Производство электродов сварочных: Технология производства сварочных электродов – линии, прессы и прочее, технология изготовления в цеху и домашних условиях, как наладить бизнес, где купить
Как производят сварочные электроды | Сварка своими руками
Производство электродов для сварки процесс наукоемкий и требующий наличия различных видов оборудования.
Сам сварной электрод состоит из металлического прутка и напрессованного на него покрытия. В процессе сварки электроток протекает по прутку, плавит его и металл детали, а обмазка защищает зону сварки от кислорода. Такая простая физика лежит в основе электродуговой сварки плавлением.
С изготовлением электродов дела обстоят гораздо сложнее, чем с их плавлением. Начинается все с того, что проволока, поступающая в специальный протяжный автомат, вытягивается в ровный пруток, который на выходе обрезается в размер электрода. Рубка проволоки на стержни осуществляется на правильно-отрезных автоматах. Рубщик контролирует их параметры, отсортировывая отбракованные. Полученные стержни проходят контроль ОТК.
Пожалуй, это самый несложный этап технологического процесса. Стержни поступают к электродным прессам. Они загружаются в подающий механизм.
Остается нанести покрытие. Пусковые компоненты покрытия, такие как мрамор, рутил, плавиковый шпат, слюда, ферро-марганец, ферро-сицилий, ферро-титан, каолин и другие, проходят операцию дробления на щековой дробилке. Компоненты повышенной влажности высушиваются во вращающемся барабане электрической вибрационной сушилки. Контроль параметров процесса сушки осуществляется автоматически. После измельчения готовые материалы складируются и хранятся в специальных емкостях.
Базирование компонентов производится на специальной линии строго в соответствии с составом покрытия каждой марки. Работа линии выполняется в автоматическом режиме. После дозировки при помощи вибротранспортера компоненты поступают в контейнер, который подается к смесителю, где происходит процесс перемешивания шихты в сухом виде, а затем с жидким стеклом, которые обычно представляют собой силикаты калия и натрия. Полученная обмазочная масса подается к брикетировочному прессу. Процесс брикетирования осуществляется под давлением 150 bar. После этого брикеты загружаются в цилиндр электродного пресса. Определенное давление при опрессовке обеспечивает качество электродов. Разность толщины покрытия – один из основных параметров, которые постоянно проверяются прессовщиком и ОТК.
Подсушенные на воздухе электроды подаются в камерную электрическую печь для термообработки. После этого электроды выгружаются, охлаждаются и сортируются по качеству поверхности покрытия. Затем их упаковывают в картонные коробки массой от 3кг до 5кг. Коробки укладываются на европоддон и формируются в пакеты с помощью стрейтч-пленки. В таком виде электроды отправляются на склад готовой продукции.
Сварочные электроды своими руками — как сделать правильно?
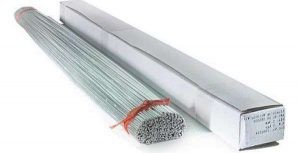
Сегодня электроды на прилавках магазинов присутствуют в огромном ассортименте. Поэтому очень трудно назвать их дефицитным и редким товаром.
Тем не менее, для общего ознакомления и ради интереса, можно попробовать сделать самодельные электроды, так сказать, в домашних условиях. В процессе изготовления электродов своими руками можно понять, как и из чего состоит сварочная обмазка, каким основным материалом изготовления, является стержень электрода.
Из чего сделать сварочные электроды своими руками
Основными материалами при изготовлении сварочных электродов, является следующие компоненты:
- Низкоуглеродистая проволока небольшого диаметра;
- Жидкое стекло;
- Мел в виде порошка, но можно использовать и известняк.
Итак, как уже становится понятным, стержень самодельных электродов будет изготовлен из стальной проволоки. Ее диаметр должен быть небольшим, в пределах 2-3 мм. В процессе изготовления электродов своими руками, проволоку придется нарезать на куски, длина которых должна составлять приблизительно 25 см.
Обмазка для самодельных электродов будет изготовлена из жидкого стекла и мела. Последний компонент, мел, если он в кусках, придется хорошенько растолочь до порошкообразного состояния. Более подробно, о том, как сделать электроды своими руками, можно будет прочесть ниже, в этой статье сайта про ручную дуговую сварку mmasvarka.ru.
