.
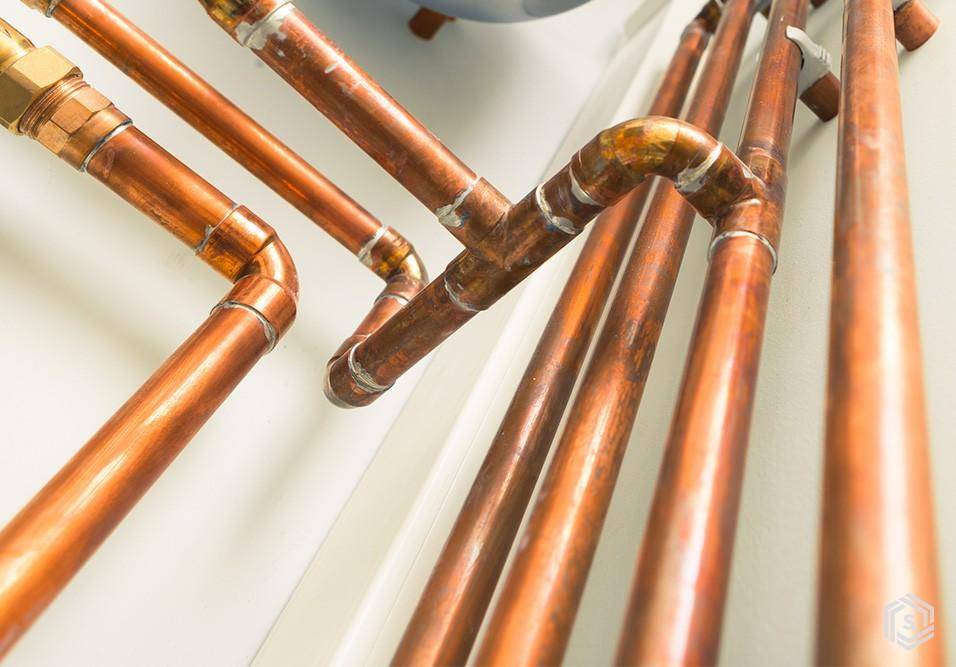
③ Растворение остаточного карбида (цементита)
В конце превращения перлита в аустенит в стали все еще остаются нерастворенные карбиды (цементит). Когда эвтектоидная сталь нагревается до температуры выше A1, начинает образовываться аустенит, но остаются карбиды. С течением времени карбиды продолжают растворяться, пока не исчезнут все.
④ Гомогенизация аустенита
Когда все остаточные карбиды растворены, концентрация углерода в аустените остается неравномерной.Содержание углерода выше в области исходного карбида и ниже в центральной области исходного феррита. Если мы продолжим увеличивать время, содержание углерода в аустените может постепенно стать однородным за счет диффузии углерода.

Микроструктура отжига доэвтектоидной стали представляет собой перлит и избыточный феррит.При медленном нагревании до AC1 перлит превращается в аустенит, который становится смешанной структурой аустенита и свободного феррита; При дальнейшем увеличении температуры и времени выдержки свободный феррит постепенно превратится в аустенит. Когда температура превышает AC1, свободный феррит полностью исчезает, и вся микроструктура представляет собой мелкие зерна аустенита. При дальнейшем увеличении температуры нагрева и времени выдержки зерно аустенита будет расти.
Микроструктура отжига заэвтектоидной стали представляет собой перлит и избыток цементита, в котором избыток цементита часто распределен сеткой.При медленном нагревании до точки AC1 перлит превращается в аустенит, который становится смешанной структурой аустенита и избыточного цементита; При дальнейшем повышении температуры и увеличении времени выдержки избыток цементита будет постепенно растворяться в аустените.

(3) Скорость образования аустенита
Чтобы контролировать состояние аустенитизации стали, необходимо понимать механизм образования аустенита. Скорость образования аустенита может быть отражена на изотермической диаграмме образования аустенита. На рис. 5 показано изотермическое образование аустенита в эвтектоидной стали. В левой части рисунка первая линия указывает, что 0.Образуется 5% аустенита, который может быть использован в качестве стартовой линии образования аустенита; Вторая линия указывает, что образуется 99,9% аустенита, который можно использовать в качестве конечной линии образования аустенита; Третья линия указывает на растворение остаточного карбида; Четыре линии показывают, что концентрация углерода аустенита в основном одинакова.

Рис. 5 Аустенит Изотермическое образование эвтектоидной стали
Из рисунка 5 видно, что время, необходимое для аустенизации, тесно связано с температурой изотермического превращения.Когда температура немного выше, чем A1, время аустенизации больше; Процесс аустенитизации ускоряется с повышением температуры.
Время образования аустенита меньше, время растворения остаточного карбида больше, а время гомогенизации аустенита больше. Взяв, например, изотермический режим 780 ℃, время образования аустенита составляет менее 10 секунд, но для полного растворения карбидов требуются сотни секунд, а для гомогенизации аустенита требуется 10000 секунд (около 3 часов).
Рис. 6 изотермическое образование аустенита в доэвтектоидной стали
В доэвтектоидной стали и заэвтектоидной стали диаграмма изотермического образования аустенита в основном такая же, как и для эвтектоидной стали. Однако доэвтектоидная сталь имеет свои собственные характеристики, как показано на рисунке 6, то есть в доэвтектоидной стали с высоким содержанием углерода конечная линия ферритного превращения и линия растворения остаточного карбида имеют характеристики пересечения.
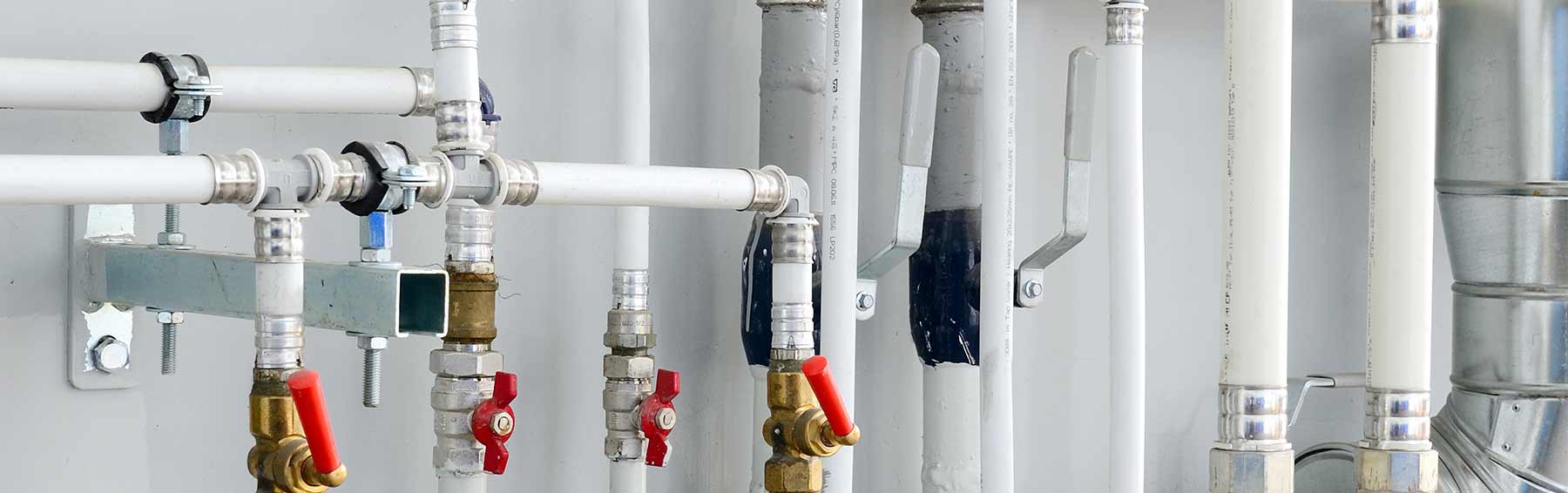
(4) Влияние различных факторов на образование аустенита
Образование аустенита — это диффузионный процесс. Все факторы, влияющие на диффузию, такие как температура и состав, будут влиять на образование аустенита.