Процесс изготовления самодельных электродов
В первую очередь нужно подготовить проволоку для электродов. Она должна быть сделана из низкоуглеродистой стали и нарезана на прутики по 25 см. Затем потребуется измельчить в порошок мел. При этом частицы порошка должны быть максимально мелкими и однородными.
Смешивать мел с жидким стеклом в процессе изготовления электродной обмазки не требуется. Достаточно будет взять кисточку и обмазать жидким стеклом стальные прутья. Затем необходимо будет несколько раз опустить электроды в мел, равномерно распределив его по поверхности проволоки.
Однако на этом изготовление электродов своими руками еще не окончено. После того, как самодельная обмазка подсохнет на проволоке, а обычно это происходит достаточно быстро, электроды нужно будет прокалить. Прокалку электродов осуществляют в электрической духовке, примерно около получаса при температуре в 100 градусов.
Конечно же, сделанные таким образом электроды своими руками не будут обладать высокими характеристиками. Скорее всего, при использовании, самодельные электроды будут прилипать к металлу или того хуже, плохо гореть.
Однако поэкспериментировав с настройками сварочного аппарата, все-таки, можно будет добиться хороших результатов. А как вы, пользовались когда-нибудь самодельными электродами из проволоки?
Поделиться в соцсетях
Принцип и технология производства сварочных электродов
Наверняка каждый сварщик задавался вопросом: какая все же технология производства сварочных электродов? Одни люди думают, что этот процесс слишком сложный, а другие считают, что производство электродов — это простой процесс, который производится очень быстро.Судить первое или второе мнение нельзя, потому что каждый человек имеет право на свое собственное мнение.
А теперь переходим к процессу изготовления сварочных электродов. Для того, чтобы начать производство электродов необходимо иметь следующие материалы: сварочная проволока, материалы для обмазки и силикатная глыба. К Вашему сведению: силикатная глыба бывает калиевой и натриевой.
Сырье, которое поступает на завод, складируется рабочими или роботами на специально отведенных для него площадках. На входе проводится проверка качества сырья. Если материал прошел проверку, по он получает сертификат и разрешение на использование в производстве сварочных электродов. Если же сырье признано неподходящего качества, то оно не отправляется в производственный цех.
Теперь переходим в изготовлению обмазки электродов. Все необходимые компоненты подвергаются дроблению на разные части, зависимо от назначения. Для этого используется валковая или щековая дробилка, которая обеспечивает качественное дробление всех частей будущего покрытия сварочных электродов.
После того, как все необходимые элементы были измельчены, они просеиваются через вибрирующееся сито (вибросито). После этого раздробленные и просеянные части покрытия электродов попадают на участок дозирования, где производится дозирование составных частей по ранее изготовленному рецепту. Потом уже готовая шихта попадает в смеситель.
Переходим к изготовлению стержней электродов. Для этого берется специальная сварочная проволока, которая проверена на наличие повреждений и других механических воздействий. Сварочная проволока в мотках подается на размоточные станки, которые сначала разматывают проволоку, а потом отрезают нужные куски, которые соответствуют длине электрода. Потом отрезанные куски проволоки попадают в обмазочный цех.
Для дальнейшего приготовления обмазки подвергают дроблению силикатную глыбу, которая в дальнейшем загружается в автоклав и заливается необходимым количеством воды. Когда из силикатной глыбы получилось стекло, оно попадает в отстойники.
Из отстойников оно попадает в смесители жидкого стекла. Если стекло соответствует всем требованиям — оно транспортируется в расходный бак. В расходном баке происходит смешивание ранее приготовленной смеси и жидкого стекла. После смешения происходит обпресовка электродов под давлением от 300 до 650 кгс/кв. см.
После обпресовки электроды проходят проверку на брак и там же происходит зачистка торцов. Потом электроды идут на маркировку и следующую за ней упаковку, а отходы бракоочистной машины попадают на переработку и изготовление следующей партии электродов.
1.Волочильный стан | ||
Наименование | Количество | Применение |
Диаметр катушки | 550мм | Используется для прокатки проволочного стержня до требуемого диаметра. |
Количество катушек | 6шт | |
Макс. диаметр входящей проволоки | 6.5мм | |
Мин. диаметр входящей проволоки | 2.0мм | |
Внешние габариты | 2200*1100*2150мм | |
Общая мощность | 18.5кВт | |
Вес | 1.8т | |
Шкаф управления | 1ш | |
2.Машина для отрезания проволоки | ||
Наименование | Количество | Применение |
Диапазон длины резки проволоки | 200-500мм | Используется для нарезания проволоки на нужную длину. |
Диаметр проволоки | 2-6мм | |
Скорость резки | 100шт/мин | |
Ход резки | 12мм | |
Мощность | 7кВт | |
Внешние габариты | 1750*650*1250мм | |
Вес | 0.9т | |
3.Машина для нарезания проволоки | ||
Наименование | Количество | Применение |
Диаметр подаваемой проволоки | 160мм | Применяется для подачи проволочного стержня в машину для нанесения на стержень порошка |
Скорость подачи проволоки | 145-395м/мин | |
Рабочая высота | 900мм | |
Общая мощность | 5.6кВт | |
Внешние габариты | 1495*728*1560мм | |
Вес | 1.5т | |
4.Машина гидравлического прессования порошка | ||
Наименование | Количество | Применение |
Макс. усилие прессования | 160(KN) | Применяется для подачи замешанного сырья в машину для нанесения порошка |
Макс.давление порошка | 18(MPa) | |
Диаметр порошкового цилиндра | Ø110×250(мм) | |
Высота рабочего стола | 1100(мм) | |
Мощность электродвигателя | 4(кВт) | |
Внешние габариты | 1350×800×1000(мм) | |
Вес | 1300(кг) | |
5.Гидравлическая машина для нанесения порошка | ||
Наименование | Количество | Применение |
Макс.давление | 655т | Служит для нанесения порошка на электрод |
Макс.гидравлическое давление | 20Mpa | |
Скорость подаваемого порошка | 0-3.6л/мин | |
Тип головки | 45° | |
Размер спрессованного куска | Φ100×650мм | |
Высота рабочей части оборудования | 990мм | |
Емкость топливного бака | 600л | |
Диаметр порошкового цилиндра | Φ132×760мм | |
Мощность | 7.5кВт | |
Внешние габариты | 2870×905×1668мм | |
Вес | 2.7т | |
6.Машина для шлифовки концов электрода | ||
Наименование | Количество | Применение |
Диаметр электрода | φ3.2-5.8мм | Применяется для шлифовки концов электрода. |
Длина электрода | 350-400мм | |
Рабочая скорость | 9.8-14.7м/мин | |
Общая мощность | 5.2кВт | |
Внешние габариты | 4300×1500×1400 | |
Вес | 1.2т | |
7.Циркуляционная сушильная печь | ||
Наименование | Количество | Применение |
Макс. рабочая температура | 450℃ | Применяется для сушки электродов. Источником питания может быть какуголь, природный газ, так и электричество. |
Макс. мощность нагрева | 170000Ккал/ч | |
Погрешность нагрева | <±5℃ | |
Производительность сушилки | 8т/8ч | |
Установленная мощность | 60кВт | |
Внешние габариты | 2500*2100*2550мм | |
Шкаф управления | 1ш | |
8.Машина для смешивания порошка | ||
Наименование | Количество | Применение |
Объем резервуара | 300л | Используется для смешивания порошка |
Общая мощность | 7.5кВт | |
Внешние габариты | 2069×1463×1920 | |
Вес | 2.5т | |
9.Буквопечатающий аппарат | ||
Наименование | Количество | Применение |
Скорость вращения | 18-130обр/мин | Служит для нанесения этикетки и модели на электрод. |
Мощность | 0.18кВт | |
Внешние габариты | 650×530×550 | |
Вес | 0.05т | |
10.Машина для восстановления электродного стержня и порошка | ||
Наименование | Количество | Применение |
Макс.длина обработки | 450мм | Служит для соскабливания порошка электрода после сушки. |
Диаметр обработки | 1.6-5.0мм | |
Производительность | 15-20кг/раз | |
Объем восстанавливающего бокса | 0.03м³ | |
Внешние габариты | 927*815*977 | |
Вес | 320кг | |
Мощность | 1.5кВт | |
11.Правильный станок | ||
Наименование | Количество | Применение |
Диаметр обработки | 1.6-5.0мм | Служит для выправления проволоки. |
Скорость вращения главной оси | 15обр/мин | |
Высота рабочей части оборудования | 850мм | |
Внешние габариты | 1200*450*1020 | |
Вес | 0.6т | |
12.Машина для очистки от ржавчины | ||
Наименование | Количество | Применение |