1) Влияние температуры
Превращение перлита в аустенит следует закону зарождения и роста. Результаты показывают, что существует тесная взаимосвязь между скоростью зарождения аустенита (n), скоростью роста (g) и температурой изотермического образования.См. Таблицу 1.
Таблица 1 влияние изотермической температуры на параметры превращения аустенита
Температура перехода (℃) | Скорость зародышеобразования аустенита n (количество ядер) / мм (3.![]() | Скорость роста аустенита G (мм / с) | Время, необходимое для превращения в аустенит 50% (секунды) |
740 | 2280 | 0.0005 | 100 |
760 | 11000 | 0,01 | 9 |
780 | 51500 | 0,026 | 3 |
800 | 616000 | 0,041 | 1 |
В таблице указано, что с повышением температуры скорость зародышеобразования и скорость роста аустенита резко возрастают.Когда температура увеличивается с 740 ℃ до 800 ℃, скорость зародышеобразования (n) аустенита увеличивается примерно в 270 раз, а скорость роста (g) увеличивается примерно в 80 раз, что значительно увеличивает скорость превращения аустенита.
2) Влияние состава
A. Удар углерода
С увеличением содержания углерода в стали, соответственно, увеличивается количество цементита, а количество феррита относительно уменьшается. Поскольку общее количество границ раздела фаз между ферритом и цементитом увеличивается, превращение перлита в аустенит ускоряется.
B. Влияние легирующих элементов
Добавление легирующих элементов в сталь не изменяет процесс образования аустенита во время нагрева, но влияет на скорость образования аустенита.
Поскольку элементы из сплава меняют положение точек A1, A3 или ACM, некоторые элементы уменьшают точки A1, например, NL, Mn и т. Д .; Некоторые элементы увеличивают точку A1, например Cr, Mo, W и Si. При разработке процесса термообработки температура аустенизации должна быть соответствующим образом увеличена или уменьшена в зависимости от влияния элементов сплава на критическую точку.
Легирующие элементы влияют на коэффициент диффузии атомов углерода в аустените и растворение остаточных карбидов. Никель (Ni) не только снижает точку A1 и увеличивает перегрев, но также увеличивает коэффициент диффузии углерода в аустените, что ускоряет образование аустенита. Кремний (SI) и алюминий (AL) мало влияют на коэффициент диффузии атомов углерода в аустените, но они замедляют скорость образования аустенита, поскольку являются элементами, которые увеличивают A1 и уменьшают перегрев.
Хром (CR), молибден (MO), вольфрам (W), ванадий (V) и титан (TI) — это элементы, которые могут образовывать стабильные карбиды. Они не только повышают точку A1 и уменьшают перегрев, но также значительно снижают коэффициент диффузии углерода в аустените, тем самым значительно замедляя скорость образования аустенита. Вышеупомянутые элементы расположены в том порядке, чтобы стабильность образованных ими карбидов постепенно повышалась, и карбиды, образованные титаном (TI), были наиболее стабильными.Чем стабильнее образуется карбид, тем труднее его растворять и тем медленнее скорость образования аустенита. В реальном производстве, чтобы ускорить растворение стабильных карбидов, часто принимаются меры по значительному увеличению температуры нагрева.
C. Влияние исходной организации
Морфология и дисперсия карбидов в перлите влияют на количество границ раздела фаз феррита и цементита и расстояние между ними. При той же температуре, чем больше межфазных границ, тем выше скорость зародышеобразования; Чем меньше межслоевое расстояние, тем больше градиент концентрации углерода в аустените и тем выше скорость диффузии. Кроме того, чем короче расстояние диффузии, тем быстрее растет кристалл аустенита. Следовательно, чем мельче исходная структура, тем быстрее образуется аустенит.
Образование аустенита при непрерывном нагреве
В реальном производстве для термообработки стальных деталей в основном используется метод непрерывного нагрева. В случае непрерывного нагрева эксперименты показывают, что закон образования аустенита во время непрерывного нагрева в основном такой же, как и закон изотермического образования, но также имеет свои характеристики, в основном в следующих аспектах:
(1) Скорость нагрева во время непрерывный нагрев изменяет положение точек AC1, AC3 и ACM, которое обычно увеличивается с увеличением скорости нагрева, особенно точки AC3.
(2) Во время непрерывного нагрева аустенит образуется в определенном диапазоне температур, и с увеличением скорости нагрева температура пласта увеличивается, а диапазон температур пласта увеличивается.
(3) Исходная структура стали оказывает большое влияние на образование аустенита при непрерывном нагреве. Чем меньше дисперсия в исходной структуре, особенно в присутствии большого количества свободного феррита или цементита, гомогенизация аустенита будет переходить к высокой температуре.
Рост зерна аустенита и его контроль
Размер зерна аустенита влияет на микроструктуру и свойства продуктов его превращения. Утончение зерна может улучшить прочность и ударную вязкость стали. Поэтому изучение роста зерен аустенита имеет большое практическое значение.
(1) Понятие размера зерна аустенита
В зависимости от процесса образования и роста зерна аустенита размер зерна аустенита можно разделить на три типа: исходный размер зерна, фактический размер зерна и основной размер зерна.
Начальный размер зерна относится к размеру зерна аустенита, когда перлит только что превратился в аустенит. Как правило, исходный размер зерна аустенита относительно невелик и будет увеличиваться при нагревании или выдержке.
Фактический размер зерна относится к размеру зерна аустенита, фактически полученного сталью при специальной термообработке или в условиях горячей обработки. Его размер напрямую влияет на работоспособность стальных деталей. Фактические зерна, как правило, больше, чем исходные зерна, потому что обычно существует стадия нагрева и выдержки при производстве термообработки, во время которой зерна растут в разной степени.
У разных марок стали тенденция к росту зерна аустенита разная. Зерно аустенита некоторых сталей будет быстро расти с увеличением температуры нагрева, в то время как зерно аустенита некоторых сталей вырасти непросто. Сталь, имеющая тенденцию к росту аустенитного зерна, может быть разделена на две категории: основная мелкозернистая сталь и основная крупнозернистая сталь. Разница между этими двумя типами сталей заключается в следующем: в определенном температурном диапазоне аустенитные зерна крупнозернистых сталей непрерывно растут с повышением температуры, то есть тенденция к росту зерна значительна; Однако тенденция к росту зерна аустенита у обычной мелкозернистой стали мала с повышением температуры. «Существенный размер зерна» не является фактическим показателем размера зерна, но указывает на тенденцию роста зерна аустенита при определенных условиях.