Количество дисков для удаления ржавчины | 4 | Применяется для удаления налета или оксидного слоя с поверхности катушки с проволочным стержнем. |
Рабочая высота | 820мм | |
Внешние габариты | 600×500×850мм | |
Вес | 0.1т | |
13.Станок для придавливания кончика проволоки | ||
Наименование | Количество | Применение |
Макс. диаметр подаваемой проволоки | Φ6.5мм | Служит для придавливания кончика проволоки, для более удобного ввода проволоки в волочильный стан. |
Мин. диаметр подаваемой проволоки | Φ2мм | |
Мощность | 3кВт | |
Внешние габариты | 520×480×1200мм | |
Вес | 0.2т | |
14.Сварочная машина | ||
Наименование | Количество | Применение |
Диаметр стыкового шва | Φ2-6.5мм | Служит для сварки двух концов проволоки, что обеспечивает непрерывных ход проволоки через волочильный стан. |
Номинальная емкость | 10кВА | |
Количество степеней регулирования | 7 | |
Внешние габариты | 550×450×1200мм | |
Вес | 0.15т | |
15.Упаковочная машина | ||
Наименование | Количество | Применение |
Размер (Д*Ш*В) | L895*565*730мм | Служит для упаковки электродов. |
Ширина упаковки | 9-16мм(регулируется) | |
Вес | Примерно 85кг | |
Электропитание | 110/220В.50/60Гц | |
16.Измерительный прибор | ||
Наименование | Количество | Применение |
Принцип измерения | магнитный | Применяется для измеренияэксцентричности поверхности электродов. |
Диапазон измерений | Φ2.0-Φ5.8мм | |
Рабочая температура | 10℃~40℃ | |
Диапазон измерений | 30-0-30 | |
Внешние габариты | 350×250×300мм | |
Вес | 5кг | |
17.Подъемный кран | ||
Наименование | Количество | Применение |
Высота подъема | 3м | Служит для доставки нарезанных электродов в резервуар для хранения электродов. |
Скорость подъма | 7.81м/мин | |
Максимальная нагрузка | 0.35т | |
Мощность | 1.5кВт | |
Внешние габариты | 1200×350×3200мм | |
Вес | 0.4т | |
18.Конвейер | ||
Наименование | Количество | Применение |
Диапазон диаметров | 1.6-5.8мм | Служит для доставки электродов от гидравлической машины для нанесения порошка в машину для шлифовки концов электрода. |
Скорость конвейера | 225-467м/мин | |
Угол вращения | 18 | |
Регулируемый угол подъема | 0-12 | |
Мощность электродвигателя | 1.1кВт | |
Внешние габариты | 1200*450*1000 | |
1600*450*1000 | ||
Вес | 0.5т | |
19.Вспомогательное оборудование | ||
Наименование | Характеристика | |
Мощность | 2,2kw | |
Габариты | 3500*650*640 | |
Вес | 0,35t | |
20.Главный шкаф управления | ||
Наименование | Характеристики | |
Рабочая обстановка | ~380V,50Hz | |
Габариты | 1000*30*1500 | |
Вес | 75kg | |
21.Термоусадочная упаковочная машина | ||
Наименование | Характеристики | |
Пределы температуры | 40-180градусов | |
Мощность нагрева | 1.5kw*6 | |
Скорость подачи | 2-15m/min | |
Длина зоны нагрева | 2200mm | |
Габариты | 3000×530×1650mm | |
Вес | 85kg | |
ПРИМЕЧАНИЕ: 1.Для транспортировки оборудования с производительностью 1 тонна понадобится один контейнер 40 футов и один контейнер 20 футов. 2.Для проведения таких работ необходимо отправить с завода 2 инженеров, от вас необходима оплата их перелетов в обе стороны, виз, предоставление жилья, питании и оплаты труда в размере 70 долларов США в день каждому. Для таких работ понадобится примерно 10-15 дней. 3.Гарантийный срок 12 месяцев, в этот период бесплатно предоставляются необходимы детали (за исключением поломок из-за неправильного использования оборудования) 4.Необходимое количество работников: 5-6 человек. 5.Размеры помещения: 52*8*3 метров(длина*ширина*высота) 6.Для изготовления 1000 кг электродов порошковое сырье составляет 300-350 кг, проволока 650-700 кг. Расход электроэнергии: примерно 70KW/8 часов Расход воды: незначительный расход жидкости на охлаждение. 7 Для изготовления 1000 кг электродов порошковое сырье составляет 300-350 кг, проволока 650-700 кг. Мы также предоставляем производственные линии с производительностями 3 тонны/8 часов, 5 тонн/8 часов, 10 тонн/8 часов, при необходимости вы всегда можете оставить свой запрос на них. |
НПО Спецэлектрод производство сварочных электродов. Электродный завод
ООО «НПО Спецэлектрод»– производство сварочных электродов.
Общество с ограниченной ответственностью «Научно-производственное объединение Спецэлектрод» — предприятие по производству и разработке сварочных (наплавочных) электродов специального назначения для сварки сталей различных классов, цветных металлов и сплавов.
ООО «НПО Спецэлектрод» является ведущим поставщиком сварочных электродов в России и на сегодняшний день специализируется по производству и продаже следующих марок сварочных электродов:
Электроды для сварки углеродистых и низколегированных сталей:
АН-Х7, АНГ-1, АНО-1, АНО-10, АНО-11, АНО-12, АНО-13, АНО-13М, АНО-14, АНО-15, АНО-16, АНО-17, АНО-18, АНО-19, АНО-20, АНО-21, АНО-23, АНО-24, АНО-25, АНО-26, АНО-27, АНО-29, АНО-29М, АНО-3, АНО-30, АНО-32, АНО-33, АНО-34, АНО-4, АНО-4Ж, АНО-5, АНО-6, АНО-6М, АНО-7, АНО-8, АНО-9, АНО-Д, АНО-Дс, АНО-Т, АНО-ТМ, АНО-ТМ/Н, АНО-ТМ/СХ, АНО-ТМ60, ВМ-10, ВМ-12, ВМ-9, ВН-48, ВН-48У, ВП-4, ВП-6, ВПТИ-12/700 ВСН-3, ВСО-50СК, ВСП-1, ВСП-2, ВСП-3, ВСФ-50, ВСФ-60, ВСФ-65, ВСФ-65У, ВСЦ-1, ВСЦ-2, ВСЦ-3, ВСЦ-4, ВСЦ-4А, ВСЦ-60, ДСК-50, ДСК-50У, ЖС-4, ЗРС-1, ЗРС-2, ЗТМ-2У, ИТС-1, ИТС-4, ИТС-4С, К-5А, КД-11, КПЗ-32Р, ЛКЗ-6, ЛКИ-1П, МИТ-2, МР-1, МР-3, НЭ-1, НЭ-2, НЭ-46, НЭ-5, НЭ-5М, НЭ-5М1, ОЗС-12, ОЗС-16, ОЗС-17Н, ОЗС-18, ОЗС-2,ОЗС-20Н, ОЗС-20Р, ОЗС-21, ОЗС-22Н, ОЗС-22Р, ОЗС-23, ОЗС-24, ОЗС-24М, ОЗС-25, ОЗС-27, ОЗС-28, ОЗС-29, ОЗС-3, ОЗС-4, ОЗС-5, ОЗС-6, ОЗС-6С, ОЗС-7, ОЗС-8, ОЗС-9, ОЗС-9В, ОМА-2, ОММ-5, РБУ-4, РБУ-5, СК2-50, СМ-11, СМ-5, ТМУ-21, ТМУ-21У, У-340/55, У-340/65, УИМ-1, УИМ-2, УНЛ-1, УОНИ 13/45, УОНИ 13/45А, УОНИ 13/55К, УОНИ-13/55У, УОНИ-13/65, УОНИИ-13/55, УП-1/45, УП-1/55, УП-2/45, УП-2/55, ЦМ-7, ЦМ-9, ЦУ-1, ЦУ-5, ЦУ-6, ЦУ-7, ЦУ-7А, ЦУ-8, ЦЦ-1, Э-138/45Н, Э-138/50Н, ЭЛУР-10, ЭЛУР-12, ЭЛУР-2, ЭПС-АН1
Электроды для сварки легированных сталей:
АН-ХН6, АН-ХН7, АНВ-70, АНО-ТМ70, АНП-1, АНП-2, АНП-6П, ВИ-10-6, ВСФ-75, ВСФ-75У, ВСФ-85, ЛКЗ-70, НИАТ-3, НИАТ-3М, НИИ-3М, ОЗШ-1, ОЗШ-1У, У-340/105, УОНИ-13, УОНИ-13/85, УОНИ-13/85У, УОНИ-13В, ЦЛ-18, ЦЛ-19
Электроды для сварки легированных теплоустойчивых сталей:
ГЛ-14, ЗИО-20, ЛКЗ-70М, Н-1, Н-10,Н-11, Н-2, Н-20, Н-25, Н-28, Н-3, Н-6, НЗЛ/СХ6М, ОЗС-11, ПТ-30, РТ-45А, ТМЛ-1, ТМЛ-1У, ТМЛ-2, ТМЛ-3, ТМЛ-3У, ТМЛ-4В, УОНИ-13/15М, УОНИ-13/45МХ, УОНИ-13ХМ, ЦЛ-12, ЦЛ-13, ЦЛ-14, ЦЛ-17, ЦЛ-20А, ЦЛ-20Б, ЦЛ-21, ЦЛ-26М, ЦЛ-27А, ЦЛ-27Б, ЦЛ-30, ЦЛ-36, ЦЛ-38, ЦЛ-39, ЦЛ-40, ЦЛ-45, ЦЛ-47, ЦЛ-48, ЦЛ-55, ЦЛ-58, ЦЛ-59, ЦЛ-6, ЦЛ-7, ЦУ-2М, ЦУ-2МХ, ЦУ-2ХМ