В промышленном производстве сталь, раскисленная алюминием, в основном представляет собой мелкозернистую сталь, а сталь, раскисленную кремнием, является, по существу, крупнозернистой сталью. Кипящаяся сталь обычно представляет собой по существу крупнозернистую сталь, раскисленная сталь обычно представляет собой по существу мелкозернистую сталь, а по существу мелкозернистая сталь обычно используется для деталей, требующих термической обработки.
(2) Рост зерна аустенита и его влияющие факторы
Рис.7 схематическая диаграмма изотермического роста зерна аустенита
Рост зерна аустенита при высокой температуре является спонтанным процессом.Фактически, рост зерен аустенита — это в основном процесс миграции границ зерен. Следовательно, все факторы, влияющие на миграцию границ зерен аустенита, могут влиять на рост зерен аустенита.
Чем выше температура аустенизации, тем заметнее рост зерна. Когда зерно растет до определенной степени, даже если время выдержки продолжает увеличиваться, зерно аустенита не будет расти значительно, как показано на рисунке 7.
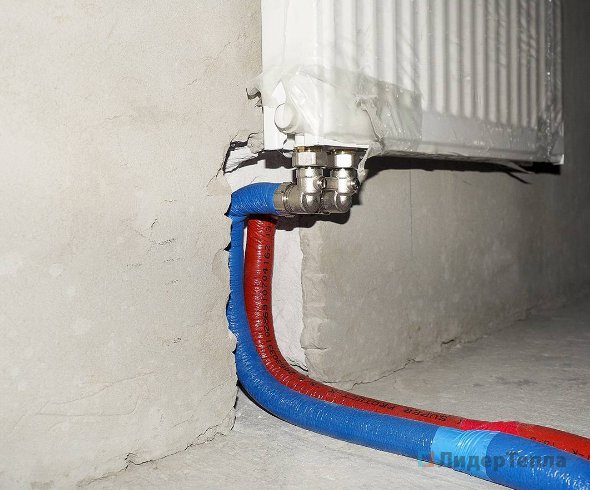
С увеличением содержания углерода в стали тенденция к росту зерна аустенита также увеличивается, но когда содержание углерода превышает определенный предел, зерно аустенита является мелким, потому что, когда содержание углерода превышает определенный предел, появляется нерастворимый цементит и цементит может расти.
Предотвратить миграцию границ зерен, чтобы зерна росли медленно, а фактические зерна аустенита были меньше.
Добавление в сталь легирующих элементов также влияет на рост зерен аустенита.Все элементы, образующие стабильные карбиды (такие как титан, ванадий, ниобий, вольфрам, молибден, хром и т. Д.), А также элементы, образующие оксиды и нитриды, нерастворимые в аустените (например, алюминий), будут препятствовать росту зерен аустенита. Марганец и фосфор ускоряют рост зерен аустенита. В современном промышленном производстве алюминий широко используется для контроля размера зерна аустенита. В стали, раскисленной алюминием, есть частицы с высокой температурой плавления, которые препятствуют движению границы аустенитного зерна и измельчают зерно.
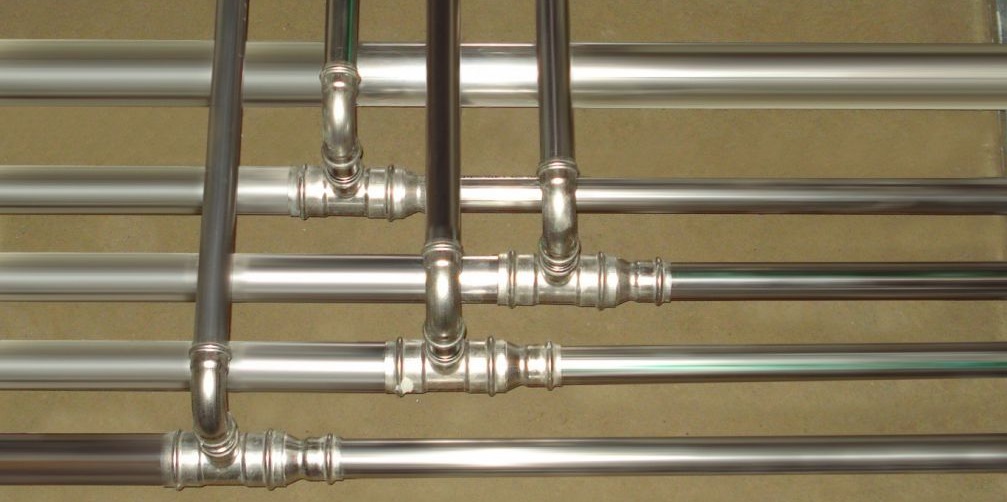
В заключение, влияние легирующих элементов на рост зерен аустенита следующее:
- Элементами, которые сильно препятствуют росту зерна, являются AI, Ti, Zr и V;
- Элементами, которые могут препятствовать росту зерна, являются w, Mo и Cr;
- Элементами, которые слабо препятствуют росту зерен, являются Si, Ni и Cu;
- Элементами, способствующими росту зерен, являются Mn (относится к высокоуглеродистым), P и C (относится к растворению в аустените).
(3) Меры по контролю роста зерна аустенита и измельчения зерна
1) Разумный выбор температуры нагрева и времени нагрева
Чем выше температура нагрева, тем выше скорость образования аустенита. Чем выше температура, тем больше тенденция к росту аустенита и тем крупнее фактическое зерно. Во время сохранения тепла рост зерен аустенита также происходит с увеличением времени сохранения тепла. Однако влияние температуры нагрева на рост зерна намного более значимо, чем влияние времени сохранения тепла, поэтому очень важен разумный выбор температуры нагрева.
Время, необходимое для образования аустенита и гомогенизации легированной стали, больше, чем у углеродистой стали, поэтому для легированной стали обычно требуется более длительное время нагрева.
2) Разумный выбор исходной микроструктуры стали
Исходная структура стали оказывает влияние на рост аустенитных зерен. Как правило, чешуйчатый перлит легче перегреть, чем гранулированный перлит, потому что чешуйчатый карбид быстро растворяется и быстро превращается в аустенит. После образования аустенита он начинает расти раньше.Таким образом, при производстве подшипниковая сталь и инструментальная сталь должны быть изначально изготовлены из гранулированного перлита. Одна из причин заключается в том, что такую структуру нелегко перегреть.
3) Добавьте определенное количество элементов сплава.
Рост зерен происходит за счет движения атомов границ зерен. Следовательно, рост зерен можно ограничить и задержать, добавив некоторые легирующие элементы.
Во-первых, добавленные легирующие элементы образуют в стали дисперсные соединения, такие как карбиды, нитриды, оксиды и т. Д.Эти дисперсные соединения механически препятствуют миграции границ зерен и росту зерен. Однако, как только эти соединения растворятся, блокирующий эффект исчезнет, и зерна начнут быстро расти. В это время скорость роста зерна даже больше, чем у по существу крупнозернистой стали. После горячей обработки (прокатка, ковка, литье, сварка и т. Д.) Зерна заготовки легко становятся крупными, что снижает ее механические свойства и отрицательно сказывается на окончательной термообработке. Зерна могут быть измельчены путем перекристаллизации.Например, для деталей из доэвтектоидной стали с крупными зернами зерна можно измельчить путем полного отжига (или нормализации).