Электроды для сварки высоколегированных сталей и сплавов:
АНВ-1, АНВ-13, АНВ-17, АНВ-20, АНВ-23,АНВ-24, АНВ-29,АНВ-32, АНВ-34, АНВ-35, АНВ-36, АНЖР-1, АНЖР-2, ВИ-12-6, ГЛ-2, ЗИО-3, ЗИО-7, ЗИО-8, ЗИФ-1, ЗИФ-9, ИМЕТ-10, КТИ-10, КТИ-9, КТИ-5, КТИ-7, КТИ-7А, КТИ-9А, Л-38М, Л-39, Л-40М, ЛМЗ-1, Н-48, НБ-38, НЖ-13, НИАТ-1, НИАТ-5, НИИ-48Г, НИИ-75, ОЗЛ-12, ОЗЛ-14, ОЗЛ-14А, ОЗЛ-19, ОЗЛ-20, ОЗЛ-21, ОЗЛ-22, ОЗЛ-25, ОЗЛ-25Б, ОЗЛ-29, ОЗЛ-3, ОЗЛ-36, ОЗЛ-4, ОЗЛ-5, ОЗЛ-6, ОЗЛ-7, ОЗЛ-8, ОЗЛ-9, ОЗЛ-9-1, ОЗЛ-9А, СЛ-16, СЛ-25, СЛ-28, УОНИ-13/НЖ, УОНИ-13/НЖ-2, УОНИ-13/НЖ-К, УОНИ-13/ЭП-56, ЦЛ-10, ЦЛ-11, ЦЛ-25, ЦЛ-25/2, ЦЛ-32, ЦЛ-33, ЦЛ-4, ЦЛ-41, ЦЛ-9, ЦТ-1, ЦТ-10, ЦТ-15, ЦТ-15-1, ЦТ-15К, ЦТ-17, ЦТ-26, ЦТ-26-1, ЦТ-28, ЦТ-36,ЦТ-46, ЦТ-50, ЦТ-7, ЦТ-7-1, ЭА-395/9, ЭА-400/10Т, ЭА-400/10У, ЭА-400/13, ЭА-48М/22, ЭА-606/10, ЭА-606/11, ЭА-855/51, ЭА-898/19, ЭА-902/14, ЭА-981/15, ЭНТУ-3М
Электроды для сварки нержавеющих высокохромистых сталей и сплавов:
АНВ-2, ЦЛ-51, ЦЛ-56, ЦЛ-57, ЦЛ-60, ЭА-908/54
Электроды для сварки корозионностойких аустенитных сталей и сплавов:
15М, 48А-1, 48А-2, АНВ-18, АНВ-26, АНВ-28, АНВ-3, ГИАП-4, ДС-12, НИАТ-6, НИАТ-6АМ, ОЗЛ-10, ОЗЛ-11, ОЗЛ-13, ОЗЛ-17, ОЗЛ-17У, ОЗЛ-23, ОЗЛ-24, ОЗЛ-26А, ОЗЛ-37-1, ОЗЛ-37-2, ОЗЛ-40, ОЗЛ-41, ХН-1, ЦТ-24, ЦТ-45, ЦТ-49, ЭА-898/21
Электроды для сварки жаростойких аустенитных сталей и сплавов:
ГС-1, ИМЕТ-4, ИМЕТ-4П, ОЗЛ-16/АНЖ, ОЗЛ-18, ОЗЛ-2, ОЗЛ-31, ОЗЛ-31М/ЦТ, ОЗЛ-35, ОЗЛ-38, ОЗЛ-39, ОЗЛ-6-1
Электроды для сварки жаропрочных аустенитных сталей и сплавов:
АЖ-13-15, АЖ-13-18, ВИ-ИМ-1, КТИ-7К, НИАТ-7, НИАТ-8, НИАТ-8А, ОЗЛ-42, ЦТ-13, ЦТ-16, ЦТ-16-1, ЦТ-22, ЦТ-23, ЦТ-25, ЦТ-48, ЦТ-5
Электроды для сварки разнородных сталей:
АНВ-27, АНЖР-3У, ОЗЛ-27, ОЗЛ-28, ОЗЛ-30, ОЗЛ-32, ОЗЛ-44, ОЗЛ-45/ЦТ, ЦЛ-8, ЭА-464/5А, ЭА-48М/16
Электроды для наплавки:
12АН/ЛИВТ, 13КН/ЛИВТ, ВСН-6, НР-70, ОЗИ-3, ОЗИ-5, ОЗИ-6, ОЗН-300, ОЗН-400, ОЗН-6, ОЗН-7, ОЗН-7М, ОЗШ-2, ОЗШ-3, ОЗШ-6, ОЗШ-7, ОЗШ-8, ОМГ-Н, Т-590, Т-620, УОНИ-13/НЖ/20Х13, ЦН-12М, ЦН-16, ЦН-2, ЦН-6Л, ЦНИИН-4, ЭН-60М, ЭНУ-2
Электроды для сварки и наплавки цветных металлов и сплавов:
АНЦ-3, АНЦ/ОЗМ-2, АНЦ/ОЗМ-3, АНЦ/ОЗМ-4, Комсомолец-1, Комсомолец-100, ЛКЗ-АБ (АМц 9-2), ЛКЗ-АБ (АНМцЖ 8-3-4-1), ЛКЗ-АБ/БрАЖНМц, ЛКЗ-АБ/БрАМц, ЛПИ-73/БрАЖНМц, ЛПИ-73/БрАМц, НИК-2, ОЗА-1, ОЗА-2, ОЗАНА-1, ОЗАНА-2, ОЗБ-1, ОЗБ-2М, ОЗБ-3, УАНА-1