Нагревательные дефекты стали (в том числе прокатный нагрев) и меры по их устранению
(1) Недогрев, перегрев и перегрев
Дефекты, такие как недогрев, перегрев и перегорание стали в процессе нагрева, в основном вызваны неточным или неисправным прибором температуры печи, неправильным методом загрузки и неравномерной температурой печи.
Так называемый недогрев означает, что феррит появляется в закаленной структуре доэвтектоидной стали, что приводит к недостаточному отклику закаленной стали; Для заэвтектоидной стали больше нерастворимых карбидов в закаленной структуре. Так называемый перегрев относится к укрупнению аустенитных зерен при нагревании стали, а крупный мартенсит получается после закалки, что делает заготовку хрупкой. Перегорание — это не только сильное укрупнение зерен аустенита, но также окисление границ зерен и даже плавление границ зерен, что приводит к списанию деталей.
Чтобы предотвратить эти дефекты, необходимо часто проверять приборы для измерения температуры и применять правильные характеристики нагрева и методы зарядки. Если во время нагрева сталь недостаточно нагревается или перегревается, ее можно однократно отжечь или нормализовать, а затем повторно закалить.
(2) Окисление и обезуглероживание
Окисление относится к процессу, при котором поверхность стали взаимодействует с кислородом, окисляющим газом и окисляющими примесями в теплоносителе с образованием оксида железа. Из-за образования окалины из оксида железа размер заготовки будет уменьшен, качество поверхности будет снижено, а скорость охлаждения во время закалки будет серьезно затронута, что приведет к появлению мягких пятен или недостаточной твердости. Хотя окисление стали представляет собой химическую реакцию, после образования оксидной пленки на поверхности стали скорость окисления в основном зависит от скорости диффузии атомов кислорода и железа через оксидную пленку. С повышением температуры скорость диффузии атомов увеличивается, а скорость окисления стали резко возрастает.Образующаяся оксидная пленка, особенно при температуре выше 600 ℃, состоит в основном из FeO, который не является плотным. Атомы кислорода и железа легко проникают внутрь через эту оксидную пленку, которая все толще и толще; Ниже 600 ℃ оксидная пленка состоит из относительно плотного Fe3O4, поэтому скорость окисления относительно низкая.
Обезуглероживание относится к окислению углерода в поверхностном слое стали, то есть к снижению содержания углерода в поверхностном слое. Чем выше температура нагрева, тем выше содержание углерода в стали (особенно когда есть больше элементов, таких как кремний, молибден и алюминий), сталь легче обезуглероживается.Из-за высокой скорости диффузии углерода скорость обезуглероживания стали всегда превышает скорость ее окисления. Под окислительным слоем стали обычно находится обезуглероживающий слой определенной толщины. Из-за обезуглероживания содержание углерода в поверхностном слое стали уменьшается, что приводит к недостаточной твердости поверхности и усталостной прочности после закалки, и на поверхности стальных деталей легко образуются поверхностные трещины.
Для предотвращения окисления и обезуглероживания можно использовать нагрев защитной атмосферы, вакуумный нагрев и нагрев упаковки для поверхностного покрытия в соответствии с требованиями и фактическим положением детали; При нагревании в соляной бане необходимо установить стандартную систему раскисления и регулярно добавлять раскислитель.
(3) Структура Видманштеттена
В процессе прокатки, если температура прокатки слишком высока, сетчатая структура Видманштеттена будет формироваться при определенной скорости охлаждения в последующем процессе охлаждения. Это значительно снизит индекс ударной вязкости. Решение — устранить его путем нормализации.
Применение термической обработки в трубопрокатном цехе
Контролируемая прокатка и контролируемое охлаждение — это новый процесс с 1980-х годов. Показатели прочности и вязкости в основном улучшаются за счет регулирования температуры прокатки (в большинстве случаев, V, Nb, Ti и других элементов с мелким зерном) и скорости охлаждения после прокатки.Типичным типом труб в нашей компании являются стальные трубопроводные трубы X52 ~ X60. В производстве цель усиления достигается за счет добавления V, Nb, Ti и других элементов или их комбинации с другими элементами.
Нормализация в оперативном режиме относится к нормализации (нормализации) термообработки на линии прокатки, то есть нагреву необработанной трубы до аустенизации и воздушного охлаждения на большом охлаждающем слое с помощью калибровочной машины для повышения прочности. Наиболее распространенными марками стали на трубопрокатных заводах являются материалы для муфт N80, класс I и K55. В настоящее время наша компания продолжает разработку обсадной колонны класса P110 из квазибейнита в режиме реального времени.
Точно так же, как развитие процессов нормализации в реальном времени, горячей загрузки и прямой прокатки, в настоящее время процессы термической обработки, такие как прямая закалка + отпуск после прокатки, будут постепенно применяться, чтобы значительно снизить потребление энергии.
Источник: Network Arrangement — Китайский производитель стальных труб — Yaang Pipe Industry Co., Limited (www.steeljrv.com)
(Yaang Pipe Industry — ведущий производитель и поставщик изделий из никелевых сплавов и нержавеющей стали, включая фланцы из супердуплексной нержавеющей стали, фланцы из нержавеющей стали, фитинги из нержавеющей стали, трубы из нержавеющей стали.Продукция Yaang широко используется в судостроении, атомной энергетике, морской инженерии, нефтяной, химической, горнодобывающей промышленности, очистке сточных вод, резервуарах для природного газа и высокого давления и других отраслях).
Если вы хотите получить дополнительную информацию о статье или поделиться с нами своим мнением, свяжитесь с нами по адресу [email protected]
Обратите внимание, что вас могут заинтересовать другие опубликованные нами технические статьи:
Термическая обработка стальных труб
Термическая обработка, также называемая термической обработкой, представляет собой метод, который ставит материалы в затруднительное положение в качестве среды для нагрева, сохранения тепла и охлаждения.Кроме того, это своего рода технический процесс, позволяющий контролировать характеристики материалов за счет изменения структуры поверхности ткани и внутренней организации.
- Производственная линия термообработки JST владеет двумя производственными линиями термообработки. Мы профессионально конфигурируем насосно-компрессорные трубы, обсадные трубы, соединительную арматуру, линейную трубу, бурильную трубу, внутреннюю котельную трубу национального стандарта, гидравлическую опорную трубу и напорный цилиндр для телевизоров.
Они производятся в соответствии со стандартами API для термообработки. Ассортимент вашей производственной линии для данной производственной линии термической обработки определен с наружным диаметром от 114 мм до 406 мм, а также длиной меньше или равной 13.5 м, а также другой, должен использовать внешний диаметр от φ48 мм до 180 мм и короче или равный 12,5 м. Может варьироваться в зависимости от производительности 2-х линий термообработки — 150 000 тонн и 50 000 тонн соответственно. Эта производственная линия также оснащена современным оборудованием для термической обработки с разницей температур внутри печи не более 5 ℃.
- Технологический процесс обработки тепла Склад труб → Закалка и нормализация нагрева → Закалка в воде → Отпускающий нагрев → Средство для удаления накипи под высоким давлением → Калибровка → Охлаждение → Правка → Охлаждение → Удаление окалины → Осмотр внутренней поверхности левого конца трубы → Осмотр конца трубы → Внутри Осмотр поверхности правого конца трубы → Осмотр корпуса трубы → Осмотр искусственной внешней поверхности → Гидростатическое испытание → Собрать и положить на хранение
Технологические особенности термической обработки
- Термическая обработка — действительно важный технологический процесс в механическом производстве.
По сравнению с другими методами обработки, он, как правило, не меняет форму обрабатываемой детали, фактически представляет собой интегрированное химическое соединение. Он может улучшить производительность за счет изменения внутренней микроструктуры заготовок или изменения химического компонента поверхности заготовки.
- Термическая обработка может снизить внутреннее качество исполнения изделия, которое невозможно обнаружить невооруженным глазом.
- Технология термообработки — еще одно неизбежное средство улучшения механических, физических и химических свойств деталей.
- Сталь — самый популярный материал в механической промышленности. Он обладает сложной микроструктурой и может контролироваться термической обработкой. Кроме того, алюминий, медь, магний, титан и их сплавы также могут получить новые механические свойства, физические свойства, химические свойства и эксплуатационные характеристики за счет термической обработки.
Термическая обработка холоднотянутых бесшовных стальных труб
Холоднотянутые бесшовные трубы используются для изготовления механической конструкции с высокой размерной точностью, гидравлического оборудования и высококачественных холоднотянутых или холоднокатаных прецизионных бесшовных стальных труб с хорошей обработкой поверхности.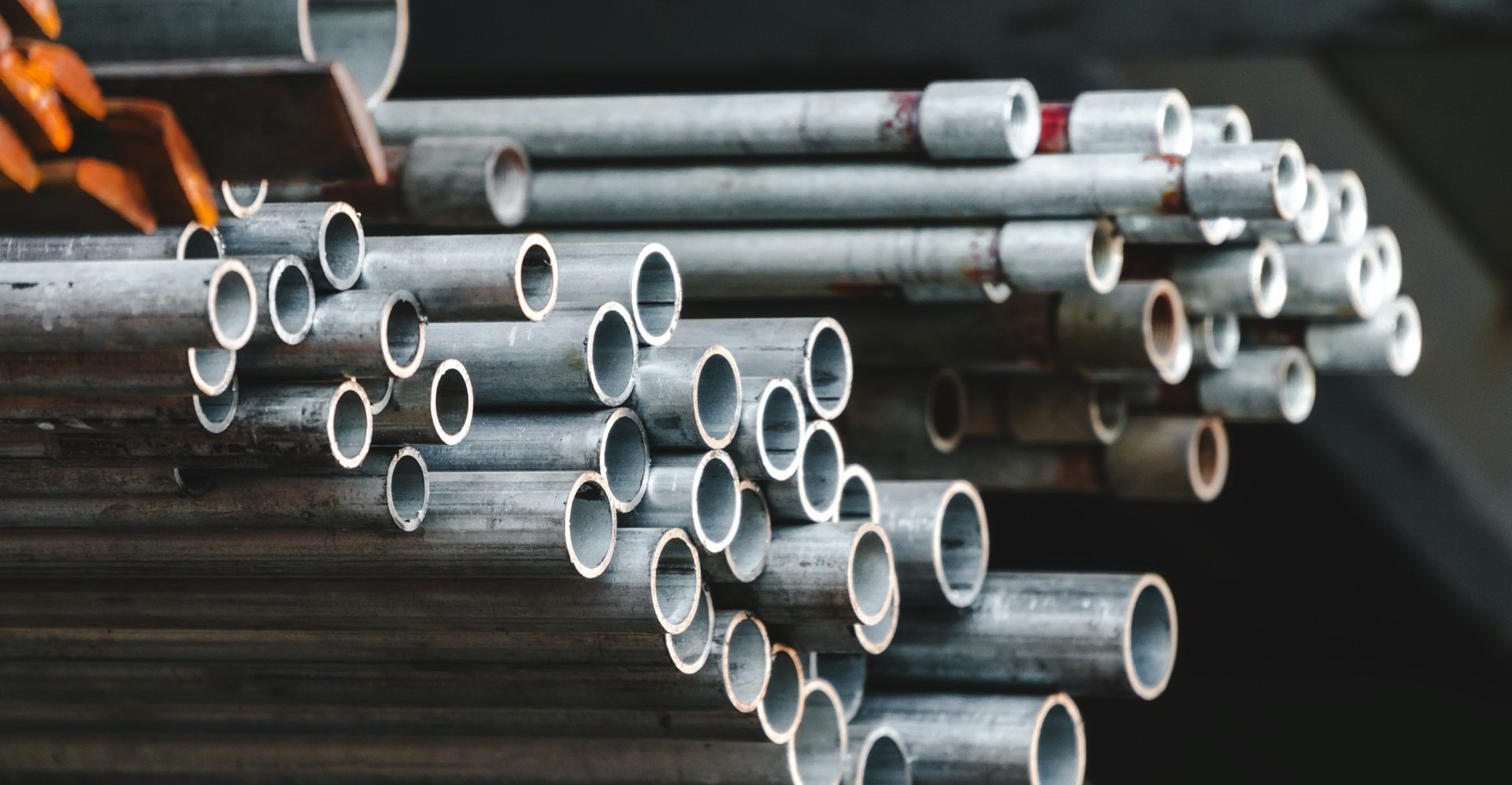
Термообработка стальных холоднотянутых бесшовных труб :
(1) холоднотянутой стали отжиг: относится к металлическому материалу нагревается до соответствующей температуры, чтобы поддерживать определенное время, а затем медленно охлаждают процесс термообработки. Общие процессы отжига: рекристаллизационный отжиг, снятие напряжений, шариковый отжиг, полный отжиг и так далее.Цель отжига: в основном для снижения твердости металлического материала, повышения пластичности или обработки резанием до обработки под давлением Liqie, уменьшения остаточного напряжения и улучшения однородности микроструктуры и состава, термообработки после возможной подготовки ткани.
(2) нормализация холоднотянутой стали: относится к нагреву стали или стали до Ac3 или Acm (критическая температура стали) свыше 30 ~ 50 ℃, по прошествии подходящего времени для сохранения прохлады на неподвижном воздухе в процессе термообработки. .Цель нормализации: в основном для улучшения механических свойств низкоуглеродистой стали, улучшения обрабатываемости, измельчения зерна, устранения дефектов тканей, подготовки к термообработке, после подготовки тканей.
(3) закалка холоднотянутой стали: относится к нагретой стали Ac3 или Ac1 (более низкая критическая температура стали) выше определенной температуры в течение определенного времени, затем соответствующая скорость охлаждения для получения ткани мартенсита (или тела термической обработки моллюсков) . Процесс закалки в ванне с поваренной солью включает закалку, мартенситную закалку, аустализацию, поверхностную закалку и частичную закалку.Цель закалки: сделать сталь необходимой для получения мартенсита повышения твердости, прочности и износостойкости заготовок, термической обработки, после подготовки к организации и подготовки.