Электроды для сварки и наплавки чугуна:
АНЧ-1, В-56У, МНЧ-2, МНЧ-КС-1, ОЗЖН-1, МНЧ-1, ОЗЧ-1, ОЗЧ-2, ОЗЧ-3, ОЗЧ-4, ОЗЧ-6, ОР-601, ЦЧ-4, ЦЧ-4А, ЧФ-3, ЧФ-9, ЭЛУР-Ч1
Электроды для резки сталей:
АНДР-1, АНР-2, АНР-2М, АНР-2М-З, АНР-3, АНР-4, ОЗР-1, ОЗР-2, ЭВ-1, ЭЛЗ-Р-1
Легированная сварочная проволока:
Св-08А, Св-08АА, Св-08ГМ, Св-08ГНМ, Св-08ХМ, Св-08Г1НМА, Св-08ГА, Св-10ГН, Св-08ГСНТ, Св-08ГСМТ, Св-08ХГСМФА, Св-04Н3ГСМТА, Св-04Н3ГМТА, Св-10НМА
Высоколегированная сварочная проволока (нержавеющая):
Св-01Х23Н28М3Д3Т (ЭП516), Cв-04Х19Н11М3, Св-04Х19Н9, Св-04Х19Н9С2, Св-05Х20Н9ФБС (ЭИ649), Св-05Х20Н9ФБС(ЭИ649), Св-06Х19Н9Т, Св-07Х19Н10Б, Св-07Х25Н12Г2Т(ЭП75), Св-07Х25Н13, Св-08Х19Н10Г2Б (ЭИ898),Св-08Х20Н9Г7Т, Св-08Х21Н10Г6 (ЭИ478), Св-10Х16Н25АМ6(ЭИ395), Св-10Х17Т (ЭИ645), Св-12Х13, Св-13Х25Т (ЭИ439), Св-20Х13, Cв-30Х25Н16Г7, Св-01Х12Н2ВИ (ЭП792ВИ), Св-10Х14Г14Н4Т (ЭИ711)
Высоколегированная сварочная проволока (жаропрочная):
Св-06Х15Н60М15 (ЭП367), Св-08Х25Н40М7 (ЭП673), Св-08Х25Н60М10 (ЭП606), Св-ХН78Т (ЭИ435)
ООО «НПО Спецэлектрод» профессиональный поставщик сварочного оборудования и сварочных электродов в России
производство электродов изготовление электродов нержавеющие электроды нержавеющие наплавочные спецэлектроды электроды сварка
7 лучших сварочных электродов
Обзор лучших электродов для ручной сварки углеродистых и коррозионно-стойких сталей составлен при использовании публикаций журналов «Сварка и диагностика», «Металлургический бюллетень» и других специализированных источников. В статье обобщены интернет-отзывы профессиональных сварщиков о продукции разных производителей.
Критерии отбора
К сожалению, российские электроды проигрывают многим зарубежным аналогам по большинству параметров. Однако «прорывы» в этой области уже наметились. Российская электродная продукция, выпускаемая на немногочисленных пока совместных предприятиях, по стабильности качества уже не уступает многим маститым брендам. Начали «подтягиваться» к ним и некоторые заводы отечественной подчиненности. Однако в случаях, когда требуется уверенно обеспечить высокое качество шва, профессионалы по-прежнему предпочитают использовать более дорогие, но и более качественные электроды зарубежного производства. Для сварочных инверторов подходят электроды любого типа, для сварочных аппаратов переменного тока подходят не все типы.