(4) холоднотянутой стали закаленной: после закалки стали, а затем нагревают до температуры ниже Ac1, выдерживая определенное время, а затем охлаждают до комнатной температуры, процесс термообработки. Обычные процессы отпуска: отпуск, отпуск, отпуск и многократный отпуск. Цель отпуска: в основном сталь устраняет напряжение, возникающее при закалке, сталь имеет высокую твердость и износостойкость, но также обладает необходимой пластичностью и вязкостью.
(5) закаленная холоднотянутая сталь: относится к закалке и отпуску стали или процесса термообработки композитной стали. Используется при закалке указанной стали, закаленной и отпущенной стали. Обычно это относится к углеродистой структуре углеродистой стали и легированной стали.
(6) химическая обработка холоднотянутой стали: относится к деталям из металла или сплава, помещенным в постоянную температуру активной среды, так что один или несколько элементов на ее поверхности изменяют свой химический состав, микроструктуру и свойства тепла. процесс лечения.Обычные процессы химической термообработки: науглероживание, азотирование, нитроцементация, проплавление алюминированного бора. Цель химической обработки: основная — повысить твердость поверхности стали, износостойкость, коррозионную стойкость, усталостную прочность и стойкость к окислению.
(7) обработка холоднотянутым стальным раствором: сплав нагревается до высокотемпературной однофазной области для поддержания постоянной температуры, так что избыточная фаза полностью растворяется в твердом растворе после быстрого охлаждения, чтобы преодолеть процесс термообработки перенасыщенного твердого раствора.Цель обработки на твердый раствор: в основном для повышения пластичности и вязкости стали и сплавов, для подготовки к обработке дисперсионным упрочнением и т. Д.
Отжиг, нормализация и закалка стальных труб
Отжиг, нормализация и закалка стальных труб
Что такое отжиг стальной трубы? Какие виды и способы применения отжига?
Answe r:
Отжиг стальной трубы : отжиг — это процесс термообработки, при котором стальная труба нагревается до температуры выше или ниже критической точки AC1 и медленно охлаждается вместе с печью после выдержки в течение определенного времени для получения структуры, близкой к равновесному состоянию.
Тип отжига: в зависимости от температуры нагрева, его можно разделить на отжиг выше или ниже критической температуры AC1. Первый включает полный отжиг, неполный отжиг, сфероидизирующий отжиг, гомогенизирующий отжиг, а второй включает рекристаллизационный отжиг и отжиг для снятия напряжения. По режиму охлаждения его можно разделить на изотермический отжиг и отжиг с непрерывным охлаждением.
Цель отжига:
- 1.Полный отжиг: полный отжиг — это процесс термообработки, при котором стальная труба нагревается до 20-30 ℃ выше AC3 в течение достаточно длительного времени, после чего структура полностью аустенитизируется, а затем медленно охлаждается в печи, чтобы получить структуру, близкую к температуре. состояние равновесия. Он в основном используется для изготовления доэвтектоидной стали. Его цель — измельчение зерна, устранение внутренних напряжений и деформационного упрочнения, улучшение пластической вязкости, даже химического состава и структуры стали, улучшение режущих характеристик стали и устранение дефектов, таких как структура видманштеттена и полосчатая структура в среднеуглеродистой конструкционной стали.
- 2. Неполный отжиг: неполный отжиг — это процесс термообработки, при котором стальная труба нагревается до ac1-ac3 (доэвтектоидная сталь) или ac1-accm (заэвтектоидная сталь) и медленно охлаждается в печи после выдержки в течение определенного периода времени для получить структуру, близкую к равновесному состоянию. Для доэвтектоидной стали, если исходное структурное распределение стали подходит, можно использовать неполный отжиг вместо полного отжига для устранения внутренних напряжений и снижения твердости.Для заэвтектоидной стали основной целью неполного отжига является получение сферической перлитной структуры, устранение внутренних напряжений, снижение твердости и улучшение характеристик обработки.
- 3. Сфероидизирующий отжиг: сфероидизирующий отжиг — это процесс термообработки, направленный на формирование сфероидального карбида в стальной трубе и получение гранулированного перлита. Он в основном используется для обработки эвтектоидных сталей, заэвтектоидных сталей и легированных инструментальных сталей.
Его цель — снизить твердость, улучшить характеристики резки, выровнять структуру и подготовить к закалке.Обычный процесс сфероидизационного отжига применяется для стальных труб общего назначения.
- 4. Гомогенизационный отжиг: также известный как диффузионный отжиг, это процесс термообработки, при котором слитки, отливки или кованые заготовки нагреваются до температуры немного ниже температуры твердой фазы в течение длительного времени, а затем медленно охлаждаются до комнатной температуры. Его цель — устранить сегрегацию дендритов и региональную сегрегацию в процессе затвердевания слитка или отливки, чтобы гомогенизировать состав и структуру.
- 5. Рекристаллизационный отжиг: процесс термообработки, при котором холодно деформированный металл нагревается выше температуры рекристаллизации в течение определенного времени, а затем медленно охлаждается до комнатной температуры. Его цель — преобразовать деформированные зерна в однородные равноосные зерна, устранить деформационное упрочнение и остаточное внутреннее напряжение, а также восстановить структуру и свойства стали до состояния, существовавшего до холодной деформации.
- 6. Отжиг для снятия напряжений: процесс термообработки, при котором металл холодной штамповки стальной трубы нагревается до определенной температуры ниже температуры рекристаллизации, выдерживается в тепле в течение определенного периода времени, а затем медленно охлаждается до комнатной температуры.Его основная цель — устранить остаточное внутреннее напряжение (в основном первое внутреннее напряжение) в стальных трубах, отливках, кованых и катаных деталях, сварных деталях и обработанных деталях, чтобы улучшить стабильность размеров и снизить склонность к деформации и растрескиванию заготовки.
Что такое нормализация стальных труб? Какая цель? Какие есть приложения?
Ответ:
Нормализация стальной трубы: нормализация заключается в том, чтобы нагреть стальную трубу до соответствующей температуры выше AC3 или Accm и нагреть ее в течение определенного времени для завершения аустенитизации.Затем процесс термообработки перлитоподобной ткани осуществляется путем охлаждения на высокой скорости (воздушное охлаждение, воздушное охлаждение или распыление). Суть нормализующего процесса — полная аустенизация и псевдоэвтектоидное преобразование.
Цель: улучшить зерно, однородный состав и структуру, устранить внутренние напряжения, отрегулировать твердость, устранить дефекты, такие как видманштеттеновая структура, полосчатая структура и сетчатый карбид, и обеспечить подходящую микроструктуру для окончательной термообработки.
Заявка:
- 1.Повышение эффективности резки труб из низкоуглеродистой стали.
- 2. Устранение дефектов горячей обработки (видманштеттеновая структура, полосчатая структура, крупное зерно) труб из среднеуглеродистой стали.
- 3. Исключен чистый карбид из заэвтектоидной стальной трубы, что удобно для сфероидального отжига стальной трубы и подготовки к закалке стальной трубы.
- 4. В качестве окончательной термообработки он может улучшить механические свойства обычных стальных труб.
Обычным методом повышения прочности доэвтектоидной стали является увеличение содержания перлита в доэвтектоидной стали.

Ответ:
Следует использовать процесс нормализации.
Причина: переохлажденный аустенит доэвтектоидной стали будет выделять доэвтектоидный феррит в процессе охлаждения. Чем ниже скорость охлаждения, тем больше содержание доэвтектоидного феррита, что приводит к меньшему содержанию перлита и снижению твердости и прочности доэвтектоидной стали.Суть нормализующего процесса — полная аустенизация плюс псевдоэвтектоидное преобразование. За счет увеличения скорости охлаждения содержание доэвтектоидного феррита может быть уменьшено, а доэвтектоидная сталь может быть преобразована в эвтектоидную структуру, то есть содержание перлита увеличивается, поэтому прочность и твердость доэвтектоидной стали могут быть улучшены.
Для чего нужна закалка? Сколько существует методов закалки? Сравнить преимущества и недостатки нескольких методов закалки?
Ответ:
Целью закалки стальной трубы является получение как можно большего количества мартенситов, которые могут значительно улучшить прочность, твердость и износостойкость стальной трубы. В сочетании с различными процессами отпуска сталь может иметь высокую прочность, твердость и пластическую вязкость.
Когда сталь нагревается до определенной температуры выше критической точки AC3 или AC1 и охлаждается со скоростью охлаждения, превышающей критическую скорость охлаждения после выдержки в течение надлежащего времени, процесс термообработки для получения мартенсита (или низшего бейнита) называется закалка.
Метод закалки: в соответствии с методом охлаждения, его можно разделить на метод одинарной закалки в жидкости, метод двойной закалки в жидкости, метод ступенчатой закалки и метод изотермической закалки
Сравнение достоинств и недостатков:
Метод закалки | Преимущество | Недостаток |
Закалка в одной жидкости | Простое управление и широкое применение | 1. 2. Сильное гасящее напряжение. 3. Выбрать охлаждающую способность и охлаждающие характеристики подходящей охлаждающей жидкости непросто. |
Метод двойной жидкой закалки | 1 Уменьшите нагрузку на ткани и уменьшите склонность к деформации и растрескиванию заготовки. 2. Подходит для обработки деталей большого размера. | Операцию нелегко контролировать, и она требует богатого опыта и квалифицированных технологий. |
Метод ступенчатой закалки | 1. Уменьшите термическое напряжение и напряжение ткани, уменьшите склонность заготовки к деформации и растрескиванию. .2. Управлять операцией относительно легко. | Только для меньшей заготовки. |
Изотермическая закалка | 1. 2. Подходит для обработки деталей сложной формы и точных размеров. | Только для меньшей заготовки. |
Обсуждается принцип выбора температуры закалки для доэвтектоидной и заэвтектоидной стали. Почему температура закалки заэвтектоидной стали не может превышать линию ACCM?
Ответ:
Принцип выбора температуры закалки и нагрева:
Для получения мелкой мартенситной структуры принцип заключается в получении ровных и мелких зерен аустенита.Доэвтектоидная сталь обычно нагревается до 30-50 ℃ выше AC3, а заэвтектоидная сталь до 30-50 ℃ выше AC1.
- 1. Если температура закалки заэвтектоидной стали превышает линию ACCM, все карбиды растворятся в аустените, что приведет к увеличению содержания углерода в аустените, уменьшению точек MS и MF стали, увеличению количества остаточного аустенита после закалки и уменьшению твердость и износостойкость стали
- 2.
Заэвтектоидная сталь имеет высокую температуру закалки, укрупненное зерно аустенита и высокое содержание углерода.После закалки легко получить крупнозернистый игольчатый мартенсит с микротрещинами, что снижает пластическую вязкость стали.
- 3. Во время высокотемпературной закалки тепловое напряжение закалки велико, а обезуглероживание является серьезным, что также увеличивает склонность к деформации и растрескиванию стальных деталей.
Что такое закаливаемость и закаливаемость стали? Факторы, влияющие на прокаливаемость, прокаливаемость и глубину прокаливаемости стали?
Ответ:
Прокаливаемость: закаливаемость стали относится к способности аустенитизированной стали получать мартенсит во время закалки, что отражает стабильность недостаточно охлажденного аустенита и связано с критической скоростью охлаждения стали.Его размер выражается глубиной закаленного слоя и распределением твердости, полученным закалкой стали при определенных условиях.
Прокаливаемость: закаливаемость стали относится к способности аустенитизированной стали закаливаться во время закалки, которая в основном зависит от содержания углерода в мартенсите, выраженного максимально возможной твердостью закаленного мартенсита.
Глубина закаленного слоя: глубина закаленного слоя относится к глубине от полумартенситной зоны до поверхности детали, измеренной во время закалки стали при определенных условиях.Это связано с закалкой стали, формой и размером заготовки, а также охлаждающей способностью закалочной среды.
Источник: Китайский производитель стальных труб — Yaang Pipe Industry Co., Limited (www.steeljrv.com).
(Yaang Pipe Industry — ведущий производитель и поставщик изделий из никелевых сплавов и нержавеющей стали, включая фланцы из супердуплексной нержавеющей стали, фланцы из нержавеющей стали, фитинги из нержавеющей стали, трубы из нержавеющей стали. Продукция Yaang широко используется в судостроении, атомной энергетике, судостроении. машиностроение, нефтяная, химическая, горнодобывающая промышленность, очистка сточных вод, резервуары для природного газа и высокого давления и другие отрасли.)
Если вы хотите получить дополнительную информацию о статье или поделиться с нами своим мнением, свяжитесь с нами по адресу [email protected]
Обратите внимание, что вас могут заинтересовать другие опубликованные нами технические статьи:
Труба из нержавеющей стали со швом или бесшовная — для нагревательных элементов — промышленное применение
Основной продукцией нашей компании являются бесшовные трубы из нержавеющей стали и специальных сплавов для промышленного использования. Мы используем самое современное производственное оборудование для обработки нержавеющей стали, коррозионно-стойких сплавов, титановых сплавов, бесшовных труб из жаропрочных сплавов (горячая экструзия / прошивка + холодная прокатка / холодное волочение) и линий по производству сварных труб, таких как формовка FFX и JCO. Мы стремимся поставлять высокопроизводительные, коррозионно-стойкие, устойчивые к давлению, термостойкие трубы из нержавеющей стали для нефтегазовой, электроэнергетической, СПГ, энергетического оборудования, а также нефтехимической, химической, судостроительной и различных других отраслей.
TOPE обеспечивает высочайшее качество сварных труб, бесшовных труб, овальных труб и полос из нержавеющей стали , наша продукция широко используется в электрических нагревателях, нагревательных элементах, пароперегревателях, теплообменниках, конденсаторах, химической, легкой и других отраслях промышленности, ежегодно производственная мощность 8000 тонн.Наше обязательство — сократить время выполнения заказа, обеспечивая большую гибкость. Потребности наших клиентов на первом месте, поэтому любая работа не является слишком маленькой.
Характеристики
Наружный диаметр : Φ2 мм — Φ30 мм ;
Толщина стенки : 0,1 мм — 2 мм ;
Давление: 70 МПа — 120 МПа
Допуск внешнего диаметра: +/- 0,05 мм
Допуск толщины стенки: +/- 0,05 мм
Состояние поставки: мягкая, средне-мягкая, твердая.
Поверхность трубок: первоначальный цвет после кислотной очистки, полированная.