При выборе лучших электродов для обзора мы руководствовались следующими критериями:
- объемы производства;
- качество продукции;
- попадание производителя в обзоры по электродной промышленности;
- отзывы профессионалов.
Для корректности сравнения цен мы включили в обзор только самый часто применяемые электроды диаметром 3 мм.
Основным параметром любого сварочного электрода, определяющим большинство его свойств – от легкости розжига до качества шва – является состав его обмазки. Наиболее распространенными сегодня являются следующие виды обмазок:
- Рутиловые электроды (и электроды со смешанной обмазкой на этой основе – рутилово-целлюлозные и так далее) стали одними из самых популярных благодаря легкости розжига, в том числе и повторного, сниженной (в разумных пределах) чувствительности к отсыреванию. Они могут использоваться и на переменном, и на постоянном токе во всех направлениях шва, но при выборе рутилового электрода нужно быть внимательным – можно купить как хороший электрод, так и загрязняющий шов огромным количеством шлаковых язв, пригодный разве что для прихваток.
- Электроды с основным покрытием чаще всего используются при сварке постоянным током в особо ответственных местах. При горении обмазки в большом количестве выделяется углекислый газ, надежно защищающий сварочную ванну от воздействия кислорода. Сам шов получается более пластичным, чем при сварке распространенными типами рутиловых электродов. Обратная сторона медали – это повышенная чувствительность к влажности и затрудненный розжиг: варить такими электродами заметно труднее.
Правильный выбор электрода требует учитывать многие факторы. К примеру, при необходимости сварить сталь с высоким содержанием углерода многие сварщики посоветуют Вам электроды УОНИ – но не факт, что в неопытных руках из получится что-то хорошее. Вместе с тем более удобные в работе электроды наподобие ОЗС-12 позволят получить более качественный результат – но только до того момента, когда Вы не освоите сварку более сложными в работе типами электродов.
Нужно учитывать и условия хранения: держать в гараже большинство типов электродов с основным покрытием значит обречь себя на постоянный и длительный прожиг обмазки перед сваркой, которая сама может занимать буквально несколько минут, и рутиловые электроды в таком случае будут более предпочтительными, особенно типы с самой низкой температурой прокалки (ESAB OK 46.00, Omnia 46).