мин. Количество: Без ограничений
Материал
Нержавеющие стали классифицируются в соответствии с их металлургической структурой: аустенитные, ферритные, мартенситные, дисперсионно-твердые и дуплексные.Аустенитные нержавеющие стали содержат хром и никель. Они закалены только при холодной обработке и немагнитны, хотя некоторые из них могут стать магнитными при холодной обработке. Поставляемые нами материалы указаны ниже.
Трубы из нержавеющей стали, классифицированные по способам производства
Основное испытательное оборудование
Для обеспечения качества продукции основное испытательное оборудование включает в себя гидравлическую испытательную машину WE-100, машину для испытания под давлением, термометр в дальнем инфракрасном диапазоне, стереомикроскоп, твердомер и все другие измерительные инструменты, которые соответствуют производственным потребностям.
Все трубки прошли 100% -ные испытания на вихревые токи и гидравлические испытания. Мы предлагаем нержавеющую трубку высочайшего качества. Строгие проверки и испытания процесса гарантируют высочайшее качество для наших клиентов.
Как отличить качество нержавеющих трубок для ТЭНов
Качество трубы из нержавеющей стали очень важно при производстве электронагревательных элементов. Материал трубы из нержавеющей стали является основой для определения качества трубы из нержавеющей стали.Качество нержавеющей стали в основном зависит от разницы в содержании никеля. Никель — качественный коррозионно-стойкий элемент. Его идеальное взаимодействие с хромом в нержавеющей стали дополнительно укрепляет коррозионную стойкость и стойкость к кислотам и щелочам, но для низкоуглеродистой никелевой стали для получения чистой аустенитной структуры содержание никеля должно достигать 24%, и только когда содержание никеля достигает 27%, он может существенно изменить коррозионную стойкость стали в определенных средах. Следовательно, для трубки нагревательного элемента, если требуется коррозионная стойкость и стойкость к высоким температурам, вы можете выбрать сплав 800, сплав 840, SUS316L и другие материалы, содержание никеля в трубке из сплава 800 составляет 30%, сплав 840 — 20%, 316L составляет 10%, но если вы используете трубку из нержавеющей стали 304, которая содержит только 8% никеля, качество будет очень плохим.
Достоинства нагревательных элементов из нержавеющей стали: хорошая термостойкость, стойкость к сухому горению и относительно невысокая стоимость. В настоящее время существует множество типов нагревательных элементов из нержавеющей стали, и разница в цене на различные материалы велика.Для того же материала из нержавеющей стали качество и производительность по-прежнему значительны. Поэтому при покупке труб из нержавеющей стали для нагревательных элементов нам необходимо проверить конкретное содержание элементов, чтобы не допустить некачественной продукции по высоким ценам. Трубы из нержавеющей стали трудно отличить невооруженным глазом, так как же определить материал труб из нержавеющей стали? Могут использоваться следующие методы:
Первый — простой тест
1.
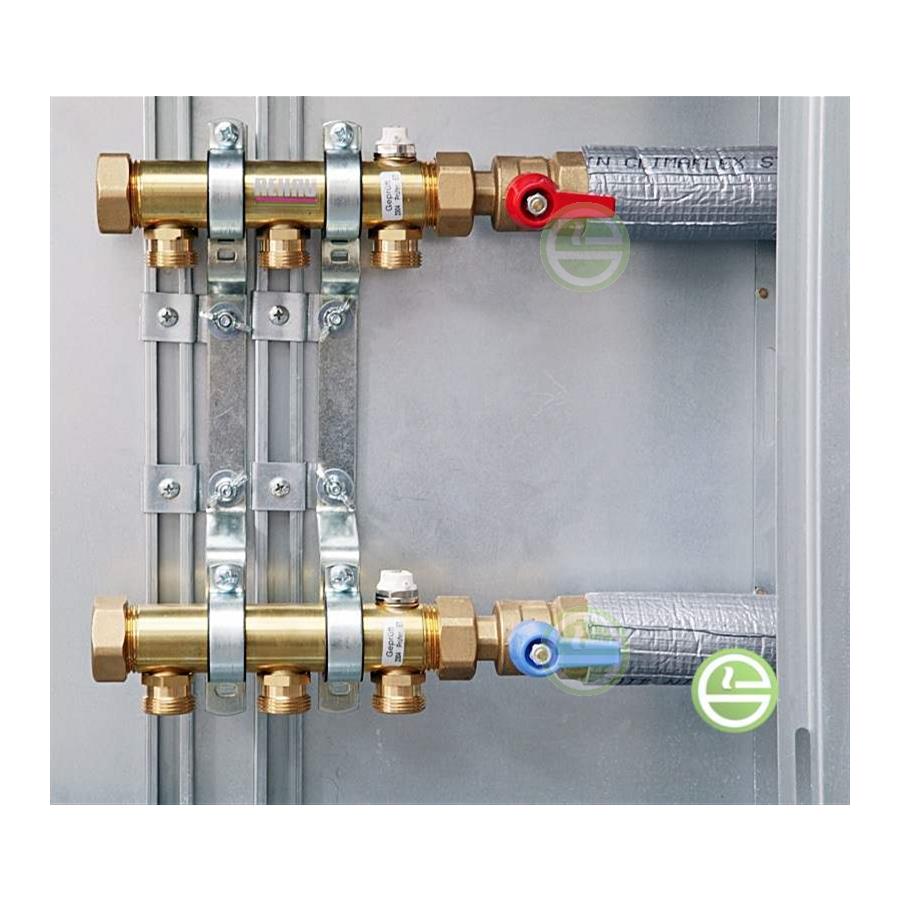
Магнетизм SUS 316 и SUS 304 очень мал.
2. Точечный тест на азотную кислоту:
Это наиболее интуитивно понятный метод проверки коррозионной стойкости подложки посредством определения точки азотной кислотой. Как правило, хорошая труба из нержавеющей стали будет лишь слегка подвергаться коррозии во время испытания, а труба из нержавеющей стали с самой низкой коррозионной стойкостью будет иметь явные следы коррозии.
3. Измерительный раствор из нержавеющей стали:
Также называется жидкостью для обнаружения трубок из нержавеющей стали. Убедитесь, что на поверхности трубки из нержавеющей стали нет пятен.После того, как избавитесь от покрытия поверхности, используйте каплю жидкости. Наблюдайте за изменением цвета нержавеющей стали в зоне испытания и сравните цвет трубки из нержавеющей стали и время покраснения.
4. Наблюдать за искрами:
Качество трубы из нержавеющей стали также можно отличить по искре и твердости во время резки или сварки.
Второй — процесс производства трубы из нержавеющей стали
1.Яркость полировки:
Чем ярче яркость, тем более гладкая поверхность и чем меньше площадь окисления, тем выше коррозионная стойкость.
2. Азотная защита сварочной линии:
Большая часть коррозии труб из нержавеющей стали начинается на сварочной линии, поэтому защита сварного шва азотом может эффективно улучшить коррозионную стойкость трубы из нержавеющей стали.
3. точность:
Хотя точность не имеет прямого отношения к коррозионной стойкости трубы из нержавеющей стали, чем выше точность трубы из нержавеющей стали, тем лучше процесс и выше качество.
Информация для заказа:
1. Материал трубы?
2. Диаметр трубы * толщина * длина?
3. Количество для заказа?
Отраслевые стандарты
.